Top 20 Industrial IoT (IIoT) Applications Transforming Industry 4.0 in 2025
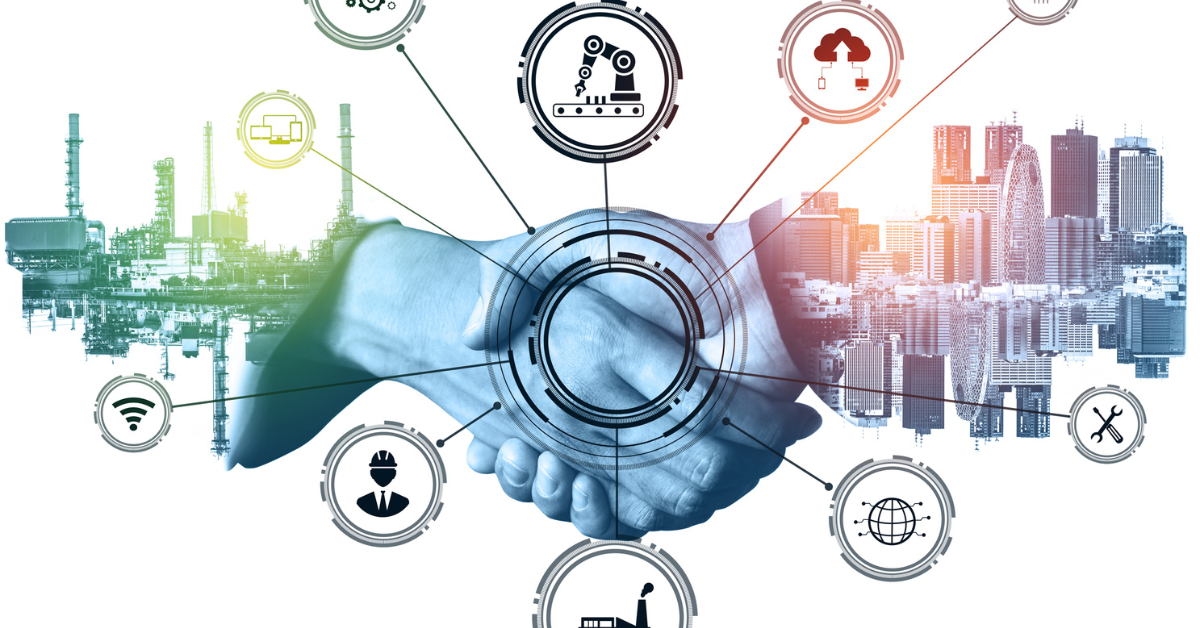
The Industrial Internet of Things (IIoT) isn't just hype — it's the steel backbone of Industry 4.0. From predictive maintenance to digital twins, IIoT is revolutionizing how factories, plants, and logistics operate, ushering in an era of unprecedented efficiency, safety, and innovation.
Why IIoT is Transforming Industries
The power of IIoT lies in its ability to connect machines, sensors, and operational technology (OT) with information technology (IT) systems. This seamless integration allows for:
- Real-time data collection and analysis: Imagine sensors on a factory floor constantly monitoring machine performance, temperature, and vibration. IIoT makes this possible, feeding crucial data into analytics platforms for immediate insights.
- Predictive maintenance: Instead of waiting for equipment to break down (costing valuable time and money), IIoT-enabled sensors can detect subtle anomalies, allowing for maintenance to be scheduled proactively. This minimizes downtime, extends asset lifespan, and reduces operational costs.
- Enhanced operational efficiency: By optimizing processes based on real-time data, companies can reduce waste, improve resource allocation, and streamline workflows. Think of smart warehouses that automatically track inventory and optimize routes for forklifts.
- Digital twins: These virtual replicas of physical assets, processes, or systems are powered by IIoT data. They allow engineers to simulate scenarios, test changes, and predict performance without impacting real-world operations, leading to faster innovation and problem-solving.
- Improved safety and compliance: Monitoring environmental conditions, equipment health, and even worker movements through IIoT can help prevent accidents and ensure adherence to safety regulations.
- Supply chain optimization: IIoT provides end-to-end visibility across the supply chain, from raw material sourcing to delivery. This enables better tracking, demand forecasting, and inventory management, leading to more resilient and responsive logistics.
Whether you’re an engineer, entrepreneur, or a curious innovator, understanding and embracing IIoT is crucial. It's not just about adopting new technologies; it's about fundamentally rethinking how industries create value.
⚙️ Industry 4.0 isn't coming. It's already here — and IIoT is the pulse, driving intelligent automation, interconnected systems, and data-driven decision-making across every sector.
🧠 Structure of Each Application (format):
- Name of Application
- Overview
- Use Case
- Tech Stack
- Impact/ROI
- Real-World Example
Table of Content:
- Zero-Downtime Predictive Engines (Sentinel AI)
- AI-Driven Dynamic Workflow Orchestration (SynapseFlow AI)
- Industrial Exoskeleton Data Interfaces ( AuraFit )
- Swarm Robotics Coordination Systems (HiveMind Robotics)
- Hyperlocal Environmental Compliance Trackers (AuraGuard)
- Self-Healing Factory Networks (NeuroMesh Industrial)
- Real-Time Worker Safety Geo-Zoning (SentinelZone Safety)
- Process-Aware Digital Twins (AuraTwin Dynamics)
- AI-Optimized Material Flow Systems (FlowSense AI)
- Smart Power Load Shedding Networks (GridGuardian AI)
- Augmented Industrial Field Support via AR IoT (VisionPro Assist)
- Post-Quantum Secure Industrial Networks (QuantumFortress Industrial)
- Edge Intelligence for Hazard Detection (SentinelEdge AI)
- Zero-Touch Industrial Onboarding Protocols (AutoConnect Pro)
- Cognitive Supply Chain Sensors (SynapseChain)
- Cyber-Physical Intrusion Prevention Systems (SentinelX Industrial Guard)
- Smart Lubrication Systems for Heavy Machinery (LubeSense AI)
- Microgrid-Synced Industrial Controllers (GridHarmony Industrial)
- Autonomous Reconfiguration of Industrial Layouts (GridHarmony Industrial)
- Drone-Assisted Infrastructure Audits (SkyInspect AI)
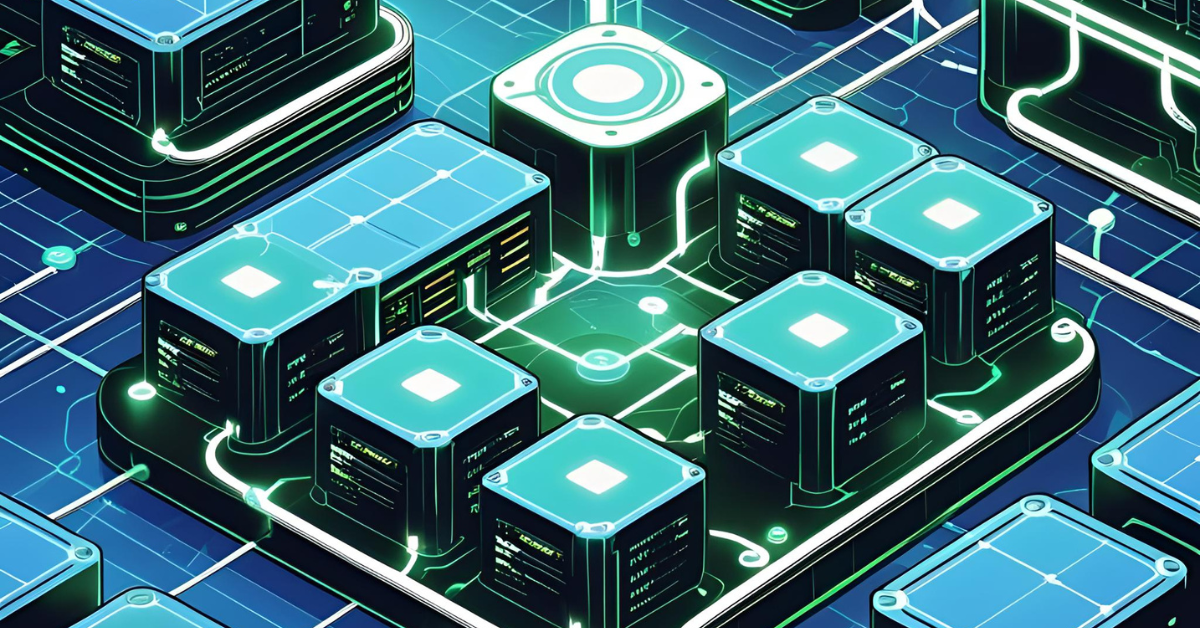
1.Zero-Downtime Predictive Engines
Application Name: Sentinel AI
Overview:
Sentinel AI represents a revolutionary leap in industrial asset management. It's an advanced, Zero-Downtime Predictive Engine that leverages cutting-edge Machine Learning (ML) and Artificial Intelligence (AI) models to continuously monitor industrial equipment. Unlike traditional scheduled maintenance or reactive repair, Sentinel AI's ML-fueled models "never sleep," constantly analyzing real-time sensor data to forecast machine failures weeks, even months, before they occur. This proactive approach transforms maintenance from a cost center into a strategic advantage, leading to unprecedented uptime and operational efficiency. Sentinel AI is the ultimate guardian of your critical assets, delivering true "uptime nirvana."
Use Case:
Sentinel AI is designed for industries where equipment downtime is highly costly and disruptive, and where continuous operation is paramount. Key use cases include:
- Manufacturing Facilities: Monitoring production lines, robotics, CNC machines, and critical infrastructure to prevent unexpected breakdowns that halt production.
- Energy Sector (Oil & Gas, Power Generation): Ensuring the continuous operation of turbines, generators, pumps, compressors, and pipeline infrastructure.
- Transportation & Logistics: Predicting failures in fleet vehicles, railway systems, and port machinery to avoid service interruptions and ensure timely deliveries.
- Mining & Heavy Industry: Monitoring heavy machinery like excavators, conveyors, and crushers in harsh environments to prevent costly downtime and ensure worker safety.
- Data Centers: Predicting failures in cooling systems, power supply units, and servers to maintain uninterrupted service and data integrity.
Tech Stack:
The robust architecture of Sentinel AI relies on a sophisticated blend of technologies:
- Data Ingestion & Processing:
- Edge Devices/Gateways: Industrial IoT (IIoT) sensors (vibration, temperature, pressure, current, acoustic, etc.) connected to ruggedized edge gateways for local data aggregation and initial processing (e.g., Siemens Industrial Edge, AWS IoT Greengrass).
- Message Brokers: Apache Kafka or RabbitMQ for high-throughput, real-time data streaming from edge to cloud.
- Data Lakes: Apache Hadoop HDFS or cloud-based solutions like Amazon S3, Google Cloud Storage, or Azure Data Lake Storage for storing vast quantities of raw and processed sensor data.
- Time-Series Databases: InfluxDB, TimescaleDB, or Amazon Timestream optimized for storing and querying high-volume time-series data from sensors.
- Machine Learning & AI Core:
- ML Frameworks: TensorFlow, PyTorch, Scikit-learn for building, training, and deploying sophisticated predictive models.
- Model Types:
- Anomaly Detection: Isolation Forests, One-Class SVMs, Autoencoders for identifying deviations from normal operating patterns.
- Time-Series Forecasting: LSTMs (Long Short-Term Memory networks), GRUs (Gated Recurrent Units), Prophet, ARIMA for predicting future sensor values and identifying trends.
- Classification: Support Vector Machines (SVMs), Random Forests, XGBoost for classifying fault types.
- Deep Learning: Convolutional Neural Networks (CNNs) for signal processing (e.g., analyzing vibration signatures).
- MLOps Platforms: Kubeflow, MLflow, AWS SageMaker, Google Cloud AI Platform, Azure Machine Learning for managing the ML lifecycle (experimentation, versioning, deployment, monitoring).
- Cloud Platform & Infrastructure:
- Cloud Providers: AWS, Google Cloud Platform (GCP), Microsoft Azure for scalable compute, storage, and networking.
- Containerization & Orchestration: Docker and Kubernetes for deploying and managing microservices and ML models at scale.
- Serverless Computing: AWS Lambda, Google Cloud Functions, Azure Functions for event-driven processing and scalable backend services.
- Analytics & Visualization:
- BI Tools: Grafana, Tableau, Power BI for interactive dashboards and reporting on asset health, predictions, and maintenance schedules.
- Custom User Interface (UI): React, Angular, or Vue.js for a bespoke, intuitive web application for maintenance teams and operators.
- Integration:
- APIs: RESTful APIs for seamless integration with existing Enterprise Asset Management (EAM) systems, Computerized Maintenance Management Systems (CMMS), ERPs (e.g., SAP), and SCADA systems.
Impact/ROI:
Implementing Sentinel AI delivers a profound and measurable return on investment (ROI) through multiple avenues:
- Significant Reduction in Downtime: Up to 70% reduction in unplanned downtime, leading to increased production capacity and revenue.
- Optimized Maintenance Costs:
- Reduced Emergency Repairs: Eliminates costly rush orders for parts and overtime for emergency repairs.
- Fewer Asset Failures: Extends the lifespan of critical machinery by addressing issues before they become catastrophic.
- Efficient Resource Allocation: Maintenance teams can transition from reactive firefighting to planned, efficient interventions.
- Increased Production Throughput: Consistent operation of machinery ensures higher output and meets demand more reliably.
- Enhanced Safety: Predicting failures in critical equipment reduces the risk of hazardous incidents and improves worker safety.
- Improved Asset Utilization: Maximizes the operational time and efficiency of high-value assets.
- Better Inventory Management: Predictable maintenance allows for just-in-time ordering of spare parts, reducing inventory holding costs.
- Competitive Advantage: Companies leveraging Sentinel AI gain a significant edge through superior operational reliability and lower costs.
Real-World Example:
Consider a large-scale automotive manufacturing plant utilizing Sentinel AI.
Before Sentinel AI: The plant experienced frequent, unscheduled breakdowns of critical robotic arms on its assembly line, leading to production halts, missed deadlines, and significant overtime costs for emergency repairs. A single unexpected breakdown could cost the plant hundreds of thousands of dollars per hour in lost production. Maintenance was largely reactive or based on time-based schedules, often replacing parts too early or too late.
With Sentinel AI:
- Sensors: Hundreds of IIoT sensors (vibration, temperature, motor current, acoustic) are installed on each robotic arm and its associated components.
- Data Collection: This data is continuously streamed to the cloud via edge gateways.
- Predictive Models: Sentinel AI's ML models analyze this vast stream of data in real-time.
- Early Warning: For instance, the system detects subtle, escalating vibration patterns in a specific robot's joint weeks before it would traditionally fail.
- Actionable Insight: Sentinel AI flags the anomaly, predicts a high probability of failure for that specific joint within the next 10-14 days, and suggests the likely root cause.
- Planned Maintenance: The plant's maintenance team receives an automated alert and uses this window of opportunity to schedule a replacement of the failing joint during a planned, brief maintenance window (e.g., during a shift change or a scheduled weekend shutdown), rather than waiting for an unexpected breakdown.
Result:
The automotive plant virtually eliminates unplanned downtime due to robot failures on its assembly line. They save millions annually by avoiding lost production, reducing emergency repair costs, and extending the overall lifespan of their robotic fleet. The maintenance team shifts from a crisis management mode to a strategic, proactive one, improving job satisfaction and efficiency.
🚀 Ready to turn your passion for connected tech into real-world impact?
At Huebits, we don’t just teach IoT — we train you to build smart, scalable, and data-driven systems using the tech stacks powering today’s most innovative industries.
From edge devices to cloud platforms, you’ll gain hands-on experience designing end-to-end IoT architectures that collect, analyze, and respond in real time — built for deployment in cities, farms, factories, and homes.
🧠 Whether you're a student, aspiring IoT engineer, or future smart systems architect, our Industry-Ready IoT Program is your launchpad.
Master Python, Embedded C, MQTT, REST APIs, ESP32, Raspberry Pi, AWS IoT, Azure IoT Hub, and Grafana — all by building real-world IoT solutions that deliver results, not just data.
🎓 Next Cohort Starts Soon!
🔗 Join now and claim your seat in the IoT revolution powering tomorrow’s ₹1 trillion+ connected economy.
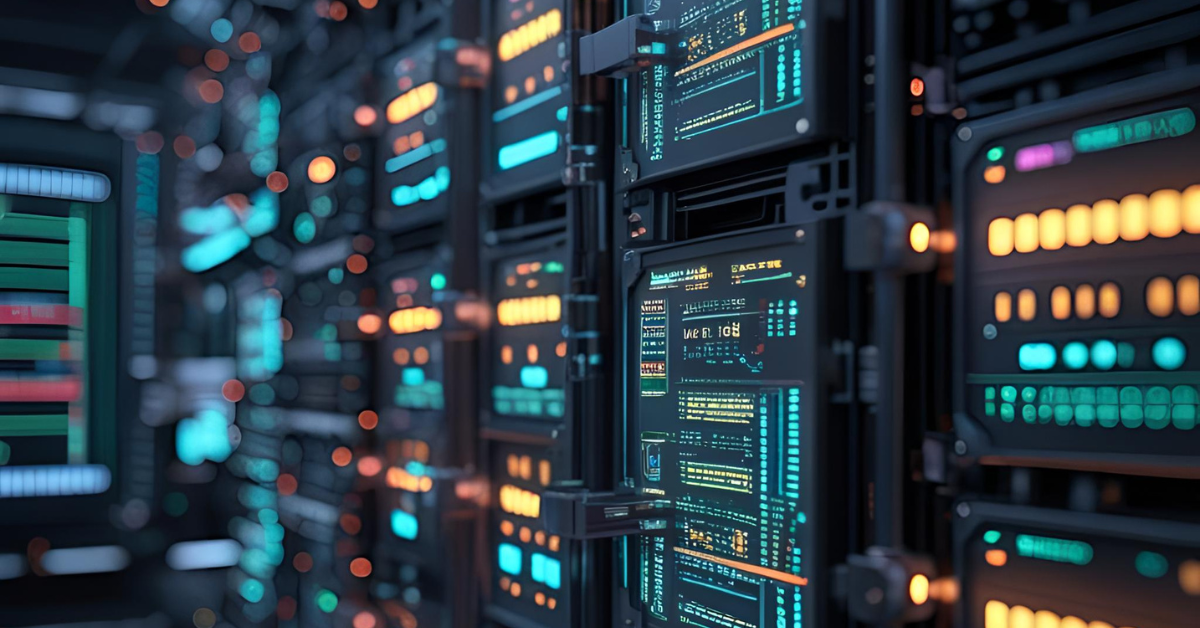
2.Industrial Exoskeleton Data Interfaces
Application Name: SynapseFlow AI
Overview:
SynapseFlow AI is the intelligent central nervous system for the modern digital factory. It is an advanced AI-Driven Dynamic Workflow Orchestration platform that moves beyond static, pre-programmed processes. By ingesting and analyzing real-time data from a multitude of sources—including industrial IoT (IIoT) sensors, wearable devices, robotics, logistics systems, and even external market indicators—SynapseFlow AI intelligently adjusts and optimizes industrial workflows on the fly. Think of it as the conductor of your digital factory, continuously harmonizing operations, mitigating disruptions, and maximizing efficiency by making autonomous, data-driven decisions that adapt to ever-changing conditions. This leads to unprecedented agility, resilience, and productivity across the entire industrial ecosystem.
Use Case:
SynapseFlow AI is critical for industries seeking maximum agility, efficiency, and resilience in complex, dynamic environments. Its applications are broad:
- Smart Manufacturing & Assembly:
- Production Line Re-routing: Automatically re-routes products to alternative machines or lines if a primary machine fails, is overloaded, or requires maintenance, ensuring continuous flow.
- Dynamic Resource Allocation: Adjusts staffing levels, robot assignments, or material delivery schedules based on real-time production demands, component availability, or worker fatigue (from wearables).
- Quality Control Adaptation: If a specific batch of raw material shows slight deviations, SynapseFlow AI can adjust machine parameters downstream to compensate, maintaining product quality without halting production.
- Logistics & Warehousing:
- Optimized Order Fulfillment: Dynamically re-prioritizes picking routes and allocates automated guided vehicles (AGVs) based on incoming order changes, truck arrival times, and real-time inventory levels.
- Traffic Management in Warehouses: Manages robotic and human traffic flows to prevent congestion and optimize movement paths in real-time.
- Dynamic Dock Scheduling: Adjusts loading/unloading schedules based on real-time truck GPS data, warehouse capacity, and labor availability.
- Process Industries (Chemicals, Food & Beverage):
- Adaptive Batch Processing: Modifies mixing times, temperatures, or ingredient flow rates based on real-time sensor data detecting slight variations in material properties or environmental conditions, ensuring consistent product quality and yield.
- Energy Optimization: Adjusts pump speeds, fan operations, or heating elements based on real-time demand and energy costs, reducing consumption.
- Construction & Heavy Industry:
- Dynamic Equipment Deployment: Re-allocates heavy machinery (e.g., excavators, cranes) based on real-time project progress, material delivery status, and unexpected site conditions.
- Resource Balancing: Optimizes worker and equipment assignments to critical path activities, reacting to delays or accelerations in real-time.
Tech Stack:
The complexity of SynapseFlow AI requires a robust and highly integrated technology stack:
- Data Ingestion & Streaming:
- Industrial IoT (IIoT) Gateways: For collecting data from sensors (temperature, vibration, pressure, current, vision systems), PLCs, SCADA systems, and industrial machinery.
- Wearable Integration: APIs and SDKs for connecting with smartwatches, smart glasses (AR/VR), and exoskeleton sensors for human-centric data (heart rate, fatigue, motion).
- Enterprise System Connectors: APIs for ERP (SAP, Oracle), MES, WMS, CMMS, and supply chain management (SCM) systems to pull in order data, inventory levels, maintenance schedules, etc.
- Message Brokers: Apache Kafka, RabbitMQ, or AWS Kinesis for high-throughput, low-latency real-time data streaming.
- Edge Computing:
- Edge Processors/Gateways: (e.g., NVIDIA Jetson, Intel OpenVINO, AWS IoT Greengrass) for local data pre-processing, filtering, anomaly detection, and immediate decision-making to minimize latency for critical actions.
- Cloud Platform & Scalable Storage:
- Cloud Providers: AWS, Google Cloud Platform (GCP), Microsoft Azure provide scalable compute, storage, and specialized services.
- Data Lakes: Amazon S3, Google Cloud Storage, Azure Data Lake Storage for storing vast quantities of raw and processed industrial data.
- Time-Series Databases: InfluxDB, TimescaleDB, Amazon Timestream for optimized storage and retrieval of sensor data.
- AI/ML Core & Orchestration Engine:
- ML Frameworks: TensorFlow, PyTorch, Scikit-learn for building and training predictive and prescriptive models.
- Reinforcement Learning (RL): For dynamic decision-making, learning optimal workflow adjustments through trial and error in simulated environments.
- Optimization Algorithms: Linear programming, mixed-integer programming, heuristic algorithms for complex resource allocation and scheduling problems.
- Process Mining & Simulation: Tools to analyze historical workflow data to identify bottlenecks and simulate the impact of proposed changes before deployment.
- Complex Event Processing (CEP): For detecting patterns and sequences in real-time data streams that trigger workflow changes.
- Workflow Orchestration Engine: Custom-built or commercial platforms (e.g., Apache Airflow, Camunda, Activiti) enhanced with AI capabilities for defining, executing, and dynamically modifying workflows.
- User Interface & Monitoring:
- Dashboards & Visualization: Grafana, Tableau, Power BI, or custom web UIs (React, Angular) for real-time visibility into workflow status, performance metrics, and AI-driven recommendations/actions.
- Alerting & Notification Systems: Email, SMS, push notifications to human operators for critical interventions or approvals.
- Cybersecurity: End-to-end encryption, access controls, intrusion detection systems tailored for OT/IT convergence.
Impact/ROI:
SynapseFlow AI delivers transformative ROI across various dimensions:
- Increased Operational Efficiency (15-30% improvement): By optimizing resource utilization, minimizing idle time, and streamlining processes in real-time.
- Reduced Downtime (Up to 50% for critical processes): Proactive adjustments based on predictive insights prevent bottlenecks and catastrophic failures.
- Enhanced Throughput & Production Capacity (10-25% increase): Continuous flow and rapid adaptation to disruptions maximize output.
- Cost Savings (Significant across OpEx):
- Reduced energy consumption through dynamic optimization.
- Lower labor costs through optimized workforce allocation.
- Decreased waste and rework due to real-time quality adjustments.
- Reduced inventory holding costs through just-in-time adjustments.
- Improved Agility & Responsiveness to Market Changes: The ability to quickly pivot production lines or logistics routes based on demand shifts or supply chain disruptions.
- Higher Product Quality & Consistency: Real-time parameter adjustments ensure consistent output regardless of minor input variations.
- Enhanced Worker Productivity & Safety: By optimizing workflows, reducing physical strain, and providing real-time guidance.
- Data-Driven Decision Making: Moves from reactive problem-solving to proactive, intelligent automation based on comprehensive data analysis.
Real-World Example:
Consider a large-scale consumer electronics manufacturing plant that produces various smartphone and tablet models, with frequently changing production schedules and component availabilities.
Before SynapseFlow AI: The plant operated on a relatively static master production schedule. If a specific component delivery was delayed, or a key machine went down, the entire line might stop or run inefficiently. Workers would have to manually re-route materials, leading to bottlenecks, missed deadlines, and significant human effort in troubleshooting and rescheduling. Quality issues might only be detected at the end of a batch, leading to costly rework.
With SynapseFlow AI:
- Real-time Data Ingestion: SynapseFlow AI continuously ingests data from:
- IIoT Sensors: On every machine (assembly robots, soldering stations, testing equipment) tracking operational status, throughput, and error rates.
- Logistics Systems: Providing real-time updates on incoming component shipments and outbound finished goods.
- MES/ERP: For current production orders, inventory levels, and labor availability.
- Wearables: On technicians, indicating their current task, location, and potential fatigue.
- Dynamic Workflow Adjustment:
- Scenario 1: Component Delay: A critical batch of display screens is delayed by 4 hours. SynapseFlow AI immediately detects this via the logistics system. Instead of halting the relevant assembly line, it automatically triggers a workflow change:
- It re-prioritizes production on other lines to focus on models not requiring the delayed component.
- It re-allocates idle workers from the affected line to support critical bottlenecks elsewhere or to perform preventive maintenance on other machines.
- It adjusts material delivery schedules for other components to prevent unnecessary inventory build-up at the line.
- Scenario 2: Machine Malfunction: An automated soldering machine begins showing increased error rates detected by IIoT sensors. SynapseFlow AI identifies the issue, forecasts a potential breakdown within 2 hours, and:
- Automatically re-routes product flow to an adjacent, less utilized soldering machine.
- Notifies the maintenance team with precise diagnostic information.
- Adjusts the overall production schedule to account for the slight reduction in capacity from using the backup machine.
- Scenario 3: Quality Fluctuation: Vision systems detect a subtle but consistent defect trend in a specific batch of assembled circuit boards. SynapseFlow AI immediately flags this, adjusts the parameters of the preceding pick-and-place machine to compensate for a suspected calibration drift, and alerts quality control for immediate inspection of the affected batch, preventing widespread defects.
- Scenario 1: Component Delay: A critical batch of display screens is delayed by 4 hours. SynapseFlow AI immediately detects this via the logistics system. Instead of halting the relevant assembly line, it automatically triggers a workflow change:
Result:
The plant achieves near zero unplanned downtime due to component delays or machine failures. Production throughput increases by 18% due to optimized flow and rapid recovery from disruptions. Cost savings are realized from reduced waste, lower emergency maintenance, and highly optimized labor utilization. The plant gains unmatched flexibility, allowing it to adapt to fluctuating market demands and supply chain challenges with minimal human intervention and maximum efficiency.
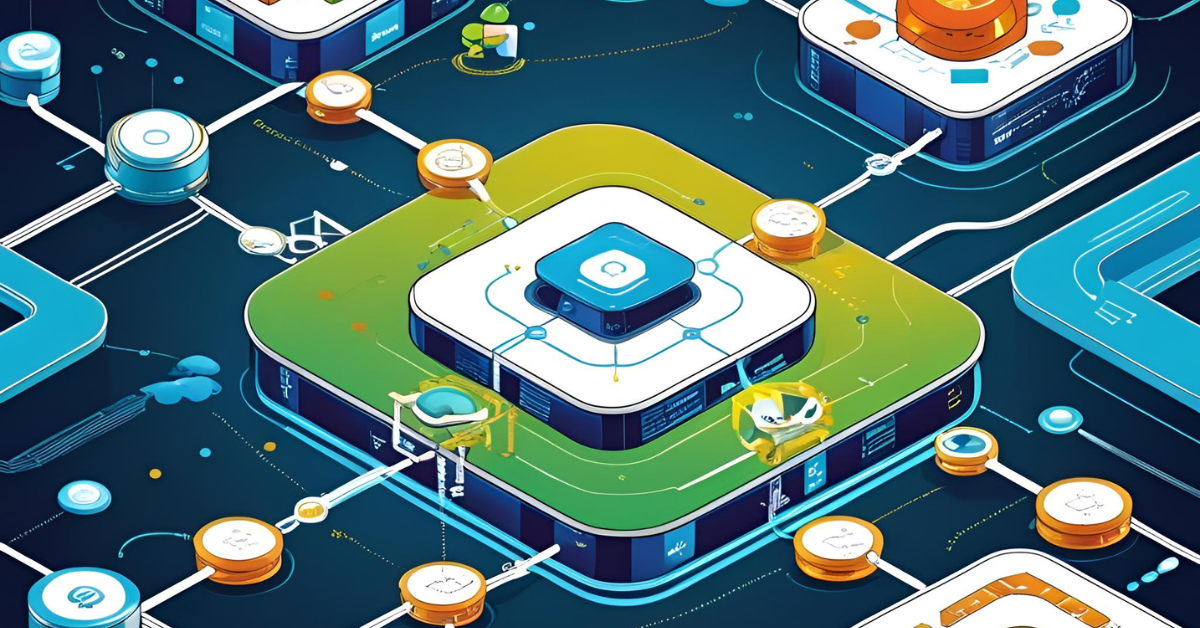
3.AI-Driven Dynamic Workflow Orchestration
Application Name: AuraFit (or "AuraSense")
Overview:
AuraFit is a groundbreaking Industrial Exoskeleton Data Interface platform designed to usher in an era of cybernetic workforce augmentation. By seamlessly integrating smart exoskeletons with advanced IoT sensors, AuraFit provides real-time muscle analytics and fatigue tracking directly on the factory floor, in warehouses, construction sites, and other physically demanding environments. This intelligent system doesn't just assist workers mechanically; it actively monitors their physiological state, analyzes biomechanical loads, and predicts fatigue onset, enabling proactive interventions that prevent injuries, enhance endurance, and optimize human-robot collaboration for unprecedented productivity and worker well-being. AuraFit transforms the worker into a "smart operator," empowered by data-driven insights and enhanced physical capabilities.
Use Case:
AuraFit is invaluable in any industry where manual labor involves repetitive motions, heavy lifting, sustained awkward postures, or prolonged physical exertion. Key use cases include:
- Automotive Assembly: Workers performing overhead tasks (e.g., installing components on car undersides), repetitive actions on assembly lines, or heavy lifting of parts. AuraFit can reduce strain on shoulders, back, and arms.
- Logistics & Warehousing: Employees engaged in order picking, packing, loading/unloading heavy boxes, or operating forklifts in dynamic environments. Fatigue tracking helps prevent errors and injuries from repetitive strain.
- Construction & Demolition: Workers handling heavy tools, lifting building materials, or performing overhead drilling/welding. Exoskeletons augment strength, while fatigue tracking ensures safe operation over long shifts.
- Shipbuilding & Aerospace: Tasks requiring sustained postures in confined spaces, heavy component manipulation, or grinding/welding overhead.
- Manufacturing (General): Any process involving manual material handling, repetitive motion, or sustained exertion where human strength and endurance limits are a factor.
- Aging Workforce Support: Enables older, experienced workers to remain in physically demanding roles longer by reducing physical strain and preventing age-related injuries.
Tech Stack:
AuraFit's intelligent capabilities rely on a sophisticated multi-layered tech stack:
- Exoskeleton Hardware:
- Powered Exoskeletons: (e.g., Sarcos Guardian XO, German Bionic Cray X, Ekso Bionics EksoVest) for active force augmentation using motors and actuators.
- Passive Exoskeletons: (e.g., Ottobock Paexo series, Laevo) for ergonomic support and load redirection using springs, dampers, and mechanical linkages.
- Integrated Sensors:
- Inertial Measurement Units (IMUs): Accelerometers, gyroscopes, magnetometers integrated into the exoskeleton joints and limbs to track motion, posture, joint angles, and movement speed.
- Electromyography (EMG) Sensors: Surface electrodes or integrated fabric sensors to measure muscle electrical activity, providing direct insight into muscle engagement and fatigue levels.
- Force Sensors/Load Cells: Embedded in exoskeleton joints or grip points to measure forces exerted by/on the user and the exoskeleton.
- Heart Rate Variability (HRV) Monitors: Wearable sensors (e.g., smartwatches, chest straps) integrated to assess physiological stress and fatigue indirectly.
- Temperature & Humidity Sensors: For environmental monitoring and worker comfort.
- Edge Computing & Data Ingestion:
- On-Exoskeleton Microcontrollers/Edge Devices: Process raw sensor data locally to extract key features, filter noise, and perform initial fatigue calculations, reducing data transmission load.
- Wireless Communication: Low-latency, high-bandwidth protocols like Wi-Fi 6, 5G, or proprietary industrial wireless (e.g., LoRaWAN for less critical data) to transmit data from exoskeletons to local gateways or cloud.
- Cloud Platform & Analytics:
- Cloud Providers: AWS IoT, Google Cloud IoT Core, Azure IoT Hub for secure ingestion and management of high-volume, real-time sensor data.
- Time-Series Databases: InfluxDB, TimescaleDB, or Amazon Timestream for optimized storage and querying of temporal sensor data.
- Machine Learning & AI Platform: TensorFlow, PyTorch, Scikit-learn for developing and deploying:
- Biomechanics Models: Analyze joint forces, torques, and movement efficiency.
- Fatigue Prediction Algorithms: Utilize EMG, motion, and physiological data to predict muscle fatigue onset and overall worker exhaustion.
- Anomaly Detection: Identify unusual movement patterns or stress on the exoskeleton indicating potential issues.
- Personalization Algorithms: Adapt exoskeleton assistance levels based on individual worker biometrics and task demands.
- Data Lake/Warehousing: (e.g., Apache Hadoop, Snowflake, Databricks) for long-term storage and historical analysis of aggregated worker performance and health data.
- User Interface & Integration:
- Worker Feedback System: Haptic feedback, visual cues on an integrated display (e.g., AR glasses), or subtle exoskeleton adjustments to guide posture or indicate fatigue levels.
- Supervisor Dashboard: Web-based or mobile application (React, Angular, Vue.js) providing real-time overview of worker health, fatigue alerts, and performance metrics across the factory floor.
- API Integration: RESTful APIs for seamless data exchange with existing HR systems, EHS (Environmental, Health, and Safety) platforms, CMMS (Computerized Maintenance Management Systems), and MES (Manufacturing Execution Systems).
Impact/ROI:
The implementation of AuraFit yields significant and multi-faceted ROI:
- Reduced Musculoskeletal Injuries (MSIs): Proactive fatigue tracking and ergonomic assistance drastically lower the incidence of back pain, shoulder strain, carpal tunnel syndrome, and other work-related MSIs. This translates to reduced worker's compensation claims, healthcare costs, and lost workdays.
- Increased Worker Productivity & Endurance: By augmenting strength and delaying fatigue, workers can maintain higher performance levels for longer periods, leading to increased output per shift. Studies show productivity gains of 10-30% or more in specific tasks.
- Lower Employee Turnover & Absenteeism: Improved worker comfort, reduced physical strain, and a safer work environment lead to higher job satisfaction and better employee retention, especially in physically demanding roles.
- Enhanced Safety: Real-time alerts for impending fatigue or improper posture help prevent accidents and ensure adherence to safety protocols.
- Improved Workforce Utilization: Enables companies to retain skilled but aging workers in roles they might otherwise have to leave due to physical limitations.
- Data-Driven Ergonomics: Provides granular data to engineers and safety managers to continuously refine workstation design, task sequencing, and training programs, creating a safer and more efficient work environment.
- Regulatory Compliance: Helps companies meet and exceed occupational health and safety regulations.
- Positive Brand Image: Demonstrates a commitment to worker well-being and cutting-edge technology, enhancing reputation and attracting talent.
Real-World Example:
Imagine a global automotive manufacturer's welding facility that employs hundreds of workers performing precision welding on vehicle undercarriages, requiring them to hold heavy welding guns overhead for extended periods. This task historically led to high rates of shoulder, neck, and back injuries, resulting in significant absenteeism, high worker's compensation costs, and frequent production bottlenecks.
Before AuraFit: Workers would experience cumulative fatigue throughout their shifts, often leading to decreased weld quality later in the day, slower work rates, and eventually, the need for medical leave. The only "fatigue tracking" was self-reported, often after pain had already set in.
With AuraFit:
- Smart Exoskeletons: Each welder is equipped with an upper-body industrial exoskeleton (e.g., a powered vest or arm support system) integrated with AuraFit's sensors.
- Real-time Monitoring: EMG sensors on the shoulders and back, along with IMUs in the exoskeleton arms, continuously monitor muscle activation and joint angles while the worker welds.
- Proactive Fatigue Alerts: AuraFit's ML models, trained on individual worker biometrics and historical fatigue data, detect early signs of muscle fatigue accumulation (e.g., a specific threshold of EMG activity coupled with prolonged overhead posture).
- Adaptive Assistance: The exoskeleton subtly adjusts its powered assistance levels to offload more weight from the worker's shoulders as fatigue begins to set in, providing just-in-time support.
- "Micro-Break" Recommendations: If fatigue reaches a critical level, AuraFit sends a gentle haptic alert or visual cue to the worker's AR glasses, suggesting a short, pre-defined ergonomic micro-break or a rotation to a less demanding task.
- Supervisor Insights: The EHS supervisor's dashboard provides an aggregated view of fatigue levels across the welding bay, allowing them to proactively plan rotations or allocate resources to prevent widespread fatigue and maintain consistent output quality.
Result:
The plant sees a dramatic reduction (e.g., 60-70%) in shoulder and back injuries among its welding workforce. Productivity increases as workers can maintain optimal performance for longer without debilitating fatigue. Absenteeism drops significantly, and the company benefits from a healthier, more engaged, and more efficient workforce, leading to millions of dollars in savings from reduced healthcare costs, improved output, and higher employee retention.
🚀 Ready to turn your passion for connected tech into real-world impact?
At Huebits, we don’t just teach IoT — we train you to build smart, scalable, and data-driven systems using the tech stacks powering today’s most innovative industries.
From edge devices to cloud platforms, you’ll gain hands-on experience designing end-to-end IoT architectures that collect, analyze, and respond in real time — built for deployment in cities, farms, factories, and homes.
🧠 Whether you're a student, aspiring IoT engineer, or future smart systems architect, our Industry-Ready IoT Program is your launchpad.
Master Python, Embedded C, MQTT, REST APIs, ESP32, Raspberry Pi, AWS IoT, Azure IoT Hub, and Grafana — all by building real-world IoT solutions that deliver results, not just data.
🎓 Next Cohort Starts Soon!
🔗 Join now and claim your seat in the IoT revolution powering tomorrow’s ₹1 trillion+ connected economy.
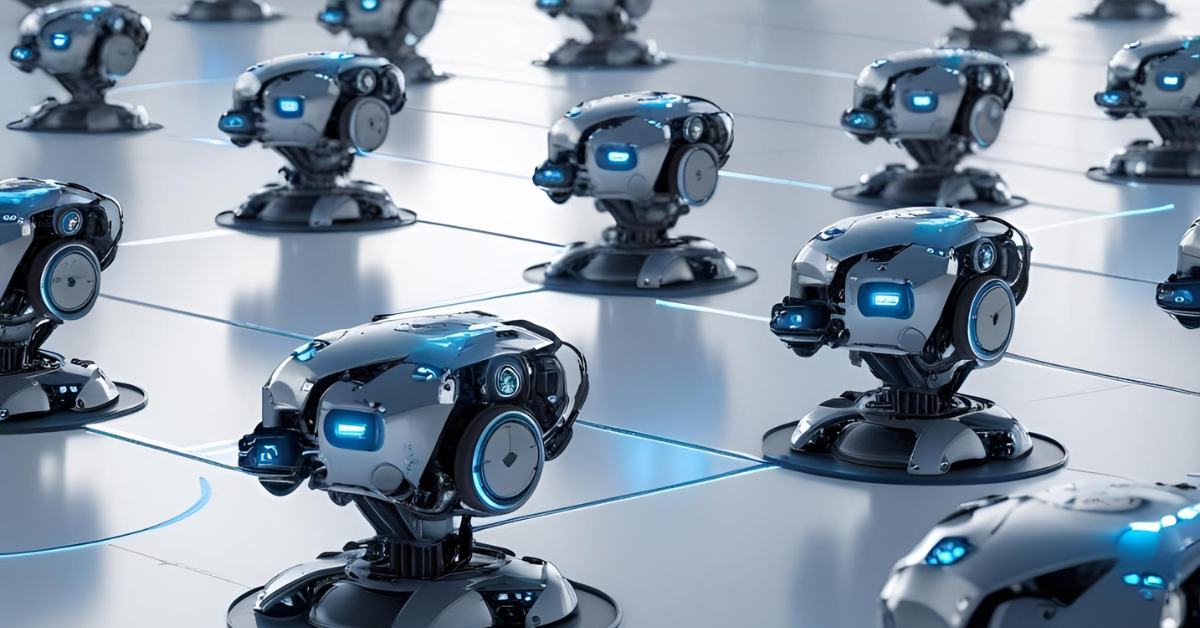
4.Swarm Robotics Coordination Systems
Application Name: HiveMind Robotics (or "MeshBots")
Overview:
HiveMind Robotics represents a paradigm shift in industrial automation, introducing Swarm Robotics Coordination Systems. This innovative platform leverages fleets of edge-controlled micro-robots that operate autonomously, coordinating seamlessly via a mesh IoT network without the need for a single central command unit. Each robot is an intelligent agent, communicating directly with its peers and its immediate environment. This decentralized intelligence enables the swarm to collectively perform complex tasks like cleaning, scanning, precision assembly, and detailed inspection with unprecedented efficiency, redundancy, and adaptability. HiveMind Robotics ushers in an era where automated tasks are handled by resilient, self-organizing robotic collectives, revolutionizing operations in intricate and dynamic industrial spaces.
Use Case:
HiveMind Robotics thrives in environments that are too large, too dangerous, too complex, or too dynamic for traditional single robots or human intervention. Key use cases include:
- Large-Scale Warehouse & Logistics Management:
- Inventory Scanning & Auditing: Fleets of small, agile robots autonomously navigate aisles, scanning QR codes or RFID tags on pallets and shelves for real-time, accurate inventory counts, identifying misplaced items or discrepancies.
- Package Sorting & Conveyance: Micro-robots can pick, sort, and move packages to designated areas, adapting to changing layouts or order priorities.
- Precision Manufacturing & Assembly:
- Micro-Assembly: Swarms of tiny robots collaboratively assemble intricate components (e.g., electronic circuit boards, medical devices) where human hands are too large or slow.
- Quality Inspection: Robots equipped with vision sensors perform continuous, high-resolution inspection of parts at various stages of production, identifying defects in real-time.
- Infrastructure Inspection & Maintenance (Difficult Access Areas):
- Pipe & Duct Inspection: Small, specialized robots navigate pipelines, ventilation shafts, or confined spaces to detect leaks, corrosion, or blockages, transmitting data back.
- Bridge & Building Structure Analysis: Robots with ultrasonic or thermal sensors crawl over large structures to find cracks, weak points, or thermal anomalies.
- Environmental Monitoring & Cleaning:
- Large Surface Cleaning: Fleets of cleaning robots autonomously cover vast industrial floors, adapting their paths to obstacles and prioritizing dirtier areas.
- Hazardous Material Handling/Spill Cleanup: Robots can isolate and clean up spills of dangerous chemicals in a factory without risking human life.
- Security & Surveillance:
- Perimeter Monitoring: Swarms of autonomous drones or ground robots provide continuous, dynamic surveillance of large industrial complexes or sensitive areas.
- Anomaly Detection: Collaboratively map an area and identify unusual activity or intrusions.
Tech Stack:
The decentralization and coordination capabilities of HiveMind Robotics rely on a sophisticated tech stack:
- Robot Hardware (Micro-Robots):
- Compact Design: Small form factor, often modular, with robust chassis for industrial environments.
- Onboard Sensors: Miniaturized vision cameras (RGB, IR, thermal), LiDAR/ToF sensors, ultrasonic sensors, accelerometers, gyroscopes, force/tactile sensors, gas/chemical sensors depending on task.
- Actuators: Miniature motors, grippers, manipulators, cleaning brushes, or specialized tools.
- Low-Power Microcontrollers: (e.g., ARM Cortex-M series, ESP32) for onboard processing and real-time control.
- Communication & Networking:
- Mesh IoT Network: Utilizes protocols like Thread, Zigbee, Wi-Fi Mesh, or custom low-power wireless solutions (e.g., Ultra-Wideband - UWB for precise localization) to enable direct, peer-to-peer communication between robots.
- Robust Protocols: Designed for high interference environments and redundancy, ensuring swarm communication even if some nodes fail.
- Edge Gateways: Strategically placed gateways act as bridges between the mesh network and the broader industrial network/cloud for data upload and overall system monitoring.
- Edge Computing & Distributed Intelligence:
- Onboard Edge AI/ML: Each robot runs lightweight AI models for local perception, navigation (SLAM - Simultaneous Localization and Mapping), obstacle avoidance, and task execution. This allows for immediate reactive behavior.
- Distributed Consensus Algorithms: Algorithms (e.g., inspired by natural swarm behaviors like ant colonies or bird flocks) enable robots to collaboratively make decisions, share local environmental data, and coordinate actions without a central brain.
- Decentralized Task Allocation: Robots dynamically assign tasks among themselves based on proximity, availability, and capability, responding to real-time changes in the environment or task requirements.
- Cloud Platform (for Aggregation & Analytics):
- IoT Platforms: AWS IoT, Azure IoT Hub, Google Cloud IoT Core for secure ingestion of aggregated data from edge gateways.
- Data Lake/Warehouse: For storing long-term performance data, inspection logs, and historical maps generated by the swarm for compliance, analytics, and training future AI models.
- MLOps Tools: For deploying updates to the edge AI models on the robots over-the-air (OTA).
- Control & Visualization:
- Minimal Human Interface: A central dashboard (web-based) for setting high-level mission parameters, monitoring swarm status, viewing collected data, and intervening only when necessary.
- Digital Twin Integration: For visualizing the swarm's real-time movements and the data they collect within a virtual representation of the industrial space.
Impact/ROI:
HiveMind Robotics delivers substantial ROI through several key areas:
- Unprecedented Efficiency (20-50% improvement): Parallel task execution by multiple robots drastically reduces completion times for large-scale operations like scanning or cleaning.
- Reduced Labor Costs: Automates repetitive, dangerous, or tedious tasks, freeing human workers for higher-value activities.
- Enhanced Data Accuracy & Granularity: Continuous, precise data collection (e.g., inventory, inspection) eliminates human error and provides richer insights.
- Improved Safety: Removes humans from hazardous environments (e.g., chemical spills, confined spaces, high-temperature areas).
- Increased Flexibility & Adaptability: The decentralized nature makes the system highly resilient to individual robot failures and capable of adapting to dynamic environments or changing task requirements.
- Optimized Resource Utilization: Robots can dynamically shift between tasks or areas based on real-time needs.
- Reduced Downtime for Inspection/Cleaning: Tasks can be performed continuously or during operational hours without requiring full shutdowns.
- Scalability: Easily add or remove robots from the swarm to scale capabilities up or down as needed.
Real-World Example:
Consider a large, multi-story pharmaceutical warehouse in Visakhapatnam, Andhra Pradesh, India, storing millions of units of sensitive medical supplies. Maintaining accurate inventory and ensuring cleanliness in specific, temperature-controlled zones is critical and labor-intensive.
Before HiveMind Robotics: Manual inventory counts were done periodically, leading to discrepancies and requiring several days. Cleaning in narrow, high-density shelving areas was difficult and time-consuming. Any misplacement of a batch could cause significant delays in order fulfillment.
With HiveMind Robotics (HiveMind Inventory & CleanSwarm modules):
- Autonomous Inventory Auditing: A swarm of HiveMind Inventory micro-robots (equipped with miniaturized RFID readers and vision cameras) are deployed. They autonomously navigate the warehouse aisles, coordinating their paths via their mesh IoT network to cover the entire facility efficiently. Each robot scans inventory tags and takes high-resolution images of stock.
- Dynamic Pathing: If one robot detects an obstruction or low battery, it automatically communicates with its peers, and the swarm re-distributes the remaining scan areas among available robots.
- Real-time Discrepancy Flagging: As they scan, the robots send real-time inventory data to an edge gateway, which then pushes aggregated data to a dashboard. If a robot scans an empty shelf that should contain product, or a barcode that doesn't match the expected inventory, it immediately flags a discrepancy on the central dashboard, pinpointing the exact location for human investigation.
- Automated Cleaning in Sterile Zones: In designated sterile packing areas, a separate swarm of CleanSwarm robots (equipped with UV-C lights and micro-scrubbers) operates autonomously. They coordinate to cover every inch of the floor space during off-hours, ensuring consistent hygiene levels.
- Obstacle Avoidance & Coordination: They share sensor data to avoid collisions, plan optimal cleaning paths, and ensure no spot is missed or double-cleaned.
- Status Reporting: The robots report back on cleaning progress, battery levels, and any detected anomalies (e.g., spills) to the facility manager's dashboard.
Result:
The pharmaceutical warehouse achieves 99.9% real-time inventory accuracy, eliminating the need for periodic manual counts and drastically reducing misplacement errors. This leads to faster order fulfillment and significantly reduced stock-outs. Cleaning costs are reduced by 30%, and hygiene levels in critical areas are consistently maintained, improving compliance with pharmaceutical regulations. Overall, the operational efficiency of the warehouse improves by 25%, allowing the company to handle higher volumes with greater reliability and safety.
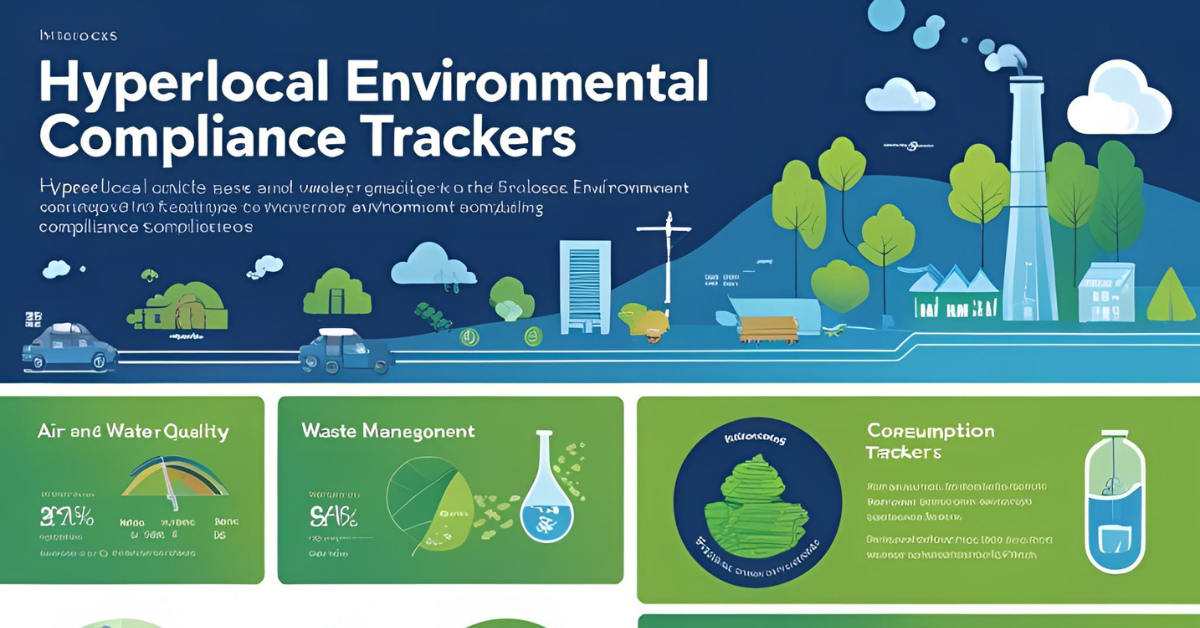
5.Hyperlocal Environmental Compliance Trackers
Application Name: AuraGuard (or "EnviroScan AI")
Overview:
AuraGuard is a sophisticated Hyperlocal Environmental Compliance Tracker system designed to bring unprecedented transparency and precision to industrial environmental monitoring. It deploys a dense network of real-time CO₂, PM2.5, and toxic emission monitors directly at the source, across factory perimeters, and within specific industrial zones. These advanced IIoT sensors continuously feed granular, real-time data into intelligent, auto-reporting Environmental, Social, and Governance (ESG) dashboards. AuraGuard moves beyond periodic manual checks, enabling proactive identification of emission anomalies, ensuring stringent regulatory compliance at scale, and providing verifiable data for sustainability reporting. It acts as a vigilant guardian of industrial environmental impact, transforming compliance from a burden into a strategic asset.
Use Case:
AuraGuard is essential for industries with significant environmental footprints or those operating under strict regulatory frameworks. Key use cases include:
- Manufacturing Plants (Chemical, Cement, Steel, Textiles):
- Stack Emission Monitoring: Real-time tracking of pollutants like SOx, NOx, CO, VOCs, and particulate matter from industrial chimneys and vents to ensure compliance with emission limits.
- Fenceline Monitoring: Deploying sensors along the facility perimeter to detect fugitive emissions or accidental releases that could impact surrounding communities.
- Process Optimization: Using emission data to optimize combustion processes or chemical reactions, reducing pollution and improving resource efficiency.
- Power Generation Facilities (Thermal, Waste-to-Energy):
- Continuous Emission Monitoring (CEMs): Providing verified, real-time data on greenhouse gas and pollutant emissions to meet national and international carbon reporting and air quality standards.
- Efficiency Monitoring: Linking emission levels to operational parameters to identify inefficiencies that lead to higher pollution.
- Ports & Logistics Hubs:
- Air Quality Monitoring: Tracking PM2.5, PM10, NOx, and SOx from vessel emissions, truck idling, and cargo handling equipment within and around port areas to manage local air quality and comply with emission control areas (ECAs).
- Dust Control: Monitoring dust levels in real-time during cargo operations (e.g., coal, ore) to trigger water suppression systems or adjust operational intensity.
- Mining & Construction Sites:
- Dust & Particulate Monitoring: Tracking PM2.5 and PM10 to ensure compliance with dust suppression regulations and worker safety limits.
- Noise Pollution Monitoring: Integrating noise sensors to track and report on sound levels, particularly near residential areas.
- Oil & Gas Refineries & Petrochemical Plants:
- Leak Detection: Monitoring for volatile organic compounds (VOCs) and methane (CH4) around equipment, pipelines, and storage tanks to detect leaks early, reducing environmental impact and potential safety hazards.
- Flares Monitoring: Analyzing emissions from flaring operations.
- Waste Management Facilities (Landfills, Incinerators):
- Methane & VOC Monitoring: Detecting gas emissions from landfills.
- Incinerator Emission Control: Ensuring incinerator emissions meet stringent air quality standards.
Tech Stack:
AuraGuard's effectiveness hinges on a robust and interconnected technology stack:
- Sensor Hardware (Hyperlocal Monitors):
- Gas Sensors: Electrochemical sensors (CO, CO₂, SO₂, NOx, H₂S), Photoionization Detectors (PIDs) for VOCs, NDIR (Non-Dispersive Infrared) for CO₂, Methane sensors.
- Particulate Matter Sensors: Optical sensors for PM1.0, PM2.5, PM10 (e.g., laser scattering technology).
- Environmental Sensors: Temperature, humidity, pressure, wind speed/direction sensors for comprehensive context.
- Integrated Units: Ruggedized, weather-proof, low-power IIoT sensor nodes designed for continuous outdoor or industrial deployment.
- Connectivity:
- Wireless Protocols: LoRaWAN (for wide-area, low-power deployment), NB-IoT, LTE-M (for cellular coverage), Wi-Fi (for local high-bandwidth data), or private industrial wireless (e.g., ISA100.11a).
- Edge Gateways: Secure industrial gateways that aggregate data from multiple sensors, perform initial filtering and aggregation, and transmit to the cloud or local servers.
- Edge Computing:
- Local Processing: Lightweight AI models on edge devices for real-time anomaly detection (e.g., sudden spikes in emissions) and immediate local alerts, reducing latency for critical environmental events.
- Data Compression: Compressing and pre-processing data before transmission to optimize bandwidth usage.
- Cloud Platform & Analytics:
- IoT Platform: AWS IoT Core, Azure IoT Hub, Google Cloud IoT Core for secure ingestion, device management, and message routing.
- Time-Series Databases: InfluxDB, TimescaleDB, Amazon Timestream, Azure Data Explorer for efficient storage and querying of high-volume, real-time sensor data.
- Data Lake: Amazon S3, Azure Data Lake Storage, Google Cloud Storage for long-term archival and big data analytics.
- AI/ML & Advanced Analytics:
- Anomaly Detection: Machine learning algorithms (e.g., Isolation Forest, ARIMA models) to identify unusual emission patterns or equipment malfunctions.
- Predictive Modeling: Forecasting potential emission exceedances based on operational parameters and historical data.
- Source Apportionment: Advanced analytics to help identify the specific source of an emission spike.
- Reporting & Visualization:
- ESG Dashboards: Custom or off-the-shelf Business Intelligence (BI) tools (e.g., Grafana, Tableau, Power BI) providing intuitive, real-time views of emission levels, compliance status, trends, and alerts.
- Automated Reporting Engine: Generates periodic (daily, weekly, monthly) compliance reports in formats required by regulatory bodies (e.g., Central Pollution Control Board (CPCB), State Pollution Control Boards (SPCBs) in India), auditors, and stakeholders.
- Alerting System: SMS, email, mobile app notifications for real-time alerts on threshold breaches or critical events.
- Integration:
- APIs: For seamless integration with existing SCADA, DCS, MES, ERP, and EHS (Environmental, Health, and Safety) systems to correlate environmental data with operational data.
Impact/ROI:
AuraGuard delivers significant ROI through several critical avenues:
- Guaranteed Regulatory Compliance & Reduced Fines: Proactive, real-time monitoring and automated reporting drastically reduce the risk of non-compliance, avoiding hefty fines, legal penalties, and operational shutdowns.
- Enhanced ESG Performance & Brand Reputation: Provides verifiable data for sustainability reports, demonstrating commitment to environmental stewardship, attracting responsible investors, and improving public perception.
- Optimized Operational Efficiency & Cost Savings:
- Resource Efficiency: Identifying inefficient processes that lead to higher emissions (e.g., sub-optimal combustion) can reduce raw material consumption and energy costs.
- Proactive Issue Resolution: Detecting anomalies early prevents minor issues from escalating into major environmental incidents.
- Reduced Manual Effort: Automating data collection and reporting saves significant labor hours previously spent on manual checks and report generation.
- Improved Public & Employee Health: Better air quality management reduces exposure to harmful pollutants for workers and nearby communities.
- Competitive Advantage: Companies with superior environmental performance gain an edge in increasingly sustainability-focused markets and supply chains.
- Data-Driven Decision Making: Provides granular insights to process engineers and environmental managers to continually optimize operations for both production and environmental impact.
Real-World Example:
Consider a large-scale steel manufacturing plant located near Visakhapatnam, Andhra Pradesh, India. Steel plants are known for significant emissions of particulate matter (PM2.5, PM10), CO, CO₂, SOx, and NOx from their blast furnaces, coke ovens, and rolling mills. The plant operates under strict regulations from the Andhra Pradesh Pollution Control Board (APPCB) and the Central Pollution Control Board (CPCB), with heavy penalties for emission limit exceedances.
Before AuraGuard: The plant relied on periodic manual stack sampling and limited fixed monitoring stations, providing only snapshots of their emissions. This made it difficult to pinpoint the exact source of an emission spike, often leading to reactive measures after an incident was reported or a regulatory audit revealed a violation. ESG reporting was based on estimations and averaged data.
With AuraGuard:
- Hyperlocal Sensor Network: The plant deploys a dense network of AuraGuard sensors:
- Stack Monitors: Continuous Emission Monitoring Systems (CEMS) integrated with AuraGuard are installed on the main stacks, providing real-time data on SOx, NOx, CO, CO₂, and PM emissions.
- Perimeter Monitors: A grid of PM2.5, PM10, and specific gas sensors (e.g., H₂S, VOCs) are placed along the plant's fenceline, especially near residential areas.
- Process Monitors: Sensors are also integrated within key production areas (e.g., near coke ovens, sintering plants) to monitor fugitive emissions and process-specific pollutants.
- Real-time Insights & Alerts: AuraGuard's platform continuously processes this data.
- If PM2.5 levels at the fenceline start to trend upwards due to an issue at a specific material handling area, AuraGuard immediately sends an alert to the environmental manager's mobile app and the control room dashboard, pinpointing the exact location and suggesting potential causes.
- If the SOx levels from a furnace stack approach a regulatory limit, AuraGuard's AI can trigger an automated alert and even suggest operational adjustments (e.g., optimize fuel-air ratio) to bring emissions back within limits before a violation occurs.
- Automated ESG Reporting: The system automatically compiles all real-time and historical emission data into CPCB and APPCB compliant formats, generating daily, weekly, and monthly reports with a click of a button. It also populates the plant's internal ESG dashboard with verifiable metrics on environmental performance.
Result:
The steel plant achieves full, continuous regulatory compliance, virtually eliminating fines related to environmental violations. Its environmental footprint is significantly reduced through data-driven operational optimization. The plant's ESG ratings improve, attracting new investors and enhancing its reputation within the community. Furthermore, the automated reporting saves hundreds of labor hours annually, freeing up environmental staff to focus on strategic sustainability initiatives rather than data collection and manual report generation. The transparency provided by AuraGuard also builds greater trust with local communities and regulators.
🚀 Ready to turn your passion for connected tech into real-world impact?
At Huebits, we don’t just teach IoT — we train you to build smart, scalable, and data-driven systems using the tech stacks powering today’s most innovative industries.
From edge devices to cloud platforms, you’ll gain hands-on experience designing end-to-end IoT architectures that collect, analyze, and respond in real time — built for deployment in cities, farms, factories, and homes.
🧠 Whether you're a student, aspiring IoT engineer, or future smart systems architect, our Industry-Ready IoT Program is your launchpad.
Master Python, Embedded C, MQTT, REST APIs, ESP32, Raspberry Pi, AWS IoT, Azure IoT Hub, and Grafana — all by building real-world IoT solutions that deliver results, not just data.
🎓 Next Cohort Starts Soon!
🔗 Join now and claim your seat in the IoT revolution powering tomorrow’s ₹1 trillion+ connected economy.
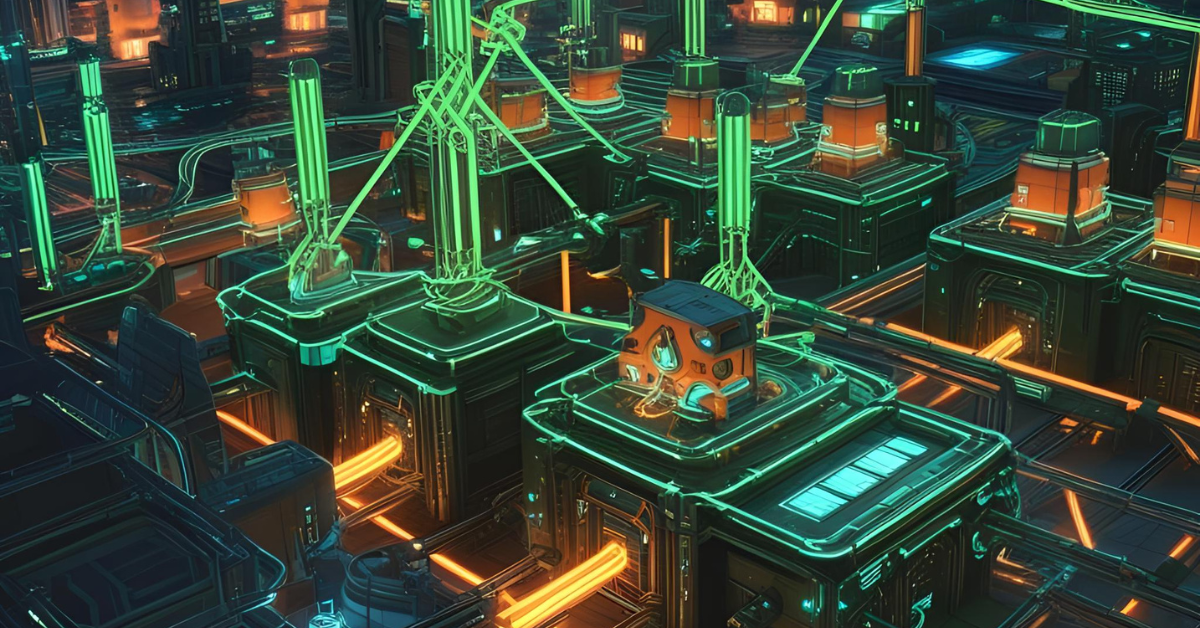
6.Self-Healing Factory Networks
Application Name: NeuroMesh Industrial (or "ResilientNet")
Overview:
NeuroMesh Industrial is a revolutionary Self-Healing Factory Network solution designed to create ultra-resilient, intelligent communication infrastructures for Industry 4.0. Inspired by the adaptive capabilities of biological nervous systems, NeuroMesh Industrial's IIoT nodes are not just passive data points; they are active, intelligent agents capable of detecting network anomalies like latency spikes or packet loss, dynamically rerouting traffic around congested or failing pathways, and even self-patching security vulnerabilities or software glitches on the fly. This decentralized, autonomous healing mechanism ensures continuous, uninterrupted data flow within the industrial environment, acting as the bedrock for critical real-time operations, autonomous systems, and predictive analytics. It transforms traditional, brittle industrial networks into fluid, adaptive, and inherently robust communication arteries.
Use Case:
NeuroMesh Industrial is indispensable for any industrial operation where continuous connectivity, low latency, and data integrity are non-negotiable for safety, productivity, or quality. Key use cases include:
- Automated Manufacturing & Robotics:
- Real-time Robot Coordination: Ensures uninterrupted, low-latency communication between collaborative robots (cobots), AGVs (Automated Guided Vehicles), and production line machinery, preventing collisions, ensuring synchronization, and avoiding production halts.
- Critical Process Control: Guarantees reliable data exchange for closed-loop control systems, where even momentary network drops could lead to significant quality deviations or safety incidents.
- Energy & Utilities (Smart Grids, Power Plants):
- Substation Automation: Ensures reliable communication for critical protection relays and control systems in substations, preventing blackouts or cascading failures.
- Distributed Energy Resource Management: Enables continuous communication with solar farms, wind turbines, and battery storage systems for real-time optimization and grid stability.
- Oil & Gas Refineries & Pipelines:
- Sensor Data Transmission: Guarantees continuous flow of data from thousands of pressure, temperature, flow, and leak detection sensors across vast and often remote facilities, critical for safety and operational awareness.
- Emergency Shutdown Systems: Ensures that commands for emergency shutdowns are transmitted without delay or failure, even under network stress.
- Large-Scale Logistics & Warehousing:
- AGV & Drone Navigation: Provides uninterrupted connectivity for autonomous vehicles and drones, crucial for real-time navigation, collision avoidance, and task execution in dynamic environments.
- Inventory Management Systems: Ensures real-time updates for inventory systems, preventing discrepancies caused by network interruptions during scanning or movement.
- Mining & Heavy Industry:
- Remote Operations: Guarantees stable network links for remotely operated heavy machinery in hazardous environments.
- Telemetry & Monitoring: Ensures continuous data flow from equipment health sensors in harsh conditions.
- Critical Infrastructure (Water Treatment, Transportation):
- SCADA/DCS Communication: Maintains robust communication links for Supervisory Control and Data Acquisition (SCADA) and Distributed Control Systems (DCS) crucial for public safety and utility delivery.
Tech Stack:
NeuroMesh Industrial combines cutting-edge networking, AI, and cybersecurity elements:
- Intelligent IIoT Nodes (Hardware):
- Multi-Interface Radios: Nodes equipped with multiple wireless communication interfaces (e.g., Wi-Fi 6/7, 5G/LTE, UWB, LoRaWAN) and possibly wired Ethernet ports, allowing for redundant pathways.
- Edge Computing Processors: Powerful ARM or x86 processors on each node capable of running AI models for real-time network analytics and decision-making.
- Resilient Hardware: Industrial-grade components designed for harsh environments (temperature, vibration, dust).
- Software-Defined Networking (SDN) & Network Function Virtualization (NFV):
- Centralized Control Plane (Logical): While physical nodes are distributed, an SDN controller (which can also be distributed for redundancy) logically centralizes network management, allowing for programmatic control over traffic flows.
- Dynamic Routing Protocols: Advanced routing algorithms (e.g., OSPF, BGP) augmented with AI-driven path selection based on real-time network conditions (latency, bandwidth, error rates).
- Virtual Network Functions: Network services (e.g., firewalls, intrusion detection, QoS enforcement) implemented as software functions that can be deployed or shifted dynamically across nodes.
- AI/ML for Network Intelligence:
- Anomaly Detection: Machine learning algorithms (e.g., autoencoders, statistical process control) deployed at the edge and cloud to detect unusual network behavior (e.g., sudden latency spikes, unexplained packet drops) that could indicate a problem or attack.
- Predictive Analytics: AI models analyze historical network data to predict potential congestion points, hardware failures, or security threats before they occur.
- Reinforcement Learning: For optimal decision-making in real-time, allowing the network to "learn" the best rerouting strategies or patching sequences based on outcomes.
- Self-Optimization Algorithms: AI-driven algorithms continuously adjust network parameters (e.g., transmission power, channel selection, bandwidth allocation) for optimal performance.
- Decentralized Coordination Mechanisms:
- Consensus Algorithms: Lightweight distributed consensus protocols (similar to those in blockchain or distributed databases) that allow nodes to agree on network state and healing actions without a single point of failure.
- Distributed Ledger Technology (DLT) / Blockchain (Optional for Audit Trail/Trust): Could be used for immutable logging of network changes, patches, and security events, enhancing trust and auditability.
- Cybersecurity & Self-Patching:
- Zero-Trust Architecture: Every connection and device is authenticated and authorized, regardless of its location within the network.
- Automated Vulnerability Scanning: Integrated capabilities to continuously scan for software vulnerabilities.
- Over-the-Air (OTA) Updates & Patching: Secure mechanisms for deploying software updates and security patches to nodes autonomously, often with roll-back capabilities.
- Threat Detection & Response (Automated): AI-driven detection of cyber threats (e.g., DDoS attempts, malware propagation) and automated response actions like isolating compromised nodes or rerouting traffic away from threats.
- Centralized Visibility & Management:
- Network Operations Center (NOC) Dashboard: A high-level view for human operators to monitor network health, receive alerts, and approve complex changes, though basic healing is autonomous.
- Digital Twin of Network: A virtual replica of the network topology and its real-time performance, allowing for simulation of changes and rapid troubleshooting.
Impact/ROI:
NeuroMesh Industrial delivers profound ROI, especially in mission-critical industrial settings:
- Near-Zero Network Downtime (Up to 99.999% availability): The primary benefit, directly translating to continuous production, uninterrupted services, and maximum operational uptime. This eliminates losses from stalled production lines or critical system failures.
- Enhanced Operational Efficiency: Reduced latency and optimized traffic flow improve the responsiveness of automated systems, leading to faster production cycles and more efficient resource utilization.
- Reduced IT/OT Support Costs: Automation of network monitoring, troubleshooting, and patching drastically reduces the need for manual intervention by network engineers, freeing them for strategic initiatives.
- Increased Security & Resilience against Cyber Threats: The self-healing and adaptive nature allows the network to automatically detect and mitigate cyberattacks, minimizing their impact and preventing data breaches or system compromise.
- Improved Data Integrity & Reliability: Ensures that critical data from sensors and control systems reaches its destination accurately and consistently, leading to better decision-making and product quality.
- Lower Maintenance Costs: Proactive identification and resolution of network issues before they escalate into major problems.
- Future-Proofing: The adaptive architecture can scale and evolve with new technologies (e.g., higher bandwidth requirements for advanced AI, new sensor types) without requiring complete network overhauls.
Real-World Example:
Consider a major port automation project in Visakhapatnam, Andhra Pradesh, India, aimed at fully automating container handling using a fleet of hundreds of Autonomous Rail-Mounted Gantry (ARMG) cranes, Automatic Stacking Cranes (ASCs), and Automated Guided Vehicles (AGVs). The seamless, real-time coordination of these assets, along with their communication with the Terminal Operating System (TOS), is absolutely critical for efficient cargo flow and preventing collisions.
Before NeuroMesh Industrial: The port relied on a traditional, segmented wireless network. A single access point failure, electromagnetic interference from passing ships, or an overload in one network segment could lead to communication drops for multiple AGVs or cranes. This would cause them to stop, creating bottlenecks, risking collisions (if safety protocols weren't instantly engaged), and leading to significant delays in cargo loading/unloading, costing millions per hour. Troubleshooting such issues was manual and time-consuming.
With NeuroMesh Industrial:
- Intelligent Network Nodes: Thousands of NeuroMesh Industrial IIoT nodes are strategically deployed across the entire port area – on every crane, AGV, and at various ground points. Each node can communicate via multiple wireless channels (Wi-Fi 6, 5G private network slices, UWB for hyper-localization).
- Real-time Latency Detection & Rerouting: An ARMG crane begins experiencing a slight increase in latency when communicating with the TOS via its primary Wi-Fi connection due to sudden localized interference from a new ship's radar. NeuroMesh Industrial's on-node AI immediately detects this latency spike.
- Autonomous Rerouting: Before the latency becomes critical, the affected node instantly reroutes its traffic to an alternative 5G private network slice, maintaining sub-millisecond communication with no perceived interruption to the crane's operation. This happens within milliseconds, completely transparent to the TOS and the crane itself.
- Self-Patching Security Vulnerability: A new minor firmware vulnerability is discovered in a specific batch of older AGV network modules. NeuroMesh Industrial's central orchestrator securely pushes a self-patching update to all affected AGV nodes over-the-air. The individual AGV nodes download and apply the patch during planned micro-maintenance windows or even on the fly if deemed non-disruptive, reporting successful application back to the system. If a patch fails on a node, the system can automatically roll back to the previous stable version.
- Predictive Maintenance for Network Hardware: NeuroMesh Industrial's AI constantly analyzes the performance of each node. If it detects a consistent pattern of minor errors or slightly elevated temperatures in a specific access point (Node X) over several days, it predicts a potential hardware failure within the next week. It then automatically schedules Node X for inspection or replacement during the next available non-peak hours, rerouting all traffic away from it proactively.
Result:
The Visakhapatnam port achieves near 100% network uptime for its automated cargo operations, drastically reducing delays caused by communication issues. This translates to millions of dollars saved annually from increased throughput, reduced demurrage charges, and optimized resource utilization. Operational safety is enhanced due to reliable real-time coordination. The port's IT/OT teams spend significantly less time on reactive network troubleshooting and more on strategic enhancements, ensuring Visakhapatnam's position as a leading smart and efficient port in India.
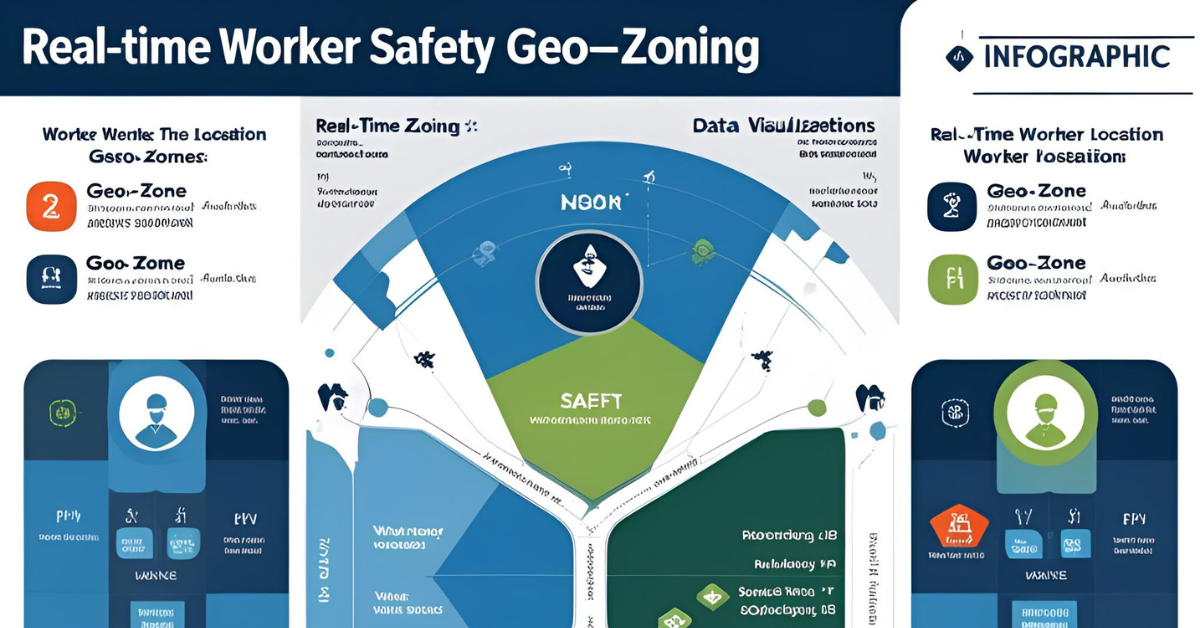
7.Real-Time Worker Safety Geo-Zoning
Application Name: SentinelZone Safety
Overview:
SentinelZone Safety is a cutting-edge Real-Time Worker Safety Geo-Zoning platform that leverages precise location technologies to create a dynamic, invisible shield around industrial workers. By defining granular safe zones and exclusion zones using Ultra-Wideband (UWB) for pinpoint accuracy and Bluetooth Low Energy (BLE) for broader presence detection, SentinelZone Safety monitors worker positions in real time. The moment a worker, equipped with a smart wearable (e.g., wristband, smart badge) and integrated with their hardhat (helmet cams), crosses into a predefined danger zone or an unauthorized area, the system instantly triggers alerts. This immediate notification, coupled with visual verification from helmet cameras, enables rapid intervention, prevents accidents, ensures regulatory compliance, and transforms workplace safety from reactive to proactive, safeguarding personnel in hazardous industrial environments.
Use Case:
SentinelZone Safety is critical for industries with high-risk operations, heavy machinery, hazardous materials, or complex layouts where worker safety is paramount. Key use cases include:
- Construction Sites:
- Heavy Machinery Exclusion Zones: Automatically alerts workers if they get too close to operating excavators, cranes, or dump trucks, preventing "struck-by" incidents.
- Fall Protection Areas: Defines virtual boundaries around unprotected edges at height; alerts if a worker approaches without proper fall arrest equipment detected (via integrated sensors).
- Confined Space Entry: Monitors entry and exit from confined spaces, ensuring no unauthorized access and that permits are followed, with automatic alerts if a worker goes silent or is overdue.
- Manufacturing & Industrial Plants:
- Robotics Cells: Creates exclusion zones around active robotic arms; if a worker enters, it can trigger an alarm or even a "safe stop" of the robot.
- High-Voltage Areas / Lockout/Tagout Zones: Ensures only authorized personnel with specific clearances (via their wearable credentials) can enter, preventing electrocution hazards.
- Hot Work / Hazardous Material Storage: Alerts workers if they enter areas with elevated temperatures or toxic gas storage without appropriate PPE (e.g., gas detectors integrated into wearables).
- Mining Operations (Open-pit & Underground):
- Blasting Zones: Automatically evacuates and verifies clear zones before blasting operations.
- Vehicle-Pedestrian Segregation: Alerts both vehicle operators and nearby workers if they are on a collision course in low-visibility mining environments.
- Roof Bolting/Support Areas: Monitors worker presence in unstable ground conditions.
- Ports & Shipyards:
- Crane Operating Radii: Alerts workers who stray into the swing radius of large port cranes during container operations.
- Vessel Hot Zones: Defines areas around active welding or maintenance on ships as high-risk.
- Forklift & AGV Paths: Prevents human-vehicle collisions in busy logistics areas.
- Oil & Gas Refineries / Petrochemical Plants:
- Flare Stack Exclusion: Establishes temporary no-go zones around flare stacks during flaring events.
- Leak Response Zones: Defines dynamic exclusion zones around detected leaks of hazardous chemicals, guiding workers away from danger.
Tech Stack:
SentinelZone Safety requires a robust combination of precise positioning, communication, and analytics technologies:
- Location Hardware:
- UWB Anchors (Fixed): Strategically placed throughout the industrial facility (e.g., every 10-30 meters) to provide highly accurate (10-30 cm) real-time positioning using Time-of-Flight (ToF) measurements.
- BLE Beacons (Fixed/Mobile): Lower cost, lower accuracy (1-5 meters) beacons for broader presence detection, especially in less critical areas or as a backup/complement to UWB. Can also be placed on assets.
- Worker Wearables:
- UWB/BLE Tags: Small, ruggedized tags worn by workers (e.g., on wristbands, hardhats, belt clips) that transmit signals to anchors.
- Integrated Sensors: Accelerometers (for fall detection), gyroscopes (for orientation), heart rate monitors (for fatigue/stress), basic environmental sensors (temperature, gas detection) within the wearable.
- Alert Feedback: Haptic (vibration) motors, audible alarms, and LED indicators on the wearable to alert the worker directly.
- Smart Hardhats/Helmet Cams: Ruggedized hardhats with integrated wide-angle cameras for visual verification, microphones for audio, and potentially edge AI for immediate hazard recognition (e.g., detecting unsafe postures, missing PPE).
- Networking & Data Transmission:
- UWB/BLE Network: The mesh of UWB anchors and BLE beacons forms a robust, low-latency, localized network.
- Industrial Wireless Network: Wi-Fi 6, 5G Private Network, or dedicated industrial wireless (e.g., LoRaWAN for non-critical alerts) to transmit data from anchors/gateways to local edge servers or the cloud.
- Edge Gateways/Servers: Collect data from UWB anchors and BLE beacons, perform initial processing (e.g., trilateration/multilateration for location calculation), and run lightweight AI models for immediate geo-zone violation detection.
- Software & Analytics Platform:
- Real-Time Location System (RTLS) Engine: Software module that processes UWB/BLE raw data into precise location coordinates.
- Geo-Zoning Configuration: User interface for defining virtual safe zones, exclusion zones, and conditional zones (e.g., requiring specific PPE) on a digital map of the facility.
- Rules Engine: Defines the logic for alerts (e.g., "If Worker A enters Zone B, trigger Alert C").
- AI/ML for Behavioral Analysis:
- Contextual Awareness: ML models correlate location data with operational schedules, machine status (via IIoT integration), and worker biometrics (from wearables) to refine alerts and reduce false positives.
- Predictive Safety: Identifies patterns of risky behavior or frequently breached zones to inform safety training and operational adjustments.
- Helmet Cam AI: Image recognition models process video streams for immediate visual verification of incidents or detection of unsafe acts.
- Cloud Platform: AWS IoT, Azure IoT, Google Cloud IoT for scalable data storage, advanced analytics, and long-term reporting.
- Data Lake/Warehouse: For historical data storage and compliance audits.
- User Interface & Alerting:
- Real-time Dashboard: Web-based or mobile application for safety managers, supervisors, and control room operators showing live worker locations, zone violations, and alert statuses on an interactive facility map.
- Automated Alerts: SMS, email, in-app notifications, and potentially integration with plant PA systems or emergency response teams.
- Incident Logging & Reporting: Automated generation of detailed incident reports for analysis, compliance, and post-incident investigation.
- Integration:
- API Gateway: For seamless integration with existing EHS (Environmental, Health, and Safety) systems, HR databases, video management systems, and plant control systems (SCADA/MES) for richer context and automated responses (e.g., slowing down machinery).
Impact/ROI:
SentinelZone Safety delivers significant and measurable ROI:
- Dramatic Reduction in Accidents & Injuries (15-40% or more): Proactive real-time alerts and interventions directly prevent workers from entering hazardous areas or engaging in unsafe proximity to machinery, leading to fewer incidents, medical costs, and lost workdays.
- Lower Worker's Compensation Claims & Insurance Premiums: A safer workplace translates to fewer claims, which can substantially reduce insurance costs over time.
- Enhanced Regulatory Compliance & Reduced Fines: Provides irrefutable, real-time data demonstrating adherence to safety protocols and geo-zoning regulations (e.g., OSHA, Factory Act, Mines Act in India), avoiding costly penalties and legal liabilities.
- Improved Productivity: Fewer accidents mean less downtime for investigations, cleanup, and worker replacement. Workers who feel safer are also more focused and productive.
- Increased Operational Visibility: Supervisors gain real-time insights into worker locations and safety statuses, enabling better resource deployment and emergency response.
- Data-Driven Safety Culture: Comprehensive data on near-misses and zone breaches allows for continuous improvement of safety protocols, targeted training, and optimized facility layouts.
- Faster Emergency Response: Precise location data for injured workers or those in distress significantly reduces emergency response times, potentially saving lives.
- Reduced Employee Turnover: A strong commitment to worker safety improves morale, job satisfaction, and employee retention, lowering recruitment and training costs.
Real-World Example:
Consider a large-scale, active port expansion project in Visakhapatnam, Andhra Pradesh, India, where new jetties are being constructed, and dredging operations are ongoing. This environment involves heavy machinery (cranes, excavators, piling rigs), moving vessels, underwater operations, and numerous workers in a highly dynamic and potentially dangerous setting. Safety is a top concern, especially with the high volume of daily activities and diverse contractor teams.
Before SentinelZone Safety: Site managers relied on physical barriers, safety cones, and manual supervision to enforce danger zones. Despite daily safety briefings, human error, fatigue, and the sheer scale of operations made it difficult to prevent workers from inadvertently straying into hazardous areas, leading to frequent near-misses and occasional accidents with heavy equipment. Tracking personnel in emergencies was also a challenge.
With SentinelZone Safety:
- Geo-Zone Definition: The project team uses SentinelZone Safety to digitally map the entire construction site. They define:
- Dynamic Exclusion Zones: Around active crane swing radii, excavation pits, and areas where piling rigs are operating. These zones automatically expand or contract as machinery moves.
- Restricted Access Zones: For areas with active welding (hot work permits required) or chemical storage.
- "No-Go" Zones: For unstable ground or active demolition areas.
- "Hard Hat Required" Zones: Designated areas where PPE compliance is critical.
- Worker Deployment: Every worker is equipped with a SentinelZone Safety wearable (a ruggedized smart badge with UWB/BLE) and their hardhat is fitted with a compact helmet camera.
- Real-time Monitoring & Alerts:
- Proximity Alert: A laborer inadvertently walks too close to an active excavator. The worker's smart badge immediately vibrates and emits an audible alert, while the excavator operator receives an in-cab warning. A notification also pops up on the supervisor's tablet, showing the laborer's exact location and the geo-zone breach.
- "Man Down" Alert: An offshore worker involved in jetty construction accidentally falls. The accelerometer in their wearable detects the fall, and an immediate "man down" alert, along with GPS coordinates, is sent to the emergency response team and nearest supervisor. The helmet cam automatically starts recording, providing visual context of the incident.
- PPE Compliance Check (Conditional Zone): As workers enter a "hot work" zone, SentinelZone Safety verifies (via integrated sensors or visual AI from helmet cams) if they are wearing the required flame-retardant clothing and welding masks. If not, an alert is triggered, and access can be temporarily denied until compliance is met.
- Emergency Muster: In case of a major site-wide emergency, the system can instantly identify all personnel location, helping to guide evacuation routes and quickly verify who has reached muster points, rather than relying on manual headcount.
Result: The Visakhapatnam port expansion project experiences a 40% reduction in "struck-by" incidents and near-misses, significantly improving site safety. Worker's compensation claims decrease, and the project avoids potential large fines from safety violations. Emergency response times are cut by over 50%, potentially saving lives. The comprehensive data collected by SentinelZone Safety allows the project management to analyze recurring safety risks and implement targeted training and operational changes, fostering a culture of proactive safety that enhances both worker well-being and project efficiency in one of India's critical infrastructure developments.
🚀 Ready to turn your passion for connected tech into real-world impact?
At Huebits, we don’t just teach IoT — we train you to build smart, scalable, and data-driven systems using the tech stacks powering today’s most innovative industries.
From edge devices to cloud platforms, you’ll gain hands-on experience designing end-to-end IoT architectures that collect, analyze, and respond in real time — built for deployment in cities, farms, factories, and homes.
🧠 Whether you're a student, aspiring IoT engineer, or future smart systems architect, our Industry-Ready IoT Program is your launchpad.
Master Python, Embedded C, MQTT, REST APIs, ESP32, Raspberry Pi, AWS IoT, Azure IoT Hub, and Grafana — all by building real-world IoT solutions that deliver results, not just data.
🎓 Next Cohort Starts Soon!
🔗 Join now and claim your seat in the IoT revolution powering tomorrow’s ₹1 trillion+ connected economy.
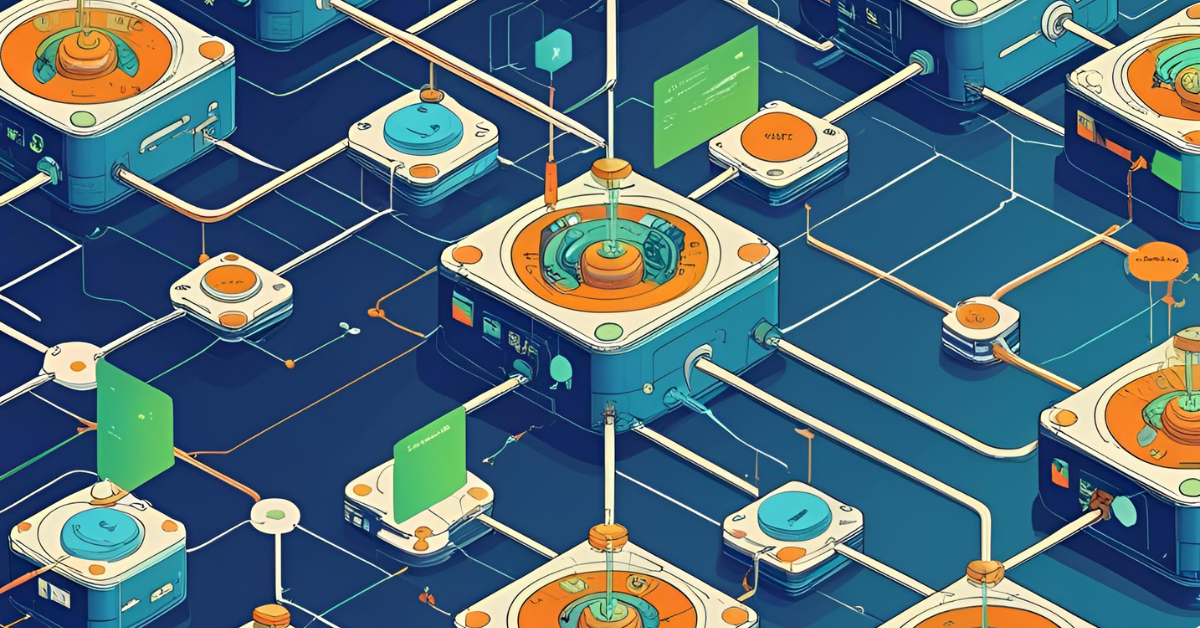
8.Process-Aware Digital Twins
Application Name: AuraTwin Dynamics
Overview:
AuraTwin Dynamics goes beyond traditional static digital representations to deliver truly Process-Aware Digital Twins. These aren't just digital copies; they are dynamic, AI-enriched simulations that learn and adapt with every new sensor reading, operational change, and environmental variable. Functioning as a "living blueprint" of physical assets, processes, and entire systems, AuraTwin Dynamics continuously synchronizes with the real world through real-time data streams from IIoT sensors, control systems, and human input. Powered by advanced AI and machine learning, it enables predictive analysis, prescriptive optimization, scenario planning, and virtual testing, allowing industrial operators to anticipate failures, optimize performance, and innovate with unprecedented precision and foresight.
Use Case:
AuraTwin Dynamics is invaluable for any industry dealing with complex, high-value assets or intricate processes where optimization, predictive capabilities, and risk reduction are paramount. Key use cases include:
- Continuous Process Industries (Chemical, Pharmaceutical, Oil & Gas, Power Generation):
- Process Optimization: Simulating changes in temperature, pressure, flow rates, or catalyst levels in real-time to identify optimal operating points that maximize yield, minimize energy consumption, or reduce emissions, without risking the actual plant.
- Predictive Quality: Predicting the quality of the final product based on real-time input parameters and adjusting upstream processes to ensure specifications are met.
- Abnormal Situation Management: Simulating the impact of potential failures (e.g., pump breakdown, valve stuck) to train operators, develop robust emergency response plans, and test automated shutdown sequences.
- Manufacturing & Assembly Lines:
- Throughput Optimization: Simulating changes in machine speed, buffer sizes, or robot pathing to identify bottlenecks and maximize production line efficiency.
- Predictive Maintenance: Combining sensor data from physical machines with their digital twin to predict component failures (e.g., motor bearing wear) with higher accuracy, allowing for just-in-time maintenance scheduling.
- New Product Introduction (NPI): Virtually testing new product designs and their manufacturability on the digital twin of the production line before committing to physical retooling.
- Infrastructure & Smart Cities (Ports, Airports, Smart Buildings):
- Traffic Flow Optimization (Ports): Simulating vessel movements, crane operations, and truck routes within a port digital twin to optimize cargo flow, reduce congestion, and predict delays.
- Energy Management (Buildings/Campuses): Creating a digital twin of a building's HVAC and lighting systems to optimize energy consumption based on occupancy, external weather, and utility prices.
- Predictive Maintenance of Infrastructure: Monitoring bridges, roads, or critical utilities via digital twins to predict structural degradation or system failures.
- Renewable Energy (Wind Farms, Solar Plants):
- Performance Optimization: Digital twins of wind turbines or solar arrays adapting to real-time weather conditions and component wear to optimize energy capture and predict maintenance needs.
- Grid Integration: Simulating the impact of renewable energy fluctuations on the grid and optimizing dispatch.
Tech Stack:
AuraTwin Dynamics demands a highly integrated and sophisticated tech stack:
- Data Ingestion & Integration:
- IIoT Connectivity: Protocols like OPC UA, MQTT, Modbus TCP for real-time data streaming from sensors (vibration, temperature, pressure, flow, current), PLCs, SCADA, DCS, and MES.
- Enterprise System Integration: APIs for ERP, CMMS, WMS, and LIMS (Laboratory Information Management Systems) to incorporate operational data, maintenance schedules, and quality results.
- External Data Sources: APIs for weather data, market prices, supply chain logistics, etc.
- Digital Twin Platform / Core Engine:
- 3D Modeling & Visualization: Advanced CAD/CAM software integration (e.g., Siemens NX, Dassault Systèmes CATIA) for creating high-fidelity 3D models of assets and environments.
- Physics-Based Simulation Engines: Tools like ANSYS, Abaqus, COMSOL, or custom simulation frameworks (e.g., based on Unity or Unreal Engine for visualization) to accurately model physical behaviors (fluid dynamics, thermodynamics, structural mechanics).
- Real-time Data Sync: Middleware and messaging queues (e.g., Kafka) to ensure continuous, low-latency synchronization between the physical asset and its digital twin.
- Graph Databases (Optional but Powerful): Neo4j, ArangoDB for representing complex relationships between assets, processes, and data points, enabling more intuitive querying and analysis.
- AI/ML & Advanced Analytics:
- Machine Learning Frameworks: TensorFlow, PyTorch, Scikit-learn for building models.
- Predictive Analytics: Regression models, time-series forecasting (LSTMs, Prophet, ARIMA) for predicting future states, performance degradation, or failures.
- Prescriptive Analytics: Reinforcement Learning (RL), optimization algorithms (linear programming, evolutionary algorithms) to recommend optimal actions or control parameters.
- Anomaly Detection: Unsupervised learning methods to detect deviations from normal behavior in real-time.
- Digital Twin Logic/Rules Engine: A component that takes AI/ML insights and translates them into actionable decisions or simulations within the twin.
- Cloud & Edge Computing:
- Cloud Infrastructure: AWS, Azure, GCP for scalable compute power required for complex simulations, data storage, and AI model training.
- Edge Computing: Lightweight AI models deployed at the edge (on industrial gateways or controllers) for immediate data processing and local closed-loop control based on digital twin insights, minimizing latency for critical actions.
- User Interface & Visualization:
- Interactive Dashboards: Web-based (React, Angular) or desktop applications providing real-time visualization of the digital twin, its key performance indicators (KPIs), predictions, and optimization recommendations.
- Augmented Reality (AR)/Virtual Reality (VR) Integration: For immersive interaction with the digital twin, enabling virtual walkthroughs, remote assistance, and overlaid real-time data on physical assets.
- Cybersecurity: Robust security protocols for data transmission, model integrity, and access control, especially given the connection to operational technology.
Impact/ROI:
AuraTwin Dynamics delivers transformative ROI across several strategic areas:
- Optimized Operational Efficiency (10-25% improvement): By simulating and optimizing processes in real-time, businesses can achieve higher throughput, reduce energy consumption, minimize waste, and improve resource utilization.
- Predictive Maintenance & Reduced Downtime (20-40% reduction): Accurate prediction of failures allows for proactive, just-in-time maintenance, drastically minimizing unplanned outages and associated costs.
- Faster Time-to-Market & Innovation: Rapid virtual prototyping and testing of new products, processes, or modifications without disrupting physical operations, accelerating innovation cycles.
- Enhanced Product Quality & Consistency: Real-time process adjustments based on digital twin insights ensure consistent product quality, reducing rework and material waste.
- Reduced Risk & Improved Safety: Simulating potential hazardous scenarios and training operators in a risk-free virtual environment enhances safety protocols and emergency preparedness.
- Cost Savings: Lower operational expenditures from optimized resource use, reduced maintenance, minimized scrap, and fewer warranty claims.
- Data-Driven Decision Making: Provides unprecedented insights into asset health, process performance, and future scenarios, empowering more informed and strategic decisions.
- Longer Asset Lifespan: Proactive maintenance and optimal operating conditions extend the life of high-value industrial equipment.
Real-World Example:
Consider a large-scale LNG (Liquefied Natural Gas) regasification terminal located near Visakhapatnam, Andhra Pradesh, India. This terminal receives LNG by ship, stores it, and then regasifies it to natural gas for distribution via pipelines. The process involves complex cryogenic operations, heat exchangers, pumps, compressors, and strict safety protocols. Optimizing energy consumption (for regasification and compression) and ensuring continuous, safe operation are paramount.
Before AuraTwin Dynamics: The terminal relied on a DCS (Distributed Control System) for real-time control, but optimization was largely based on historical data, operator experience, and periodic process simulations that didn't adapt in real-time. Predicting equipment failures, especially in cryogenic environments, was challenging, often leading to reactive maintenance or conservative, expensive scheduled shutdowns. Identifying optimal energy usage for regasification based on varying ambient temperatures and gas demand was a constant manual challenge.
With AuraTwin Dynamics:
- Living Digital Twin: AuraTwin Dynamics creates a comprehensive digital twin of the entire LNG regasification process, from the jetty and storage tanks to regasification units, compression stations, and gas export pipelines. This twin is continuously fed real-time data from thousands of IIoT sensors (temperature, pressure, flow rates, vibration, energy consumption) across all assets.
- Real-time Optimization & Energy Management:
- AuraTwin Dynamics' AI constantly analyzes real-time data from ambient temperature sensors, gas demand forecasts, and LNG tank levels. It runs simulations within the twin to dynamically determine the most energy-efficient configuration for the regasification units and compressors, adjusting parameters like seawater flow rates in heat exchangers to minimize power consumption while meeting gas demand.
- If there's a slight change in the LNG composition received, the twin immediately updates its models and recommends real-time adjustments to process parameters to maintain consistent gas quality and maximize energy efficiency.
- Predictive Maintenance & Anomaly Detection:
- The digital twin's AI monitors the vibration patterns and thermal signatures of critical pumps and compressors in real-time. If it detects a subtle anomaly (e.g., a specific frequency in vibration data that indicates early bearing wear) weeks before an actual failure, it alerts the maintenance team.
- The team can then simulate the pump's replacement within the digital twin to identify the least disruptive time for scheduled maintenance, considering operational demand and available resources, preventing an unplanned shutdown.
- Abnormal Situation Simulation & Training:
- Before a major maintenance turnaround or an emergency drill, operators can use the digital twin to simulate various failure scenarios (e.g., a sudden drop in a heat exchanger's performance, a major leak). This allows them to practice emergency response procedures in a risk-free virtual environment, improving their readiness and minimizing actual plant downtime during drills.
- The twin can also be used to test the impact of planned process changes before implementation, ensuring they don't negatively affect safety or efficiency.
Result:
The LNG regasification terminal in Visakhapatnam achieves a 15% reduction in energy consumption due to continuous, AI-driven process optimization, leading to significant operational cost savings. Unplanned downtime for critical equipment is reduced by 30-40%, ensuring reliable gas supply. The ability to simulate and test scenarios in real-time enhances safety protocols and significantly reduces the risk of operational incidents. The terminal operates with unprecedented efficiency and resilience, solidifying its role as a vital energy hub in the region.

9.AI-Optimized Material Flow Systems
Application Name: FlowSense AI
Overview:
FlowSense AI is a cutting-edge AI-Optimized Material Flow System designed to revolutionize the movement of goods, components, and raw materials within industrial and logistics environments. Moving beyond static configurations, FlowSense AI enables conveyor belts, robotic arms, Automated Guided Vehicles (AGVs), and other material handling equipment to adapt their operations in real-time based on a continuous stream of data. This intelligence is derived from demand forecasts, current stock levels, production schedules, and immediate sensor alerts (e.g., equipment status, blockage detection). Acting as the intelligent choreographer of internal logistics, FlowSense AI minimizes bottlenecks, optimizes throughput, reduces idle time, and ensures a seamless, highly efficient flow of materials, creating a truly responsive and agile supply chain within the factory or warehouse.
Use Case:
FlowSense AI is crucial for any industry that relies heavily on internal logistics and material handling, where efficiency directly impacts production costs, delivery times, and inventory levels. Key use cases include:
- Automotive Manufacturing:
- Just-in-Time Component Delivery: Dynamically adjusts the speed and routing of conveyor belts and AGVs to deliver specific components to assembly line workstations precisely when needed, minimizing on-line inventory.
- Body Shop Material Flow: Optimizes the movement of car body parts through welding and painting sections, adapting to variations in production speed or equipment availability.
- E-commerce Fulfillment Centers & Warehouses:
- Dynamic Order Picking & Packing: Re-routes orders to available picking robots or human pickers based on real-time order volume, inventory location, and available packing stations.
- Returns Processing Optimization: Intelligently directs returned items to inspection, re-shelving, or disposal stations based on product condition and current processing capacity.
- Food & Beverage Production:
- Ingredient Batching & Routing: Optimizes the flow of ingredients to different mixing tanks or processing lines based on recipes, batch sizes, and available tank capacity.
- Packaging Line Management: Adjusts conveyor speeds and robotic packing sequences based on product fill levels and packaging material availability to prevent bottlenecks.
- Electronics Manufacturing:
- PCB (Printed Circuit Board) Assembly: Fine-tunes the flow of PCBs between different SMT (Surface Mount Technology) machines, reflow ovens, and inspection stations based on machine status and quality checks.
- Component Kitting: Robotic arms pick and present specific component kits to assembly workers or automated machines based on real-time production needs.
- Mining & Bulk Material Handling:
- Conveyor Load Optimization: Dynamically adjusts conveyor belt speeds and feeder rates based on real-time material density, moisture content, and downstream processing capacity to prevent overloads or underutilization.
- Material Blending: Optimizes the flow from different stockpiles to achieve a desired blend ratio.
Tech Stack:
FlowSense AI integrates various technologies for sensing, intelligence, and execution:
- Data Acquisition (Sensors & IIoT):
- Throughput Sensors: Photoelectric sensors, laser scanners, vision systems (cameras with AI for object recognition, barcode/RFID reading) on conveyor belts and entry/exit points to track items.
- Weight & Volume Sensors: Load cells and volumetric scanners on conveyors and AGVs to measure material attributes.
- Machine Status Sensors: Integration with PLCs/SCADA systems to get real-time status of conveyors (speed, faults), robotic arms (operational status, error codes), and AGVs (location, battery, status).
- Inventory Sensors: RFID readers, ultrasonic sensors, LiDAR in storage areas for real-time stock levels.
- Wearables Integration (Optional): For human-robot collaboration insights or manual task completion status.
- Material Handling Equipment:
- Smart Conveyor Systems: Conveyor belts with variable speed drives, diversion gates, sorting mechanisms, and integrated sensors.
- Robotic Arms: Collaborative robots (cobots), industrial robots with vision systems, grippers, and end-of-arm tooling for picking, placing, and sorting.
- Automated Guided Vehicles (AGVs) / Autonomous Mobile Robots (AMRs): For flexible material transport, capable of dynamic path planning.
- Edge Computing:
- Edge Controllers/Gateways: Process raw sensor data locally, perform real-time analysis (e.g., detecting blockages, counting items), and execute immediate commands to material handling equipment, minimizing latency.
- Local AI/ML: Run lightweight AI models for immediate decision-making, such as dynamic lane changes for packages or adjusting robot pick speeds.
- Cloud Platform & Analytics:
- IoT Platform: AWS IoT Core, Azure IoT Hub, Google Cloud IoT for secure ingestion and management of aggregated data from edge devices.
- Time-Series Databases: For storing high-volume, real-time material flow data.
- Data Lake/Warehouse: For historical data, demand forecasts, and long-term analysis.
- AI/ML Core:
- Predictive Analytics: Forecasting future demand, potential bottlenecks, or equipment maintenance needs based on historical data and current trends.
- Prescriptive Analytics/Optimization: Reinforcement Learning, simulation-based optimization, discrete event simulation, and linear programming to determine optimal routes, speeds, and resource allocation.
- Anomaly Detection: Identifying unusual material flow patterns (e.g., unexpected jams, deviations from expected throughput).
- Demand Forecasting Models: Integrate with ERP/SCM systems to leverage demand forecasts for proactive adjustments.
- Workflow Orchestration & Integration:
- Central Control Layer: A software layer that receives insights from AI models and translates them into commands for the various material handling systems (conveyors, robots, AGVs) via industrial protocols (e.g., OPC UA, Modbus).
- APIs: For seamless integration with Manufacturing Execution Systems (MES), Warehouse Management Systems (WMS), Enterprise Resource Planning (ERP) systems, and supply chain management software.
- User Interface & Visualization:
- Digital Twin/Dashboard: A real-time 3D visualization of the material flow system, showing current status, bottlenecks, predicted issues, and AI-driven adjustments.
- Alerting System: Notifications to operators or supervisors for critical events or manual intervention requests.
Impact/ROI:
FlowSense AI delivers significant and measurable ROI by optimizing every aspect of material movement:
- Increased Throughput & Production Capacity (15-30% improvement): By eliminating bottlenecks and ensuring a continuous, optimized flow of materials.
- Reduced Operational Costs:
- Lower Labor Costs: Automating repetitive material handling tasks and optimizing human-robot collaboration.
- Reduced Energy Consumption: Dynamically adjusting conveyor speeds and equipment utilization based on real-time demand.
- Minimized Waste & Rework: Ensuring materials arrive at the right place, at the right time, in the correct quantity, reducing errors and material damage.
- Optimized Inventory Levels: Supporting just-in-time and just-in-sequence delivery strategies, reducing working capital tied up in inventory.
- Faster Order Fulfillment & Reduced Lead Times: Especially critical in e-commerce and fast-moving consumer goods.
- Enhanced Agility & Resilience: The system can quickly adapt to demand fluctuations, machine failures, or changes in production schedules, making the operation more robust.
- Improved Safety: Fewer human-machine interactions in dangerous material handling areas, and automated collision avoidance for AGVs.
- Better Space Utilization: Optimized flow reduces the need for large buffer zones and improves overall layout efficiency.
- Data-Driven Decision Making: Provides granular insights into material flow patterns, helping identify systemic issues and areas for further long-term optimization.
Real-World Example:
Consider a large-scale Fast-Moving Consumer Goods (FMCG) packaging plant in Visakhapatnam, Andhra Pradesh, India, producing various hygiene and food products. The plant has multiple packaging lines, each requiring a constant supply of different product batches, bottles, caps, labels, and cartons, which are moved via a complex network of conveyors, AGVs, and robotic palletizers. Demand for different products fluctuates significantly.
Before FlowSense AI: The plant operated on a fixed schedule for material delivery to each line. If a packaging line experienced a micro-stoppage, or if demand for a specific product unexpectedly surged, materials would either accumulate at the stoppage point (causing jams and waste) or lines would run out of components (leading to idle time). Manual intervention was often required to clear jams, re-route materials, or expedite deliveries, leading to inefficiency and production delays.
With FlowSense AI:
- Integrated Monitoring: FlowSense AI integrates with:
- IIoT Sensors: On all conveyor belts (speed, jam detection, item count), robotic arms (status, pick rate), and AGVs (location, battery, load).
- MES: For real-time production targets and line status.
- WMS: For current component inventory in the warehouse.
- ERP: For updated demand forecasts and order backlogs.
- Dynamic Adaptation:
- Scenario 1: Line Stoppage: Packaging Line 3 experiences a temporary blockage due to a faulty cap dispenser. FlowSense AI immediately detects the stoppage via conveyor sensors. Instead of materials piling up:
- It automatically slows down or temporarily diverts incoming product batches and packaging materials (bottles, caps) intended for Line 3 to a temporary buffer zone or re-routes them to an alternative, underutilized Line 4 if capable of handling the product.
- It dispatches an AGV with tools and spare parts to Line 3's location based on the MES fault code.
- Scenario 2: Demand Surge: The sales forecast for a specific handwash product suddenly increases by 20% overnight. FlowSense AI updates its internal models with this new demand. It then:
- Accelerates the inbound delivery of bottles, pumps, and liquid bulk from the warehouse to the relevant packaging line.
- Increases the speed of associated conveyors.
- Prioritizes the dispatch of palletizing robots for finished handwash cartons to the outbound loading docks, ensuring the higher demand is met without delay.
- Scenario 3: Robotic Arm Overload: A robotic arm on Line 1 responsible for placing labels is running at 95% capacity, approaching a bottleneck. FlowSense AI detects this via the robot's performance data. It proactively initiates a dynamic rebalancing:
- It might slightly reduce the inflow of products to Line 1 by adjusting upstream conveyor speeds or
- If a neighboring line's robotic arm is underutilized, it could trigger a small batch diversion, offloading some work to prevent Line 1's arm from becoming a hard bottleneck.
- Scenario 1: Line Stoppage: Packaging Line 3 experiences a temporary blockage due to a faulty cap dispenser. FlowSense AI immediately detects the stoppage via conveyor sensors. Instead of materials piling up:
Result:
The FMCG plant in Visakhapatnam achieves a 25% increase in overall production throughput by virtually eliminating bottlenecks and material flow inefficiencies. Operational costs are reduced by 18% due to optimized energy use, less material waste from jams, and more efficient labor allocation. The plant becomes significantly more agile, able to quickly respond to demand fluctuations and production disruptions, ensuring consistent product availability in the competitive FMCG market of Andhra Pradesh.
🚀 Ready to turn your passion for connected tech into real-world impact?
At Huebits, we don’t just teach IoT — we train you to build smart, scalable, and data-driven systems using the tech stacks powering today’s most innovative industries.
From edge devices to cloud platforms, you’ll gain hands-on experience designing end-to-end IoT architectures that collect, analyze, and respond in real time — built for deployment in cities, farms, factories, and homes.
🧠 Whether you're a student, aspiring IoT engineer, or future smart systems architect, our Industry-Ready IoT Program is your launchpad.
Master Python, Embedded C, MQTT, REST APIs, ESP32, Raspberry Pi, AWS IoT, Azure IoT Hub, and Grafana — all by building real-world IoT solutions that deliver results, not just data.
🎓 Next Cohort Starts Soon!
🔗 Join now and claim your seat in the IoT revolution powering tomorrow’s ₹1 trillion+ connected economy.
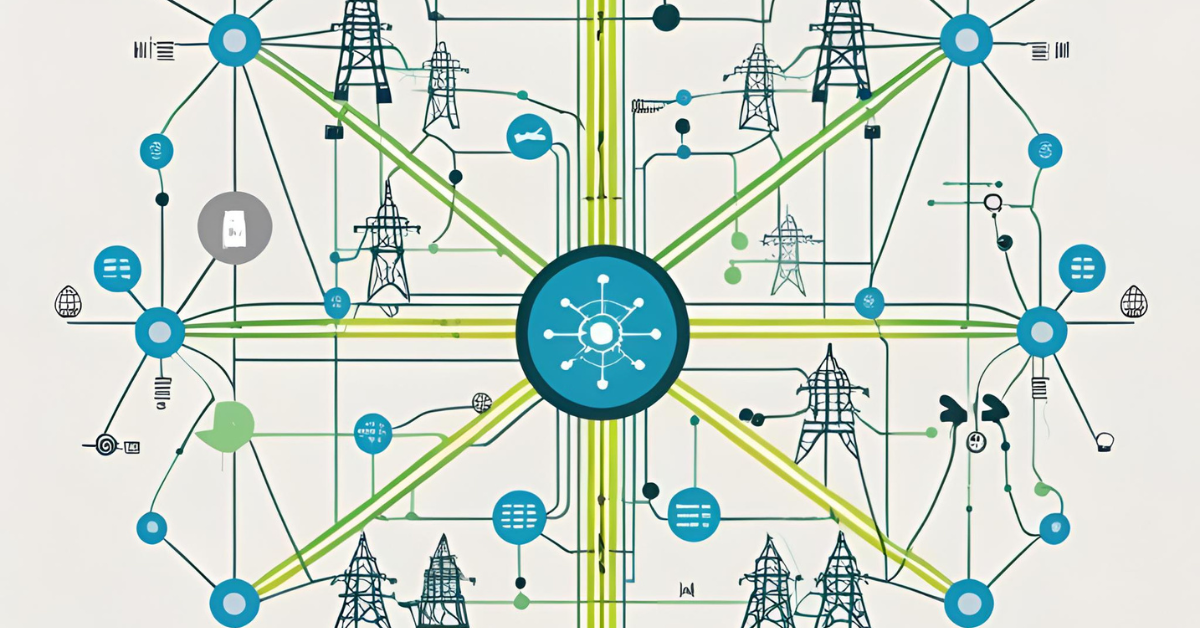
10.Smart Power Load Shedding Networks
Application Name: GridGuardian AI
Overview
GridGuardian AI is an intelligent, Smart Power Load Shedding Network that transforms industrial energy management from reactive to proactive. When the electrical grid is strained due to peak demand, generation shortages, or equipment failures, GridGuardian AI leverages IoT-enabled smart devices and machine intelligence to dynamically and autonomously manage energy consumption within industrial facilities. Unlike traditional, often disruptive, manual load shedding, GridGuardian AI allows machines to "know how to chill"—prioritizing critical operations while strategically shedding non-essential loads or reducing consumption in real-time without causing brownouts or operational halts. This advanced system not only ensures grid stability and avoids costly penalties from power disruptions but also significantly slashes energy bills through optimized, data-driven consumption.
Use Case:
GridGuardian AI is crucial for energy-intensive industries and facilities that cannot tolerate full power outages but need to manage demand proactively, especially in regions with fluctuating grid stability or high peak-demand charges. Key use cases include:
- Manufacturing Plants (Automotive, Steel, Cement, Textiles):
- Dynamic Demand Response: During peak hours or grid stress, automatically reduces power to non-critical processes (e.g., HVAC in non-production areas, lighting in unoccupied zones, less critical heating elements, non-essential motors), while maintaining core production.
- Scheduled Load Shifting: Shifts energy-intensive processes (e.g., large motor starts, batch heating) to off-peak hours when electricity is cheaper, or when grid capacity is higher.
- Brownout Prevention: Prevents entire lines from tripping during voltage sags by quickly shedding non-critical loads.
- Data Centers:
- Cooling Optimization: Dynamically adjusts cooling unit fan speeds or chiller operations based on server load and real-time power grid conditions, shedding non-critical cooling during grid stress.
- Non-Essential Load Reduction: Prioritizes server power while reducing power to office lighting, auxiliary equipment, or less critical backup systems during a grid event.
- Commercial Buildings & Campuses (Large Industrial Complexes, Ports):
- HVAC & Lighting Management: Intelligently reduces power to air conditioning, heating, and non-essential lighting systems across vast areas without significantly impacting comfort or safety, based on occupancy, time of day, and grid signals.
- Electric Vehicle (EV) Charging Management: Pauses or reduces charging rates for non-urgent EV fleet vehicles during peak grid stress.
- Water Treatment & Pumping Stations:
- Pump Optimization: Dynamically adjusts pump speeds or cycles for water intake/outflow based on water levels and grid conditions, ensuring critical supply while minimizing energy costs.
- Phased Operation: Staggers the operation of multiple pumps to avoid simultaneous high-current draws.
- Mining & Heavy Industry:
- Conveyor/Crusher Optimization: Reduces power consumption of non-critical conveyors or pre-crushing stages during peak grid demand while ensuring essential operations continue.
- Ventilation Systems: Dynamically adjusts fan speeds in non-critical ventilation shafts based on air quality monitoring and grid availability.
Tech Stack:
GridGuardian AI requires a robust interplay of IoT, AI, and power management technologies:
- IoT-Enabled Smart Devices (End Nodes):
- Smart Circuit Breakers/Relays: IoT-enabled circuit breakers that can be remotely controlled to open/close circuits and monitor power flow.
- Smart Meters/Sub-Meters: Devices (e.g., Schneider Electric, Siemens) at equipment level, zone level, and feeder level to measure real-time voltage, current, power factor, and energy consumption.
- Motor Controllers (VFDs): Variable Frequency Drives that can precisely control motor speed and power consumption.
- Smart HVAC Controls: IoT-enabled thermostats, chillers, and fan units.
- Smart Lighting Controls: Dimmable lights and smart switches.
- Environmental Sensors: Temperature, humidity, occupancy sensors for contextual data.
- Communication Network:
- Industrial IoT (IIoT) Connectivity: Wired Ethernet (Modbus TCP, PROFINET), industrial Wi-Fi, LoRaWAN, cellular (5G/LTE-M) for reliable and secure data transmission between smart devices and the central platform.
- Dedicated Low-Latency Links: For critical load control commands.
- Edge Computing:
- Edge Gateways/Controllers: Deployed within the facility to aggregate data from local IoT devices, perform real-time power analytics, and execute immediate load shedding commands, minimizing latency.
- Local AI Models: Run lightweight AI for rapid anomaly detection in power consumption or voltage fluctuations, and for autonomous initial load shedding actions based on predefined policies.
- Cloud Platform & AI/ML Core:
- IoT Platform: AWS IoT Core, Azure IoT Hub, Google Cloud IoT for secure ingestion and management of high-volume power data.
- Time-Series Databases: For storing granular power consumption data.
- Data Lake/Warehouse: For historical energy data, utility tariffs, and long-term analysis.
- AI/ML Engine:
- Predictive Demand Forecasting: ML models (e.g., LSTMs, Prophet) to predict the facility's power demand and grid strain based on production schedules, weather, and historical data.
- Load Prioritization Algorithms: AI-driven algorithms (e.g., Reinforcement Learning, optimization algorithms) that dynamically determine which loads to shed or curtail based on pre-configured priorities, operational constraints, and real-time grid signals.
- Anomaly Detection: Identifies unusual power consumption patterns or potential equipment faults.
- Distributed Control Optimization: Algorithms that manage complex interactions between various loads to achieve desired shedding without disrupting critical processes.
- Integration:
- Utility Grid Integration: APIs/protocols (e.g., OpenADR) to receive real-time signals from the utility provider regarding grid conditions, demand response events, or peak pricing.
- MES/ERP Integration: To understand production schedules, critical path operations, and current equipment status.
- BMS (Building Management System) Integration: For holistic energy management in industrial complexes.
- User Interface & Control:
- Energy Management Dashboard: Real-time visualization of power consumption, load shedding events, energy cost savings, and grid status.
- Policy Configuration: Interface for defining load shedding policies, load priorities (critical, semi-critical, non-critical), and thresholds.
- Alerting System: Notifications for load shedding events, grid anomalies, or system failures.
Impact/ROI:
GridGuardian AI delivers significant and multi-faceted ROI for industrial facilities:
- Substantial Energy Bill Savings (10-25%):
- Reduced Peak Demand Charges: By intelligently shedding or shifting loads during expensive peak hours, significantly lowering the highest demand spikes.
- Participation in Demand Response Programs: Earning incentives from utilities for voluntarily reducing consumption during grid stress.
- Optimized Energy Consumption: Continuous, data-driven optimization of energy use across all connected assets.
- Avoided Production Loss due to Brownouts/Outages: Proactive load shedding prevents full power disruptions, ensuring continuous operation of critical processes and avoiding costly restarts or damage to equipment.
- Enhanced Grid Resilience & Stability: Contributing to the overall stability of the local grid, especially beneficial in regions with unreliable power supply.
- Reduced Carbon Footprint & ESG Compliance: Optimizing energy use naturally leads to lower greenhouse gas emissions, improving sustainability reporting and ESG ratings.
- Improved Equipment Lifespan: Smoother power management reduces stress on electrical equipment, potentially extending its operational life.
- Automated & Precise Control: Eliminates manual, often imprecise, load shedding, ensuring only non-critical loads are affected and critical operations remain uninterrupted.
- Better Resource Utilization: Energy resources are used more efficiently and intelligently across the facility.
Real-World Example:
Consider a large-scale textile manufacturing plant in Visakhapatnam, Andhra Pradesh, India. This plant operates 24/7, with energy-intensive processes like dyeing, drying, and spinning. Andhra Pradesh, like many states in India, experiences periods of high peak demand, leading to higher electricity tariffs during these hours and occasional grid strain that can result in voltage fluctuations or forced load shedding by the utility. Even a brief power dip can halt production lines, requiring costly restarts and impacting fabric quality.
Before GridGuardian AI: The plant's energy management was relatively static. They paid high peak demand charges. During grid stress, they might receive a manual alert from the utility to reduce load, often requiring supervisors to manually shut down entire sections or large machines, disrupting production and potentially damaging equipment from abrupt shutdowns. Reactive measures were the norm.
With GridGuardian AI:
- Smart Device Integration: The plant integrates GridGuardian AI by installing smart sub-meters on all major energy-consuming equipment (dyeing machines, large motors for spinning, industrial dryers, HVAC units in non-production areas). These meters and associated smart circuit breakers/VFDs are connected to edge gateways.
- Load Prioritization: The plant defines load priorities within GridGuardian AI:
- Critical: Spinning machines, main process control systems (must never shut down).
- Semi-Critical: Dyeing machines (can be briefly paused or reduced in intensity), some auxiliary pumps.
- Non-Critical: Large ventilation fans in less critical areas, warehouse lighting during daylight, water heaters for non-process uses.
- Real-time Grid & Demand Monitoring: GridGuardian AI continuously monitors the plant's real-time energy consumption, local grid voltage stability, and receives demand response signals from the utility via API. It also uses its AI to forecast the plant's own internal peak demand based on production schedules.
- Autonomous Load Shedding & Shifting:
- Scenario 1: Peak Tariff Hour/Grid Strain: At 5:00 PM, GridGuardian AI detects that the local grid is under stress and the peak tariff period has begun. It immediately initiates a pre-programmed, intelligent load shedding sequence:
- It reduces the fan speed of non-critical HVAC units by 20%.
- It dims warehouse lighting by 30% where ambient light is sufficient.
- It slightly reduces the power consumption of auxiliary motors in the dyeing section that are currently running below full capacity, without affecting quality.
- Crucially, it does not impact the spinning machines or core dyeing processes, maintaining production continuity.
- Scenario 2: Impending Brownout: If a sudden voltage dip is detected (signaling an impending brownout), GridGuardian AI acts within milliseconds, automatically shedding predefined non-critical loads (e.g., temporarily pausing a non-essential water pump, reducing power to cafeteria kitchen equipment) to stabilize the plant's internal grid and prevent a full trip of the main breakers, protecting sensitive machinery.
- Scenario 3: Demand Shifting: The AI identifies that pre-heating large drying ovens for the next day can be optimally done during the lowest-tariff hours (e.g., 2 AM - 4 AM) when grid capacity is abundant. It automatically schedules these energy-intensive actions for those hours, reducing the plant's overall peak demand during the day.
- Scenario 1: Peak Tariff Hour/Grid Strain: At 5:00 PM, GridGuardian AI detects that the local grid is under stress and the peak tariff period has begun. It immediately initiates a pre-programmed, intelligent load shedding sequence:
Result: The textile plant in Visakhapatnam achieves a 17% reduction in its overall electricity bill, primarily through lower peak demand charges and participation in utility demand response programs. It virtually eliminates production losses due to grid fluctuations or forced load shedding, ensuring consistent fabric quality and delivery schedules. The plant's improved energy efficiency also boosts its ESG profile, enhancing its reputation in the region.
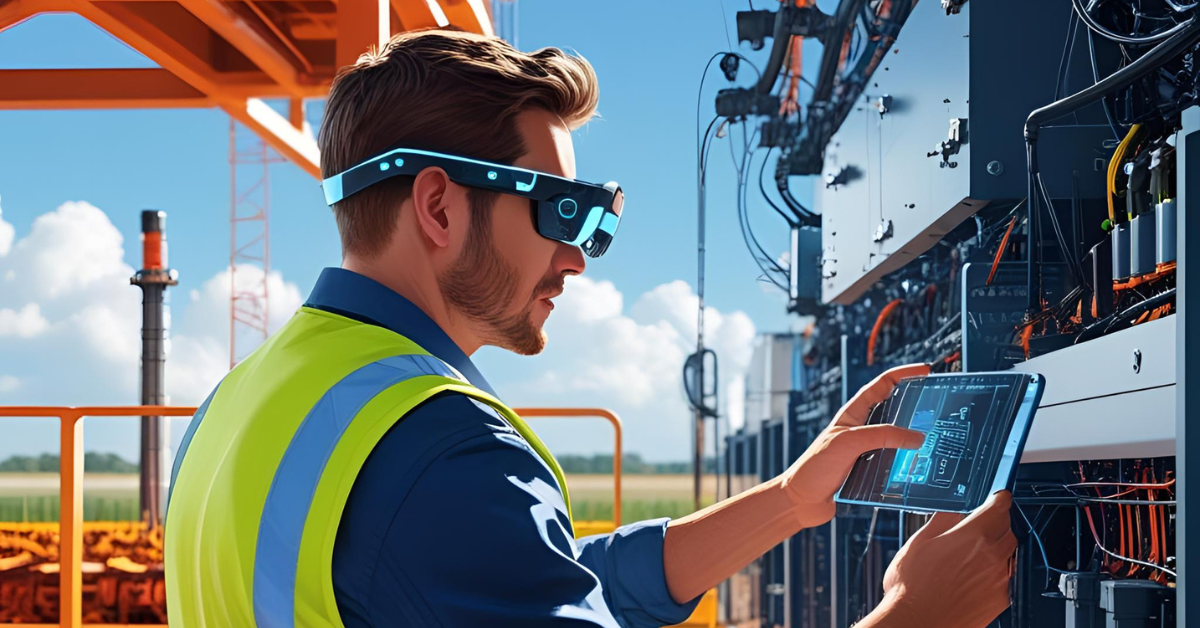
11.Augmented Industrial Field Support via AR IoT
Application Name: VisionPro Assist
Overview:
VisionPro Assist is an advanced Augmented Industrial Field Support via AR IoT solution that revolutionizes maintenance, repair, and operational tasks in industrial settings. It eliminates the need for bulky paper manuals and guesswork by beaming real-time operational data, step-by-step maintenance instructions, 3D schematics, and remote expert guidance directly into the field of vision of frontline technicians through smart glasses. By overlaying digital information onto the physical world, VisionPro Assist empowers field personnel to execute complex procedures with unprecedented accuracy, efficiency, and safety. This integrated AR and IoT system reduces human error, accelerates troubleshooting, enhances training, and significantly minimizes equipment downtime.
Use Case:
VisionPro Assist is indispensable for industries with complex machinery, critical uptime requirements, skilled labor shortages, or distributed assets where on-site expertise is costly or unavailable. Key use cases include:
- Manufacturing & Assembly (e.g., Automotive, Aerospace, Electronics):
- Complex Machine Assembly/Disassembly: Guides technicians through intricate assembly or disassembly sequences for large machinery, displaying torque specifications, tool requirements, and part orientation directly in their view.
- Quality Control & Inspection: Overlays digital checklists and tolerance ranges on physical products, allowing technicians to quickly identify defects or verify specifications with precision.
- Robot Calibration & Maintenance: Provides real-time data from robot sensors and guides technicians through calibration procedures or fault diagnosis.
- Energy & Utilities (Power Plants, Wind Farms, Oil & Gas Rigs):
- Turbine Maintenance: Guides field engineers through complex maintenance or troubleshooting of wind turbines or gas turbines, visualizing internal components and real-time operational data (e.g., vibration, temperature).
- Substation Equipment Repair: Provides step-by-step instructions for repairing high-voltage transformers or circuit breakers, enhancing safety and accuracy.
- Pipeline Inspection & Repair: Superimposes pipeline schematics and real-time pressure/flow data onto the physical pipeline, assisting in leak detection and repair.
- Logistics & Warehouse Operations:
- Automated Material Handling System Repair: Guides technicians through troubleshooting complex conveyor systems, sorters, or robotic picking systems, displaying diagnostics and repair steps.
- Forklift/AGV Maintenance: Provides interactive 3D models and maintenance checklists for complex vehicle systems.
- Mining & Heavy Machinery:
- Drill Rig / Excavator Maintenance: Guides technicians through complex hydraulic system repairs or engine diagnostics on massive mining equipment in remote or hazardous environments.
- Preventive Maintenance Checks: Provides interactive checklists and data entry fields directly in the field of view for routine inspections.
- Healthcare (Medical Equipment Maintenance):
- Diagnostic Imaging Machine Repair: Guides biomedical engineers through the repair of MRI, CT scanners, or X-ray machines, overlaying digital schematics and diagnostic information.
- Surgical Robot Maintenance: Provides precise, step-by-step instructions for maintaining highly sensitive and critical surgical robotics.
Tech Stack:
VisionPro Assist leverages a powerful blend of AR hardware, IoT, cloud computing, and AI:
- Augmented Reality Hardware:
- Industrial Smart Glasses: Ruggedized, hands-free AR glasses (e.g., Microsoft HoloLens, RealWear, Vuzix) with high-resolution displays, integrated cameras, microphones, and speakers. Key features include comfortable wear with PPE, long battery life, and robust environmental resistance.
- Eye/Hand Tracking: Integrated sensors for precise interaction with virtual content.
- IoT & Data Integration:
- IIoT Sensors: Networked sensors on machinery providing real-time data streams (e.g., vibration, temperature, pressure, current, operational status, error codes, diagnostic alerts).
- IoT Gateways: Securely collect and transmit sensor data from OT networks to edge and cloud platforms.
- SCADA/MES/CMMS Integration: APIs or connectors to pull operational data, work orders, maintenance history, spare parts inventory, and equipment manuals from existing enterprise systems.
- Edge Computing:
- Local Processing: Lightweight AR rendering and initial data processing can occur on the smart glasses or a connected edge device to minimize latency.
- Real-time Object Recognition: Edge AI models for rapid recognition of equipment or components being viewed, triggering context-specific information overlay.
- Cloud Platform & AI/ML:
- Cloud Infrastructure: Scalable compute and storage (AWS, Azure, GCP) for hosting AR content, digital twin models, and AI analytics.
- Digital Twin Platform: A virtual replica of physical assets that streams real-time data and can be used to generate interactive 3D overlays for the AR glasses.
- Content Management System (CMS): For managing and deploying 3D models, step-by-step instructions, videos, and diagnostic flows.
- AI/ML for Contextual Awareness & Optimization:
- Computer Vision: For precise object recognition, alignment of digital content, and potentially identifying unsafe conditions or incorrect procedures from the camera feed.
- Natural Language Processing (NLP): For voice commands and intelligent search of knowledge bases.
- Predictive Diagnostics: AI analyzes IoT data to predict potential failures and provide proactive maintenance instructions.
- Remote Assistance & Collaboration:
- Live Video & Audio Streaming: Enables remote experts to see exactly what the field technician sees, providing real-time annotations, drawing guides, and voice instructions directly into the technician's field of view.
- Annotation Tools: Shared drawing and pointing tools for precise guidance.
- File Sharing: Ability to share documents, schematics, or video clips instantly.
- User Interface & Experience:
- Intuitive AR Interface: Designed for hands-free operation via voice commands, gestures, or head movements.
- Context-Aware Information: Automatically displays relevant information based on the technician's gaze, location, and the equipment being viewed.
- Workflow Integration: Seamlessly guides technicians through workflows, logging completed steps and capturing necessary data/images.
Impact/ROI:
VisionPro Assist delivers substantial and quantifiable ROI:
- Reduced Mean Time To Repair (MTTR) (20-50% improvement): Technicians can diagnose and fix issues significantly faster with real-time guidance and data.
- Increased First-Time Fix Rate (15-30% improvement): Access to accurate, up-to-date information and expert support minimizes errors and repeat visits.
- Reduced Equipment Downtime (up to 20%): Faster repairs mean critical assets spend less time offline, boosting productivity.
- Lower Travel Costs for Experts (Significant Savings): Remote expert support eliminates the need for specialists to travel to distant sites for every complex issue.
- Accelerated Workforce Training & Upskilling: New technicians can learn complex procedures much faster on the job with interactive AR guidance, reducing training time and costs.
- Improved Safety (Reduced Accidents): Clear, hands-free instructions and real-time hazard alerts reduce human error and exposure to risks.
- Enhanced Data Capture & Audit Trails: Automated logging of steps, images, and video during maintenance provides detailed records for compliance and post-mortem analysis.
- Increased Technician Productivity & Job Satisfaction: Empowered technicians work more efficiently and feel more confident, leading to higher morale and retention.
- Improved Knowledge Transfer & Retention: Expert knowledge is digitized and made accessible, preventing knowledge loss due to retirement or attrition.
Real-World Example:
Consider a large-scale steel manufacturing plant in Visakhapatnam, Andhra Pradesh, India. This plant operates massive machinery like blast furnaces, rolling mills, and continuous casting machines, which are prone to complex breakdowns. When a critical machine fails, it results in significant production losses. The plant often faces challenges with skilled maintenance technicians for specialized equipment, sometimes requiring experts to fly in from other cities or even countries, leading to long downtimes.
Before VisionPro Assist: When a complex issue arose in the rolling mill (e.g., a specific gear assembly failure), a maintenance technician would rely on bulky paper manuals, 2D schematics, and phone calls with remote experts. Diagnosing the exact problem could take hours, and disassembling the machinery was slow, prone to errors, and required constant cross-referencing of documents. An expert might need to travel physically, causing days of delay and huge travel expenses.
With VisionPro Assist:
- Immediate Anomaly Detection: IIoT sensors on the rolling mill detect an unusual vibration pattern and send an alert with diagnostic codes to the plant's CMMS and VisionPro Assist platform.
- AR-Guided Diagnosis: A field technician puts on their VisionPro Assist smart glasses. As they look at the rolling mill, the glasses immediately recognize the specific machine and overlay its real-time operational data (e.g., temperature of bearings, motor RPMs) and the diagnostic error code.
- The system then projects interactive 3D models of the rolling mill's internal components directly onto the physical machine, allowing the technician to see "through" the casing to identify the suspected faulty gear assembly.
- Step-by-Step Instructions: The AR glasses display animated, step-by-step instructions for troubleshooting the specific error code, showing where to place probes, which bolts to loosen, and in what sequence. Voice commands allow the technician to move through steps hands-free.
- Remote Expert Collaboration: If the technician encounters an unforeseen challenge or needs confirmation, they can initiate a live video call through the smart glasses. A senior engineer located in Hyderabad (or even Europe) sees the technician's exact field of view in real-time.
- The remote expert can then draw digital annotations (arrows, circles) directly onto the technician's view, highlighting specific components, pointing to hidden fasteners, or confirming correct readings, eliminating miscommunication.
- The expert can also pull up historical maintenance logs or more detailed schematics and share them as overlays in the technician's view.
- Automated Documentation: As the technician completes each step, VisionPro Assist automatically logs the actions, captures photos/videos, and updates the work order in the CMMS, ensuring accurate documentation for compliance and future reference.
Result:
The steel plant in Visakhapatnam experiences a 45% reduction in MTTR for complex machinery breakdowns in the rolling mill. The first-time fix rate improves by 30%, leading to significantly less rework. The need for expert travel is reduced by over 70%, saving substantial costs and minimizing delays. Overall, the plant experiences less unplanned downtime, leading to millions of dollars in increased production output and a safer, more efficient maintenance operation. New technicians are onboarded and become proficient much faster due to the hands-on, guided training provided by VisionPro Assist.
🚀 Ready to turn your passion for connected tech into real-world impact?
At Huebits, we don’t just teach IoT — we train you to build smart, scalable, and data-driven systems using the tech stacks powering today’s most innovative industries.
From edge devices to cloud platforms, you’ll gain hands-on experience designing end-to-end IoT architectures that collect, analyze, and respond in real time — built for deployment in cities, farms, factories, and homes.
🧠 Whether you're a student, aspiring IoT engineer, or future smart systems architect, our Industry-Ready IoT Program is your launchpad.
Master Python, Embedded C, MQTT, REST APIs, ESP32, Raspberry Pi, AWS IoT, Azure IoT Hub, and Grafana — all by building real-world IoT solutions that deliver results, not just data.
🎓 Next Cohort Starts Soon!
🔗 Join now and claim your seat in the IoT revolution powering tomorrow’s ₹1 trillion+ connected economy.
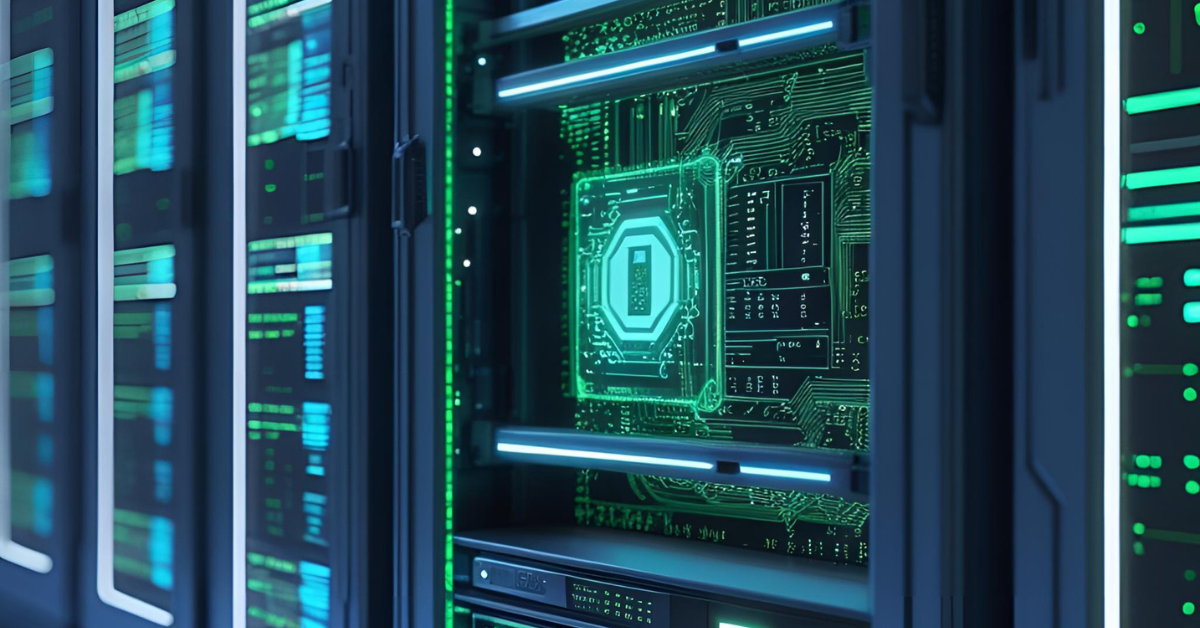
12.Post-Quantum Secure Industrial Networks
Application Name: QuantumFortress Industrial
Overview:
QuantumFortress Industrial is a pioneering solution for Post-Quantum Secure Industrial Networks, designed to safeguard the critical data and operational integrity of Industry 4.0 environments against the looming threat of quantum computing. As factories become increasingly digital and interconnected through IIoT, they transform into vast digital fortresses—making their data, control systems, and intellectual property vulnerable to advanced computational attacks. QuantumFortress Industrial ensures that all IoT data is wrapped in next-generation encryption, leveraging cryptosystems resistant to both current classical and future quantum algorithms. It establishes an impenetrable shield around industrial communications, data at rest, and device identities, providing an unparalleled level of security that future-proofs the digital factory against the most sophisticated cyber threats.
Use Case:
QuantumFortress Industrial is indispensable for any industrial sector where data breaches, intellectual property theft, operational sabotage, or long-term data integrity are critical concerns, especially in light of the impending quantum computing era. Key use cases include:
- Critical Infrastructure (Energy, Water, Transportation):
- Grid Control & SCADA Systems: Securing communication between control centers and remote power generators, substations, and water treatment facilities to prevent state-sponsored attacks or sabotage.
- Nuclear Facilities: Protecting highly sensitive operational data and control commands from sophisticated adversaries, ensuring national security.
- Defense & Aerospace Manufacturing:
- Intellectual Property (IP) Protection: Safeguarding proprietary designs, manufacturing processes, and R&D data from espionage, both during transmission and at rest on IIoT devices.
- Supply Chain Integrity: Ensuring the authenticity and integrity of components throughout the complex supply chain, preventing counterfeit parts.
- Pharmaceutical & Biotech Manufacturing:
- Formula & Process Protection: Protecting highly valuable drug formulas, manufacturing processes, and clinical trial data from theft.
- Data Integrity for Compliance: Ensuring that audit trails and batch records remain immutable and trustworthy for regulatory compliance.
- Automotive Manufacturing (Connected & Autonomous Vehicles):
- Secure OTA Updates: Ensuring that firmware updates for connected vehicles and factory robots are delivered securely and cannot be tampered with by quantum-enabled attackers.
- IP of Manufacturing Robotics & AI Algorithms: Protecting the highly valuable algorithms and configurations that drive advanced manufacturing processes.
- Advanced Manufacturing & High-Value Production:
- Precision Robotics Control: Securing real-time control commands to highly precise robots to prevent manipulation or sabotage that could lead to product defects or equipment damage.
- Protection of Digital Twin Data: Ensuring the integrity and confidentiality of the massive datasets and models used by digital twins.
- Financial & Sensitive Data Processing within Industrial Systems:
- Secure Payment & Transaction Processing: For automated material procurement or smart contract execution on the factory floor.
Tech Stack:
QuantumFortress Industrial integrates advanced cryptographic techniques, robust network architecture, and continuous monitoring:
- Post-Quantum Cryptography (PQC) Algorithms:
- Key Establishment: Using PQC algorithms like Kyber (for key exchange) to establish secure communication channels.
- Digital Signatures: Using PQC algorithms like Dilithium or Falcon (for digital signatures) to authenticate devices, users, and data integrity.
- Symmetric Encryption: Continuing to use strong symmetric encryption (e.g., AES-256) but with keys derived from PQC-secured key exchanges.
- Secure Hardware (Hardware Root of Trust):
- Trusted Platform Modules (TPMs) / Hardware Security Modules (HSMs): Embedded in IIoT devices, gateways, and servers to provide a hardware root of trust, secure key storage, and cryptographic acceleration.
- Secure Elements: Dedicated hardware for storing cryptographic keys and executing secure boot processes on edge devices.
- Network Segmentation & Zero Trust Architecture:
- Micro-Segmentation: Dividing the industrial network into small, isolated segments to limit the lateral movement of potential threats.
- Zero Trust: All devices and users are continuously authenticated and authorized, regardless of their location, with least-privilege access enforced.
- Secure Boot & Firmware Integrity:
- Cryptographically Signed Firmware: Ensuring that only authorized and untampered firmware can run on IIoT devices, validated with PQC digital signatures.
- Remote Attestation: Continuously verifying the integrity and security posture of remote IIoT devices.
- Secure Communication Protocols:
- TLS 1.3 with PQC Extensions: Implementing TLS (Transport Layer Security) with PQC algorithms for secure communication channels between devices, gateways, and cloud services.
- PQC-Enabled VPNs: For secure remote access to industrial networks.
- Identity and Access Management (IAM):
- PQC-Secure PKI (Public Key Infrastructure): Establishing a PKI that issues and manages digital certificates based on PQC algorithms for device and user authentication.
- Multi-Factor Authentication (MFA): With PQC-resistant methods where applicable.
- Security Monitoring & Orchestration:
- Security Information and Event Management (SIEM): Aggregating security logs and alerts from all network components for centralized monitoring and threat detection.
- Security Orchestration, Automation, and Response (SOAR): Automating responses to detected threats, such as isolating compromised devices or rerouting traffic.
- Threat Intelligence Integration: Continuously updating threat models with the latest intelligence on quantum threats and attack vectors.
- Quantum Key Distribution (QKD) (Optional for Ultra-Sensitive Links):
- For extremely critical, short-distance point-to-point links (e.g., between a control center and a power plant), QKD can provide information-theoretically secure key exchange, although its practicality for distributed IIoT is limited currently.
Impact/ROI:
QuantumFortress Industrial provides unparalleled security benefits, leading to significant ROI:
- Future-Proof Cybersecurity: Protection against "Harvest Now, Decrypt Later" attacks, where encrypted data is collected today to be decrypted by future quantum computers. This safeguards sensitive data and IP for decades to come.
- Reduced Risk of Cyberattacks & Breaches: A robust defense against sophisticated adversaries (e.g., nation-state actors) targeting critical industrial infrastructure, preventing costly downtime, data loss, and operational sabotage.
- Ensured Operational Continuity & Safety: By securing control systems and critical communications, the system guarantees the integrity of operational commands, preventing accidents, equipment damage, and production halts.
- Enhanced Data Integrity & Trust: Verifiable authenticity and integrity of all data (sensor readings, production logs, maintenance records) are maintained, crucial for compliance, quality control, and legal purposes.
- Protection of Intellectual Property (IP): Safeguarding proprietary manufacturing processes, product designs, and R&D secrets, which are a company's most valuable assets.
- Compliance with Evolving Regulations: Proactive adoption of post-quantum security prepares organizations for anticipated future cybersecurity regulations and industry standards.
- Reduced Financial & Reputational Damages: Avoiding the massive costs associated with cyberattacks, including recovery expenses, regulatory fines, legal fees, and severe damage to brand reputation and customer trust.
- Competitive Advantage: Demonstrating superior security postures can be a key differentiator, especially for defense contractors, pharmaceutical companies, or high-value manufacturing.
Real-World Example:
Consider a newly constructed, highly automated smart port terminal in Visakhapatnam, Andhra Pradesh, India. This terminal relies heavily on IIoT-connected cranes, AGVs, automated gates, and an integrated Terminal Operating System (TOS) to manage millions of tons of cargo annually. The communication channels carrying real-time crane movements, cargo manifests, shipping schedules, and customs data are incredibly valuable and sensitive, making the port a prime target for cyberattacks by state-sponsored actors or criminal organizations seeking to disrupt trade or steal cargo information.
Before QuantumFortress Industrial: The port's network uses standard, strong classical encryption (like RSA and ECC). While secure against current classical computers, this data could theoretically be harvested and stored by an adversary today, with the expectation of decrypting it years later when powerful quantum computers become available. A successful attack could disrupt port operations, reroute cargo, or compromise sensitive trade data.
With QuantumFortress Industrial:
- PQC-Enabled IIoT Devices: All newly deployed IIoT devices (sensors on cranes, AGVs, gates, smart cameras, environmental monitors) are equipped with secure hardware modules that implement PQC algorithms (e.g., Kyber for key exchange, Dilithium for digital signatures).
- Secure Boot & Attestation: Each device undergoes a secure boot process verified by PQC signatures. Continuously, the devices perform remote attestation, proving their software and hardware integrity to the central QuantumFortress platform.
- Quantum-Resistant Communication: When a crane's control system communicates with the TOS, or an AGV sends its real-time position data, the communication session is established using PQC-based key exchange. The data itself is then encrypted with a strong symmetric key derived from this quantum-safe exchange. Even if an adversary captures this encrypted traffic, a future quantum computer would find it computationally infeasible to break the PQC key.
- Secure Firmware Updates: Over-the-air firmware updates for the cranes and AGVs are digitally signed using PQC algorithms. This ensures that only legitimate, untampered updates can be installed, preventing a quantum-enabled attacker from injecting malicious code.
- Identity & Access Management: Every device and user is authenticated using credentials secured by PQC. If a maintenance technician logs into a crane's diagnostic panel, their identity is verified with a quantum-resistant digital certificate.
- Immutable Audit Trails: All critical operational logs and security events are signed using PQC digital signatures and stored in a tamper-proof manner, providing an undeniable audit trail for compliance and forensic analysis.
Result:
The Visakhapatnam smart port terminal achieves an unprecedented level of cybersecurity, effectively future-proofing its operations and sensitive data against both current and anticipated quantum computing threats. The risk of operational disruption, cargo theft, or intellectual property compromise due to cyberattacks is drastically reduced. This advanced security posture enhances the port's reputation as a reliable and secure global trade hub, attracting more international business and ensuring India's critical infrastructure remains resilient in the face of evolving digital threats.
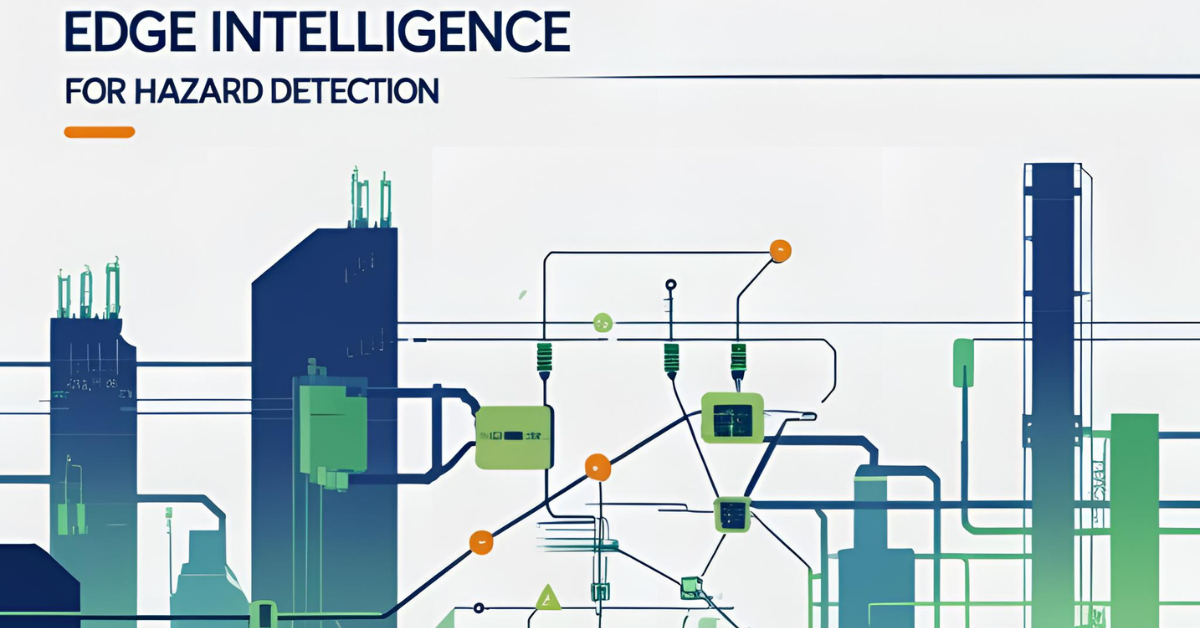
13.Edge Intelligence for Hazard Detection
Application Name: SentinelEdge AI
Overview:
SentinelEdge AI is a cutting-edge solution for Edge Intelligence for Hazard Detection, designed to provide instantaneous, localized threat identification in critical industrial environments. While cloud computing offers vast processing power, the sheer volume of sensor data and the need for sub-millisecond response times for safety-critical events make traditional cloud-centric approaches inadequate. SentinelEdge AI embeds powerful AI models directly onto edge devices (e.g., smart sensors, industrial gateways, local controllers) situated at the source of data generation. This enables it to detect critical hazards like gas leaks, microfractures, unusual vibrations, or overheating in real-time—often within milliseconds—triggering immediate alerts or automated safety responses. It provides a "reflex" capability for the industrial environment, acting as an indispensable first line of defense that the cloud simply cannot match in terms of speed and responsiveness for high-stakes scenarios.
Use Case:
SentinelEdge AI is crucial for industries where immediate detection and response to anomalies are vital for preventing catastrophic failures, ensuring worker safety, and protecting high-value assets. Key use cases include:
- Oil & Gas Refineries & Pipelines:
- Gas Leak Detection: Continuously monitors for minute changes in gas concentrations (e.g., methane, H₂S, VOCs). Edge AI instantly identifies signature patterns of leaks, triggering alarms, automatic valve closures, or ventilation system activation.
- Pipeline Integrity: Acoustic sensors and strain gauges detect microfractures or subtle pressure waves indicative of pipeline integrity issues, enabling immediate shutdown or isolation of affected segments.
- Chemical Manufacturing:
- Exothermic Reaction Control: Monitors temperature and pressure in reactors. Edge AI detects runaway reactions within milliseconds, triggering emergency cooling or inert gas injection before an explosion or rupture.
- Toxic Spill Detection: Vision AI combined with chemical sensors rapidly identifies spills, initiating containment protocols and isolating affected areas.
- Power Generation (Thermal, Hydro, Nuclear):
- Turbine/Generator Overheating & Vibration: High-frequency vibration and thermal sensors feed into edge AI models that detect subtle anomalies indicative of bearing failure, shaft misalignment, or overheating before critical damage occurs. Triggers immediate controlled shutdown or power reduction.
- Transformer Fault Detection: Acoustic and thermal analysis at the edge to detect partial discharges or overheating in high-voltage transformers.
- Mining Operations:
- Ground Stability Monitoring: Geophones and strain gauges detect micro-seismic activity or rock displacement indicative of potential collapses, triggering immediate evacuation alerts.
- Ventilation System Failure: Monitors fan performance and air quality. Edge AI detects failures or dangerous gas buildups, activating backup systems or evacuation alarms instantly.
- High-Precision Manufacturing (e.g., Aerospace, Semiconductors):
- Machine Tool Malfunction: Vibration and acoustic sensors on CNC machines. Edge AI detects tool wear, chatter, or impending component failure in real-time, stopping the machine to prevent damage to expensive parts or the machine itself.
- Quality Anomaly Detection: Vision AI on the production line immediately identifies microscopic defects in components, triggering rejection or stopping the line.
- Industrial Robotics:
- Collision Detection: Proximity sensors and force feedback in robots. Edge AI processes data to detect potential collisions with humans or other robots and triggers an immediate emergency stop.
- Anomalous Robot Behavior: Monitors motor current, joint angles, and unexpected movements. Edge AI detects deviations that could indicate a mechanical fault or software glitch.
Tech Stack:
SentinelEdge AI combines specialized sensors, powerful edge computing, and optimized AI models:
- Specialized Industrial Sensors:
- Gas Detectors: Electrochemical, infrared, catalytic bead, PID sensors for specific gases (CH₄, H₂S, CO, VOCs).
- Vibration Sensors: Accelerometers (MEMS, piezoelectric) for high-frequency data collection.
- Acoustic Sensors: Microphones optimized for specific frequency ranges (e.g., ultrasonic for leaks, infrasound for structural issues).
- Thermal Cameras/Infrared Sensors: For non-contact temperature monitoring and hot spot detection.
- Strain Gauges & Fiber Optics: For structural integrity monitoring (microfractures, stress).
- Vision Cameras (High-Resolution/IR): For visual inspection and anomaly detection.
- Edge Computing Hardware:
- Industrial Edge Gateways: Ruggedized, fanless, powerful mini-PCs (e.g., NVIDIA Jetson series, Intel NUC Industrial, ARM-based industrial controllers) with sufficient processing power (GPUs, NPUs) for AI inference.
- Smart Sensors with Embedded AI: Sensors that have integrated microcontrollers capable of running lightweight AI models directly on the sensor itself (e.g., smart accelerometers performing FFT analysis).
- Real-time Operating Systems (RTOS): Linux variants optimized for low-latency processing (e.g., real-time Linux kernel).
- Connectivity:
- High-Bandwidth, Low-Latency Protocols: Industrial Ethernet (PROFINET, EtherCAT), TSN (Time-Sensitive Networking), 5G private networks, or dedicated short-range wireless for sensor-to-edge communication.
- Robust & Secure: Protocols designed for harsh industrial environments and cybersecurity.
- Edge AI/ML Models:
- Optimized Models: Machine learning models (e.g., Convolutional Neural Networks for vision, Recurrent Neural Networks for time-series data, anomaly detection algorithms like Isolation Forest or One-Class SVM) specifically designed for low-power, low-latency inference at the edge.
- Pre-trained Models: Models trained on vast datasets of normal and abnormal industrial conditions, then fine-tuned for specific assets.
- Model Compression Techniques: Quantization, pruning, knowledge distillation to make models run efficiently on edge hardware.
- Alerting & Actuation System:
- Local Alarms: Audible alarms, visual beacons, haptic feedback on wearables (from integrated safety systems).
- Automated Control Integration: Direct connection to PLCs (Programmable Logic Controllers) or DCS (Distributed Control Systems) for triggering immediate safety responses (e.g., emergency stops, valve closures, ventilation activation).
- Cloud Integration (for long-term storage, training, remote management):
- IoT Platform: AWS IoT Greengrass, Azure IoT Edge, Google Cloud IoT Edge for remote deployment of AI models, device management, and data synchronization.
- Data Lake: For storing aggregated raw sensor data and edge inference results for future model training and root cause analysis.
- MLOps Pipeline: For continuous training, validation, and deployment of updated AI models to edge devices.
- User Interface & Monitoring:
- Local HMI/Control Panel: For immediate local status and basic configuration.
- Central Dashboard: In the control room, providing an overview of all edge-detected hazards, their locations, and status.
Impact/ROI:
SentinelEdge AI delivers critical ROI in high-stakes industrial environments:
- Drastic Reduction in Accidents & Catastrophes: Immediate detection and response to hazards prevent minor issues from escalating into major safety incidents, explosions, or environmental disasters. This is the paramount ROI.
- Minimized Production Downtime: Proactive detection of microfractures, overheating, or tool wear prevents catastrophic equipment failures, allowing for planned maintenance or controlled shutdowns instead of reactive, prolonged outages.
- Significant Cost Savings:
- Reduced Damage to High-Value Assets: Preventing equipment breakdown through early detection saves millions in repair or replacement costs.
- Lower Insurance Premiums: Demonstrating superior safety and risk mitigation capabilities can lead to reduced insurance costs.
- Avoided Regulatory Fines & Legal Penalties: Compliance with safety regulations is enhanced by continuous, verifiable hazard detection.
- Reduced Environmental Cleanup Costs: Early detection of leaks or spills minimizes their environmental impact and associated cleanup expenses.
- Enhanced Worker Safety: Immediate alerts ensure personnel can evacuate hazardous areas or take protective measures, significantly reducing injury risks.
- Improved Operational Efficiency: Maintaining optimal machine health and preventing unplanned stops contributes to smoother production flow.
- Better Data for Root Cause Analysis: High-frequency edge data provides granular insights into the conditions leading up to an incident, aiding in future prevention.
- Increased Regulatory Compliance & Reputation: Proactive hazard management strengthens a company's safety culture and public image.
Real-World Example:
Consider a large, active petrochemical complex in Visakhapatnam, Andhra Pradesh, India, which handles highly volatile chemicals, operates under high pressures and temperatures, and has extensive networks of pipelines and storage tanks. A single unnoticed gas leak or microfracture in a pipe could lead to a massive explosion, fire, or toxic release, with devastating consequences for human life, the environment, and the company's operations.
Before SentinelEdge AI: The complex relied on a combination of periodic manual inspections, fixed gas detectors (that might only detect large leaks after they've dispersed), and SCADA systems that monitored basic pressure/temperature deviations. Detecting a subtle, developing microfracture or a very small gas leak in a complex pipe network was extremely difficult and often discovered only when it had escalated into a significant problem. Response times were limited by network latency to the cloud and manual human interpretation.
With SentinelEdge AI:
- Dense Sensor Deployment with Edge AI: The complex deploys a dense network of specialized sensors throughout its pipelines, reactors, and storage tanks:
- Acoustic Emission Sensors: Attached to critical pipelines and vessels to detect the ultrasonic "pings" of propagating microfractures.
- Hyper-sensitive Gas Detectors: Located at numerous points, optimized to detect minute concentrations of specific volatile organic compounds (VOCs) and H₂S.
- Thermal Cameras: Monitor critical joints and pumps for early signs of overheating.
- Vibration Sensors: On pumps and compressors for machinery health.
- Real-time Edge Inference: Each sensor feeds its high-frequency raw data directly into a local SentinelEdge AI gateway. This gateway has a powerful processor running pre-trained AI models.
- Gas Leak Detection: An edge AI model constantly analyzes the gas sensor data. If it detects a specific, subtle rise in VOC concentration with a particular spectral signature – even before it reaches traditional alarm thresholds – it instantly identifies it as a potential leak (e.g., from a specific valve) within milliseconds.
- Microfracture Detection: Another edge AI model processes acoustic emission data. It differentiates between background noise and the unique sonic signature of a developing microfracture in a pipeline.
- Overheating Anomaly: The edge AI on a thermal camera immediately flags an unexpected hot spot on a bearing that is slightly above normal operating temperature but not yet critical.
- Instantaneous Response:
- Upon detecting a gas leak, the edge gateway doesn't wait for cloud confirmation. It immediately triggers local audible and visual alarms, sends an alert to the nearest operator's handheld device, and automatically initiates a controlled shutdown of the affected pipeline segment by sending a command to the local PLC.
- For a detected microfracture, the system might trigger a slightly less urgent but still critical alert to maintenance, recommending immediate, localized inspection and controlled pressure reduction in that segment.
- For overheating, it might trigger an alert to adjust cooling or schedule immediate inspection.
- Cloud for Analysis & Model Improvement: All edge inferences and a subset of the raw data are sent to the central cloud platform for long-term storage, advanced analytics, and to continuously retrain and improve the edge AI models.
Result:
The petrochemical complex in Visakhapatnam achieves an unprecedented level of safety and operational resilience. The ability to detect gas leaks and microfractures in milliseconds – orders of magnitude faster than traditional methods – drastically reduces the risk of explosions, fires, and toxic releases. This translates to millions of dollars saved in potential disaster recovery, environmental cleanup, and legal liabilities. Unplanned downtime due to equipment failure is significantly reduced by proactive detection, enhancing production continuity. The complex's safety record improves dramatically, bolstering its reputation and ensuring the well-being of its workforce and surrounding communities in Andhra Pradesh.
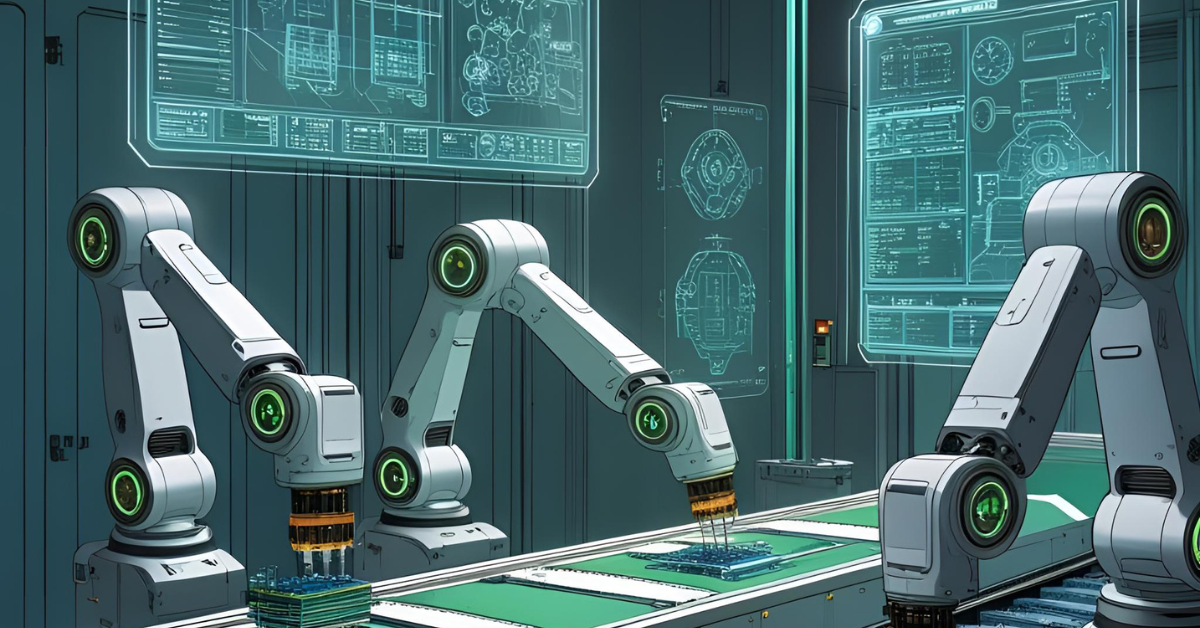
14.Zero-Touch Industrial Onboarding Protocols
Application Name: AutoConnect Pro
Overview:
AutoConnect Pro is an innovative solution for Zero-Touch Industrial Onboarding Protocols, fundamentally transforming how new devices are integrated into complex industrial IoT (IIoT) networks. In the rapidly expanding landscape of Industry 4.0, manually configuring and provisioning thousands of sensors, actuators, robots, and gateways is a time-consuming, error-prone, and security-vulnerable process. AutoConnect Pro automates this entire lifecycle, enabling devices to come online securely and seamlessly without requiring a technician on-site for manual setup. By leveraging technologies like QR codes for simplified initial access and blockchain for immutable device identity and validation, it creates a truly plug-and-play experience. This "no technician, no problem" approach drastically reduces deployment time and costs, enhances security by eliminating human error, and ensures that every new device is a trusted and compliant member of the industrial network from the moment it's powered on.
Use Case:
AutoConnect Pro is essential for industries undergoing large-scale digital transformation, deploying vast numbers of IIoT devices, or operating geographically dispersed facilities where manual intervention is impractical or costly. Key use cases include:
- Large-Scale Smart Factory Deployments (e.g., Automotive, Electronics, FMCG):
- Mass Sensor Rollout: Automatically onboard hundreds or thousands of new temperature, vibration, or quality control sensors on production lines without individual manual configuration.
- New Machine Integration: When a new robotic arm or CNC machine is installed, it can self-onboard to the factory network, receiving its specific configurations and security policies.
- Logistics & Warehouse Automation:
- Automated Guided Vehicle (AGV) / Autonomous Mobile Robot (AMR) Deployment: Quickly add new AGVs or AMRs to the fleet, which self-register, download their operational maps, and integrate into the fleet management system.
- Smart Pallet & Asset Tracking: Rapidly provision RFID readers or environmental sensors for intelligent asset tracking across large warehouses or distribution centers.
- Utilities & Critical Infrastructure (Smart Grids, Water Management):
- Smart Meter Deployment: Streamlines the secure onboarding of thousands of smart energy or water meters in residential, commercial, and industrial areas, ensuring accurate data collection and billing.
- Remote Sensor Networks: Onboard environmental sensors in remote substations, pipelines, or water treatment plants without sending a technician for each device.
- Mining & Construction (Remote Site Monitoring):
- Equipment Monitoring: Rapidly deploy sensors on heavy machinery (excavators, drill rigs) in remote mining sites, automatically connecting them to the central monitoring system for predictive maintenance.
- Site Environmental Monitoring: Onboard air quality or ground stability sensors in hazardous or remote areas.
- Industrial Fleet Management (Shipping, Rail, Aviation):
- Vehicle Telematics & Diagnostics: Automatically register new vehicles or ships with their telematics systems, ensuring they begin transmitting operational data and location information immediately.
Tech Stack:
AutoConnect Pro leverages a sophisticated blend of hardware, software, and networking technologies:
- Device-Side Components:
- Secure Hardware Module (TPM/Secure Element): Embedded in each IIoT device during manufacturing, providing a hardware root of trust, unique device identity (e.g., a hardware-backed cryptographic key pair), and secure storage for initial credentials.
- Factory-Provisioned QR Codes/NFC Tags: Each device comes with a unique, cryptographically linked QR code or NFC tag that contains its unique device ID and a pointer to its onboarding profile.
- Lightweight Onboarding Agent: Firmware pre-loaded on the device enabling it to initiate the onboarding process (e.g., connect to a discovery network, send a provisioning request).
- Network & Connectivity:
- Dedicated Onboarding Network/VLAN: A segmented, secure network that new devices connect to initially for provisioning, isolating them from the main operational network until validated.
- Standard IIoT Protocols: MQTT, CoAP, OPC UA for secure communication once onboarded.
- Central Onboarding & Management Platform:
- Device Management Platform (DMP): A centralized platform responsible for device lifecycle management, including registration, authentication, configuration, and firmware updates (e.g., Azure IoT Hub, AWS IoT Core, Google Cloud IoT).
- Blockchain Network (e.g., Hyperledger Fabric, Ethereum Enterprise):
- Decentralized Identity Registry: Stores immutable records of unique device IDs, their manufacturing details, and their onboarding status.
- Smart Contracts: Automate the validation process. When a device requests onboarding, a smart contract verifies its authenticity against manufacturer records and authorized deployment orders stored on the blockchain.
- Tamper-Proof Audit Trail: Provides an unalterable history of every device's onboarding, configuration changes, and ownership transfers.
- Certificate Authority (PQC-Enabled PKI): Issues digital certificates to newly onboarded devices for ongoing secure authentication and encryption, potentially using post-quantum cryptography for future-proofing.
- Workforce Management/Field App: A mobile application for basic on-site interaction (e.g., scanning a QR code, confirming a successful onboarding, or triggering a re-provision).
- Integration with Enterprise Systems: APIs to connect with MES (Manufacturing Execution Systems), ERP (Enterprise Resource Planning), CMMS (Computerized Maintenance Management Systems), and Identity & Access Management (IAM) systems for role-based access control and data synchronization.
- Security & Policy Enforcement:
- Zero Trust Principles: Every device, even after onboarding, is continuously authenticated and authorized.
- Automated Policy Deployment: Upon successful validation, the system automatically pushes security policies, network configurations, and operational parameters specific to the device's role and location.
Impact/ROI:
AutoConnect Pro delivers significant and measurable ROI through automation, security, and efficiency:
- Drastically Reduced Deployment Time (70-90% faster): Devices can be brought online in minutes instead of hours or days, accelerating project timelines and time-to-value for IIoT initiatives.
- Significant Cost Savings:
- Lower Labor Costs: Eliminates the need for highly skilled technicians for routine device provisioning, freeing them for more complex tasks.
- Reduced Travel Expenses: Minimizes on-site visits for device setup, especially for geographically dispersed deployments.
- Minimized Human Error: Automated processes eliminate misconfigurations, incorrect credential entry, and other manual errors that lead to costly reworks and security vulnerabilities.
- Enhanced Security Posture:
- Stronger Device Identity: Blockchain-validated, immutable device identities prevent unauthorized devices from joining the network.
- Automated Policy Enforcement: Ensures every device is configured with the correct security protocols from day one, reducing attack surfaces.
- Tamper Detection: The blockchain ledger can immediately flag any unauthorized attempts to modify device identities or configurations.
- Improved Scalability: Enables rapid, high-volume deployment of IIoT devices, supporting exponential growth in connected industrial assets.
- Increased Operational Efficiency: Faster deployment means faster data collection, leading to quicker insights for predictive maintenance, process optimization, and quality control.
- Simplified Device Lifecycle Management: From initial onboarding to decommissioning, the blockchain-based registry provides a transparent and verifiable record of each device's journey.
- Empowered Non-Technical Personnel: Enables factory floor operators or even third-party installers with minimal training to deploy new devices, democratizing IIoT adoption.
Real-World Example:
Consider a newly commissioned, state-of-the-art consumer electronics assembly plant in Visakhapatnam, Andhra Pradesh, India. This plant aims for maximum automation, deploying tens of thousands of IIoT sensors (for temperature, humidity, vibration, component tracking), robotic arms, vision cameras, and AGVs across its multiple production lines.
Before AutoConnect Pro: Traditionally, onboarding a new sensor or robot involved a trained IT/OT technician. They would physically connect the device, manually enter network credentials, configure IP addresses, ensure firmware compatibility, install certificates, and register the device with the central management system. For thousands of devices, this would take months, incur massive labor costs, and introduce potential for human error leading to security gaps or operational issues. If a device needed to be replaced, the entire manual process would repeat.
With AutoConnect Pro:
- Pre-Provisioned Devices: Each IIoT device (e.g., a new temperature sensor for a soldering station, a vision camera for quality inspection) arrives at the plant with a unique, tamper-resistant QR code printed on its casing and a pre-loaded secure element containing a cryptographic key pair.
- Zero-Touch Activation:
- An unboxing crew or even the production line operator mounts the new device.
- Using a mobile app (field app) on a ruggedized tablet, they simply scan the QR code on the device.
- The field app sends the device's unique ID (from the QR code) and the location/role information to the central AutoConnect Pro platform.
- The platform, in real-time, queries a private blockchain network (e.g., a Hyperledger Fabric instance). This blockchain contains an immutable record of all approved devices from manufacturers, along with their cryptographic identities. A smart contract on the blockchain verifies if the device's unique ID and cryptographic signature match an authorized record and if it's assigned to this specific plant and location.
- Once validated by the blockchain, the AutoConnect Pro platform automatically:
- Issues a digital certificate to the device (via a secure over-the-air channel), providing it with a trusted identity.
- Pushes the correct network configurations (IP address, Wi-Fi SSID/password, network segment) and security policies (firewall rules, access control lists) to the device.
- Registers the device with the plant's central device management system and MES, assigning its role (e.g., "Soldering Station 5 Temp Sensor," "Assembly Line 2 Vision Camera").
- Updates the blockchain ledger with the device's successful onboarding timestamp and its current operational status.
- No Technician Needed: The device comes online and immediately begins functioning, securely integrated into the plant's network without any manual typing, complex configurations, or a specialized technician on-site for each device. If a device fails and needs replacement, the new device follows the same automated, QR-code-driven process.
Result:
The consumer electronics plant in Visakhapatnam reduces its IIoT device onboarding time by over 80%, saving hundreds of thousands of dollars in labor and accelerating its factory automation rollout. The risk of misconfiguration errors is virtually eliminated, leading to a significant enhancement in cybersecurity and operational reliability. The blockchain validation ensures a tamper-proof chain of custody and identity for every device, providing unparalleled trust and auditability, which is critical for high-value manufacturing and intellectual property protection in Andhra Pradesh.
🚀 Ready to turn your passion for connected tech into real-world impact?
At Huebits, we don’t just teach IoT — we train you to build smart, scalable, and data-driven systems using the tech stacks powering today’s most innovative industries.
From edge devices to cloud platforms, you’ll gain hands-on experience designing end-to-end IoT architectures that collect, analyze, and respond in real time — built for deployment in cities, farms, factories, and homes.
🧠 Whether you're a student, aspiring IoT engineer, or future smart systems architect, our Industry-Ready IoT Program is your launchpad.
Master Python, Embedded C, MQTT, REST APIs, ESP32, Raspberry Pi, AWS IoT, Azure IoT Hub, and Grafana — all by building real-world IoT solutions that deliver results, not just data.
🎓 Next Cohort Starts Soon!
🔗 Join now and claim your seat in the IoT revolution powering tomorrow’s ₹1 trillion+ connected economy.
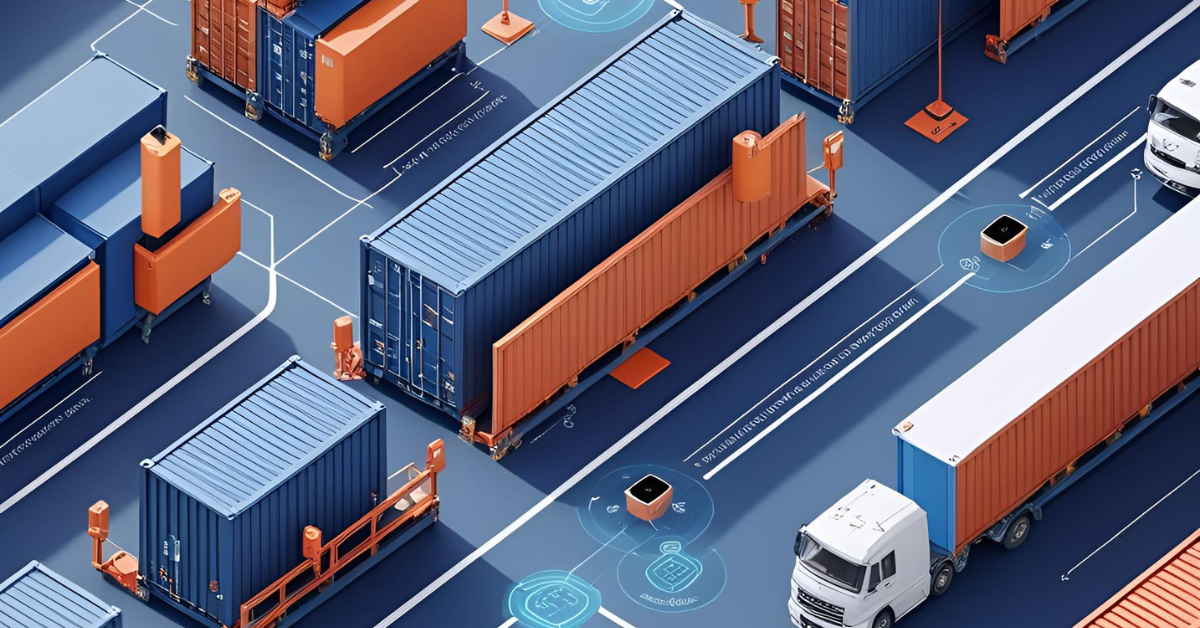
15.Cognitive Supply Chain Sensors
Application Name: SynapseChain
Overview:
SynapseChain represents the next evolution in supply chain management, moving beyond mere visibility to true Cognitive Supply Chain Sensors. It transforms static, reactive logistics into an intelligent, self-learning ecosystem. By embedding advanced IoT sensors with localized processing capabilities (edge AI) throughout the supply chain (on products, pallets, containers, vehicles, and in warehouses), SynapseChain gathers an unprecedented volume of real-time data. This data is then fed into a powerful cognitive engine that leverages AI and machine learning to predict delays before they occur, dynamically suggest optimal route optimizations, detect anomalies indicative of fraud or tampering, and provide deep, actionable insights into every aspect of the logistics flow. No longer a "black-box" operation, SynapseChain provides unparalleled transparency and intelligence, enabling supply chains to "think" and adapt proactively to disruptions and opportunities.
Use Case:
SynapseChain is critical for any industry dealing with complex, global supply chains, high-value goods, perishable items, or strict regulatory compliance, where transparency, efficiency, and risk mitigation are paramount. Key use cases include:
- Pharmaceutical & Cold Chain Logistics:
- Temperature Excursion Prediction: Sensors on vaccine shipments not only monitor temperature but also predict the likelihood of an excursion based on current conditions, upcoming weather, and traffic. AI suggests proactive re-routing or re-icing to prevent spoilage.
- Tamper Detection: Accelerometers and light sensors detect unauthorized package openings or excessive shock, instantly alerting to potential fraud or damage to sensitive medications.
- High-Value Electronics & Luxury Goods:
- Diversion/Theft Detection: GPS and geofencing combined with anomaly detection algorithms identify unusual stops or deviations from planned routes, signaling potential theft or diversion of high-value cargo.
- Counterfeit Prevention: Real-time tracking and immutable digital records (blockchain-linked) confirm the authenticity of goods at every touchpoint, combating counterfeiting.
- Food & Beverage (Perishables):
- Shelf-Life Optimization: Monitors temperature, humidity, and even gas composition (for fruits/vegetables) to predict remaining shelf life, allowing dynamic re-routing to closer markets or faster delivery to minimize waste.
- Quality Degradation Alerts: Detects conditions that could compromise food safety or quality, enabling interventions before products become unsaleable.
- Automotive & Industrial Manufacturing (Just-in-Time/Sequence):
- Component Delivery Delay Prediction: Tracks critical components from suppliers. AI analyzes traffic, weather, customs data, and supplier performance history to predict delivery delays and automatically triggers alerts for production line adjustments or alternative sourcing.
- In-Transit Damage Prevention: Shock sensors on specialized parts detect excessive impacts, alerting the recipient to potential damage before unloading.
- Global Freight & Shipping:
- Port Congestion Prediction: Integrates real-time sensor data from vessels and containers with port schedules, weather forecasts, and historical congestion data to predict delays at ports, allowing carriers to re-route or adjust schedules proactively.
- Optimized Multi-Modal Routing: Dynamically suggests the most efficient routes combining road, rail, sea, and air based on real-time conditions, cost, speed requirements, and carbon footprint objectives.
Tech Stack:
SynapseChain is built on a comprehensive, integrated technology stack:
- Advanced IoT Sensors:
- Multi-Modal Sensors: Temperature, humidity, light, pressure, vibration/shock, GPS, accelerometer, gyroscope, potentially even gas sensors for specific cargo types.
- Low-Power Connectivity: LoRaWAN, NB-IoT, Cat-M1 for long-range, low-power tracking; Bluetooth Low Energy (BLE) for local asset tracking; satellite connectivity for remote areas.
- Embedded Processing: Edge microcontrollers with sufficient processing power for basic data filtering and pre-processing, potentially running lightweight AI models for immediate anomaly detection.
- Edge Computing:
- Smart Gateways/Hubs: Deployed at key transit points (warehouses, distribution centers, in trucks/vessels) to aggregate data from local sensors, perform real-time analytics, and make immediate decisions (e.g., local re-routing, triggering alerts).
- Local AI Inference: Run pre-trained machine learning models at the edge for rapid pattern recognition (e.g., detecting unusual vibration signatures for potential equipment failure, or sudden changes in temperature profiles indicating a cold chain breach).
- Cloud Platform & Big Data Analytics:
- IoT Platform: AWS IoT Core, Azure IoT Hub, Google Cloud IoT for secure ingestion, management, and scaling of massive volumes of sensor data.
- Data Lake/Warehouse: For storing historical sensor data, external market data (weather, traffic, geopolitical events, news feeds), supplier performance data, and customer order history.
- Big Data Processing: Apache Kafka, Spark for real-time stream processing and batch analytics.
- Artificial Intelligence & Machine Learning Core:
- Predictive Analytics:
- Time Series Forecasting: Models (e.g., LSTMs, ARIMA, Prophet) to predict delivery times, demand fluctuations, and potential equipment failures.
- Risk Prediction: ML models trained on historical delays, weather patterns, geopolitical events, and supplier performance to forecast disruption likelihood.
- Prescriptive Analytics/Optimization:
- Route Optimization Algorithms: Graph theory, genetic algorithms, reinforcement learning for dynamic re-routing based on real-time traffic, weather, and unexpected events.
- Inventory Optimization: Models that suggest optimal stock levels based on predicted demand and supply chain conditions.
- Anomaly Detection: Unsupervised learning algorithms (e.g., Isolation Forest, Autoencoders) to identify unusual patterns indicative of fraud, tampering, or operational issues.
- Natural Language Processing (NLP): To integrate and analyze unstructured data from news, social media, and incident reports for broader risk assessment.
- Predictive Analytics:
- Blockchain (Distributed Ledger Technology):
- Immutable Traceability: Records provenance and chain of custody for goods, ensuring transparency and preventing fraud. Each significant event (handover, temperature excursion, inspection) is logged on the blockchain.
- Smart Contracts: Automate actions based on pre-defined conditions (e.g., releasing payment upon verified delivery, triggering an alert if cold chain parameters are violated).
- Secure Data Sharing: Enables trusted, permissioned sharing of supply chain data among multiple stakeholders without a central intermediary.
- Integration Layer:
- APIs: For seamless integration with existing ERP (Enterprise Resource Planning), WMS (Warehouse Management Systems), TMS (Transportation Management Systems), MES (Manufacturing Execution Systems), and CRM (Customer Relationship Management) systems.
- EDI (Electronic Data Interchange): For B2B data exchange with partners.
- User Interface & Visualization:
- Real-time Dashboard: Intuitive dashboards with maps, alerts, KPIs, and predictive insights.
- Digital Twin: A virtual replica of the entire supply chain, visualizing product flow, asset locations, and predicted disruptions.
- Alerting System: Proactive notifications via SMS, email, or app for critical events or predicted issues.
Impact/ROI:
SynapseChain delivers transformative ROI across the entire supply chain:
- Reduced Operational Costs (10-25%):
- Optimized Routes: Lower fuel consumption, reduced mileage, and improved delivery efficiency.
- Minimized Spoilage/Damage: Proactive intervention prevents loss of perishable goods or high-value items.
- Lower Inventory Carrying Costs: More accurate forecasting and real-time visibility reduce the need for buffer stock.
- Improved On-Time Delivery Performance (15-30% improvement): Predicting and mitigating delays ensures goods arrive when expected, enhancing customer satisfaction and reducing penalties.
- Enhanced Fraud Detection & Loss Prevention (Significant Savings): Real-time anomaly detection and immutable traceability reduce theft, diversion, and counterfeiting losses.
- Increased Agility & Resilience: The ability to sense, predict, and adapt to disruptions makes the supply chain more robust against unexpected events (weather, geopolitical, supplier issues).
- Better Customer Satisfaction & Brand Reputation: Reliable deliveries, transparency, and product integrity lead to higher customer loyalty.
- Faster Decision-Making: Actionable insights from cognitive sensors enable supply chain managers to make informed decisions in real-time.
- Reduced Manual Intervention & Errors: Automation of tracking, alerting, and some optimization tasks frees up staff for more strategic work.
- Improved Compliance & Auditability: Immutable records on blockchain provide irrefutable proof of conditions and actions throughout the supply chain.
- Lower Carbon Footprint: Optimized routes and reduced waste contribute to sustainability goals.
Real-World Example:
Consider a major seafood exporter based in Visakhapatnam, Andhra Pradesh, India, specializing in fresh prawns and fish, shipping them globally (e.g., to markets in Japan, Europe, and the US). The quality and safety of these products are highly dependent on maintaining a strict cold chain, and any deviation can lead to spoilage, huge financial losses, and damage to their international reputation. Fraudulent practices, such as mislabeling origin or species, also pose a significant threat.
Before SynapseChain: The exporter relied on manual temperature checks, basic GPS tracking, and paper-based logs. They would only know about a cold chain breach or a significant delay after it had occurred, often upon arrival at the destination when the cargo was already compromised. Detecting fraud, such as product substitution or origin misrepresentation, was nearly impossible mid-transit. Route planning was static and didn't account for real-time variables.
With SynapseChain:
- Smart Containerization: Each container of seafood is equipped with SynapseChain cognitive sensors that include:
- Multi-Point Temperature & Humidity Sensors: Providing granular data from different areas within the container.
- GPS/GSM/Satellite Trackers: For global location tracking.
- Light & Accelerometers: To detect unauthorized opening or excessive shock.
- IoT Gateway: In the container to aggregate sensor data and perform edge processing.
- Real-time Data & Edge Intelligence: As the container moves from the processing plant in Visakhapatnam to the port, onto the vessel, and then through international logistics networks:
- Edge AI for Anomaly Detection: The gateway on the container continuously monitors temperature profiles. If the temperature deviates by even a small margin from the optimal range, or if the rate of temperature change is unusual (e.g., indicative of a faulty refrigeration unit), the edge AI immediately flags it as a potential cold chain breach. Similarly, unusual light exposure or excessive vibrations trigger "tampering" or "damage" alerts.
- Predictive Delay & Route Optimization: The cognitive engine in the cloud constantly ingests this real-time sensor data, combined with external data feeds:
- Weather Data: Predicting storms at sea or extreme temperatures in transit countries.
- Traffic Data: Real-time road conditions from Visakhapatnam to Chennai port.
- Port Congestion Data: Historical and real-time data on queues at customs or vessel berths.
- Geopolitical Updates: Information on strikes or trade route disruptions.
- Based on this, the AI predicts potential delays (e.g., "Vessel expected to be 12 hours late at Singapore port due to typhoon") and suggests alternative routes (e.g., "Consider diverting to Colombo port and trans-shipping via a faster vessel") or proactive actions (e.g., "Add more dry ice to container 123 for extended transit").
- Fraud Detection & Provenance:
- Every major event (loading, customs clearance, hand-over to new carrier, temperature alerts) is recorded on a permissioned blockchain ledger. Each record is linked to the unique digital identity of the container and its contents.
- If a sensor reports an unexpected location deviation, or if a container is opened prematurely, the system flags it.
- At destination, a quick scan of a QR code linked to the blockchain instantly verifies the product's origin, cold chain history, and authenticity, preventing mislabeled or compromised seafood from entering the market.
Result:
The Visakhapatnam seafood exporter experiences a 90% reduction in spoilage and quality-related rejections, leading to substantial cost savings and safeguarding their premium brand image. On-time delivery performance improves by 20% as the company proactively mitigates delays. The immutable, transparent traceability provided by blockchain-linked sensors virtually eliminates fraud and ensures full compliance with international food safety regulations. This cognitive capability transforms their supply chain from a reactive cost center into a transparent, resilient, and highly efficient profit driver in the global seafood market.
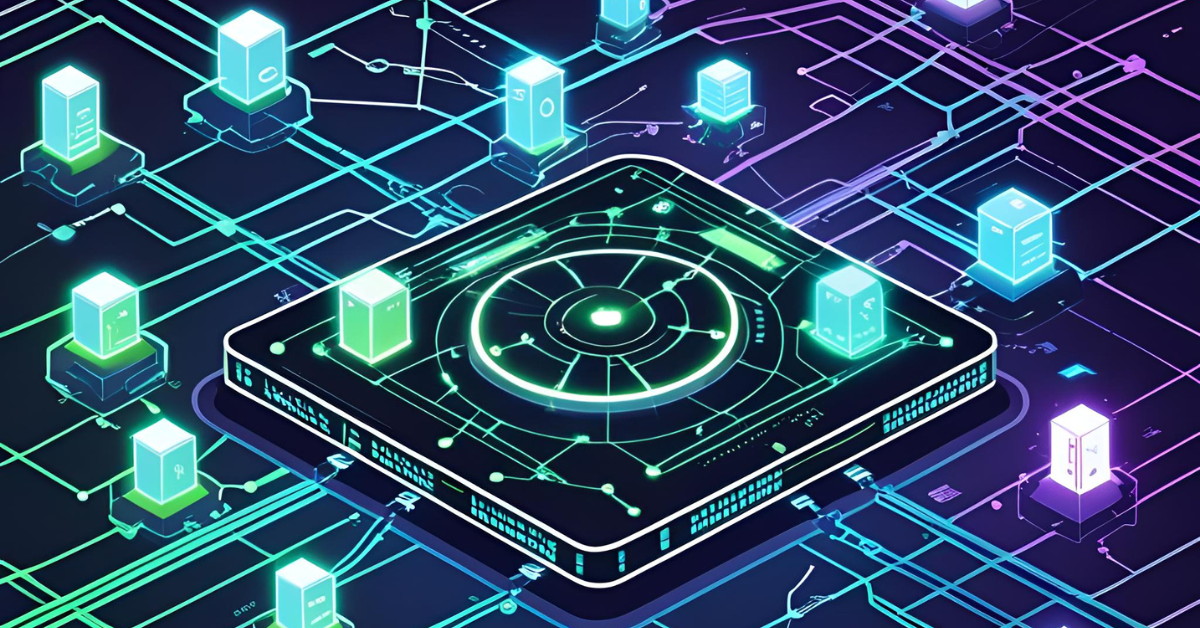
16.Cyber-Physical Intrusion Prevention Systems
Application Name: SentinelX Industrial Guard
Overview:
SentinelX Industrial Guard is a next-generation Cyber-Physical Intrusion Prevention System (CP-IPS) that extends IIoT security far beyond traditional IT firewalls and endpoint protection. Recognizing that modern industrial environments are deeply intertwined cyber and physical systems, SentinelX focuses on real-time anomaly detection directly on operational technology (OT) assets such as conveyor belts, security cameras, robotic arms, and SCADA systems. By continuously analyzing their behavior – including operational parameters, network traffic, sensor data, and physical movements – SentinelX identifies subtle deviations and patterns indicative of cyber intrusions, physical tampering, insider threats, or even equipment malfunctions. This proactive, holistic approach provides an early warning system and automated response capabilities, preventing cyberattacks from manifesting as physical disruptions, ensuring the safety, reliability, and integrity of industrial operations in a way that traditional security measures alone cannot achieve.
Use Case:
SentinelX Industrial Guard is crucial for industries with critical infrastructure, sensitive processes, high-value assets, and strict safety or regulatory compliance requirements. Key use cases include:
- Manufacturing & Industrial Control Systems (ICS):
- SCADA/PLC Anomaly Detection: Monitors network traffic and command sequences to PLCs, RTUs, and HMIs for unauthorized access, manipulated commands, or denial-of-service attempts. Also analyzes process variables (e.g., unexpected temperature or pressure changes) that could indicate a cyber-physical attack.
- Robotics & Automation Security: Detects unusual robot movements, deviations from programmed paths, or unauthorized access to robot controllers that could lead to product defects, collisions, or sabotage.
- Conveyor Belt & Material Handling System Monitoring: Analyzes motor current, speed, and sensor readings for anomalies that might indicate physical tampering (e.g., intentional blockage) triggered by a cyber intrusion.
- Energy & Utilities (Power Grids, Water Treatment, Oil & Gas):
- Substation Security: Analyzes data from smart meters, protective relays, and control systems for malicious commands or unauthorized configuration changes. Integrates with physical security systems (cameras, access control) to correlate cyber and physical events.
- Pipeline Monitoring: Detects unusual pressure fluctuations or valve operations that could be caused by cyberattacks targeting control systems, potentially leading to leaks or disruptions. Correlates with physical intrusion sensor data along pipelines.
- Transportation (Ports, Airports, Railways):
- Automated Systems Security: Monitors control systems for automated cranes, baggage handling systems, or railway signaling for malicious manipulation that could cause disruptions or safety incidents. Correlates with video surveillance for physical breaches.
- Access Control & Surveillance Integration: Analyzes data from access control systems (card readers, biometric scanners) and security cameras for suspicious patterns (e.g., unauthorized access attempts followed by unusual OT activity).
- Healthcare (Medical Device Security, Hospital Infrastructure):
- Connected Medical Device Monitoring: Detects anomalies in the behavior of networked medical devices (e.g., infusion pumps, patient monitors) that could indicate compromise.
- Building Management Systems (BMS) Security: Monitors HVAC, lighting, and access control systems for unusual activity that could be a precursor to a physical security breach or disrupt critical hospital operations.
Tech Stack:
SentinelX Industrial Guard combines specialized sensors, advanced analytics, and robust security measures:
- OT Network Monitoring & Visibility:
- Deep Packet Inspection (DPI) for Industrial Protocols: Analyzes network traffic for protocols like Modbus, PROFINET, EtherCAT, DNP3, identifying anomalies in command sequences and data payloads.
- Asset Inventory & Baselining: Automatically discovers and profiles all OT assets on the network, establishing a baseline of normal operational behavior.
- Network Segmentation Monitoring: Verifies the integrity of network segmentation and detects unauthorized communication across segments.
- Physical Sensor Integration & Analytics:
- Conveyor Belt Sensors: Analyzes data from speed sensors, motor current sensors, load cells, and proximity sensors for unusual patterns (e.g., sudden stops, overloads at unexpected times).
- Security Camera Analytics: Leverages AI-powered video analytics (object detection, motion detection, behavior recognition) to identify unusual physical activity around critical OT assets, unauthorized access, or tampering.
- Environmental Sensors: Monitors temperature, humidity, and other environmental factors for deviations that might correlate with cyber incidents or physical threats.
- Acoustic & Vibration Sensors: Detects unusual sounds or vibrations from machinery that could indicate physical tampering or cyber-induced malfunctions.
- Edge Intelligence & Real-Time Anomaly Detection:
- Behavioral Anomaly Detection Engines: Machine learning algorithms (e.g., statistical models, time-series analysis, neural networks) running on edge devices or local servers to analyze OT data in real time and identify deviations from established baselines.
- Rule-Based Detection: Predefined rules based on known attack patterns and industrial control system vulnerabilities.
- Correlation Engines: Combines insights from network traffic analysis, physical sensor data, and security logs to identify complex, multi-stage attacks that span cyber and physical domains.
- Threat Intelligence & Contextual Enrichment:
- OT-Specific Threat Intelligence Feeds: Provides up-to-date information on known ICS vulnerabilities, attack signatures, and threat actors targeting industrial environments.
- Contextual Data Integration: Correlates anomalies with information about asset criticality, process dependencies, and potential impact.
- Automated Response & Mitigation:
- Policy-Based Responses: Predefined actions (e.g., isolating a compromised device, alerting security personnel, triggering a safe shutdown sequence) that are automatically executed based on detected anomalies and configured policies.
- Integration with Security Orchestration, Automation, and Response (SOAR) Platforms: Enables more complex, coordinated responses across IT and OT security tools.
- Centralized Monitoring & Management:
- Security Operations Center (SOC) Dashboard: Provides a unified view of OT security events, alerts, and the overall cyber-physical security posture.
- Incident Response Workflows: Guides security teams through investigation and remediation procedures for cyber-physical incidents.
Impact/ROI:
SentinelX Industrial Guard delivers critical ROI by protecting against a wider range of threats and minimizing potential damages:
- Enhanced Cyber-Physical Security Posture: Provides a holistic defense against attacks that target the interconnected nature of cyber and physical industrial systems, significantly reducing the attack surface.
- Prevention of Production Downtime & Financial Losses: Early detection and prevention of cyber-physical intrusions avoid costly disruptions to operations, equipment damage, and loss of productivity.
- Improved Safety & Reduced Risk of Accidents: By detecting malicious manipulation of control systems or physical tampering, SentinelX helps prevent safety incidents, environmental damage, and potential harm to personnel.
- Enhanced Regulatory Compliance: Assists organizations in meeting stringent security requirements and industry standards for critical infrastructure and industrial control systems.
- Faster Incident Detection & Response: Real-time anomaly detection and automated responses significantly reduce the time to identify and contain cyber-physical incidents, minimizing their impact.
- Increased Visibility into OT Operations: Provides a deeper understanding of OT network traffic and device behavior, improving overall situational awareness.
- Reduced Risk of Intellectual Property Theft & Sabotage: Protects valuable data, control algorithms, and manufacturing processes from malicious actors.
- Improved Asset Reliability & Lifespan: By detecting anomalies that could indicate equipment malfunction (whether cyber-induced or otherwise), SentinelX can contribute to proactive maintenance and prevent catastrophic failures.
Real-World Example:
Consider a large petrochemical processing plant in Visakhapatnam, Andhra Pradesh, India, which relies heavily on a complex network of sensors, actuators, PLCs, and SCADA systems to control critical processes involving hazardous materials under high pressure and temperature. A cyberattack that manipulates sensor readings or control commands could have catastrophic consequences, leading to explosions, leaks, and significant environmental damage and loss of life.
Before SentinelX Industrial Guard: The plant primarily relied on traditional IT firewalls at the perimeter and basic antivirus software on operator workstations. There was limited real-time visibility into the OT network traffic and no automated way to detect subtle anomalies in the behavior of critical control system components or physical assets. Security cameras provided surveillance but lacked intelligent analytics to correlate physical events with cyber activity.
With SentinelX Industrial Guard:
- OT Network Monitoring: SentinelX is deployed to passively monitor all network traffic on the plant's OT network, performing deep packet inspection of protocols like Modbus and analyzing command sequences between HMIs and PLCs. It establishes a baseline of normal communication patterns for each device.
- Physical Sensor Integration: The system ingests real-time data from various physical sensors:
- Pressure and Temperature Sensors: Monitoring critical vessels and pipelines.
- Valve Position Sensors: Tracking the state of safety valves and control valves.
- Motor Current Sensors: On pumps and compressors.
- Security Cameras: Covering critical areas around control rooms, pipelines, and storage tanks.
- Real-Time Anomaly Detection:
- Cyber Anomaly: SentinelX detects an unauthorized command originating from an engineering workstation (that was recently compromised via a phishing attack) attempting to open a critical safety valve beyond its normal operating range during an off-shift hour. This deviation from the established baseline triggers an immediate high-severity alert.
- Physical Anomaly Correlation: Simultaneously, a security camera near the affected valve detects unusual, unscheduled maintenance activity by an individual who badges in with a compromised access card minutes before the unauthorized valve command. SentinelX's correlation engine links these two seemingly separate events – the cyber command and the suspicious physical presence – significantly raising the confidence level of a malicious intrusion.
- Physical Tampering Detection: On a remote section of a pipeline, SentinelX analyzes the data from acoustic sensors and detects subtle, high-frequency vibrations that deviate from the normal operational noise profile. While not immediately critical, this anomaly, combined with a slight unexplained pressure drop reported by a nearby sensor, flags a potential physical tampering attempt or a precursor to a cyber-physical attack targeting pipeline integrity.
- Automated Response: Based on pre-configured policies, the detection of the unauthorized valve command and correlated physical activity automatically triggers:
- Isolation of the compromised workstation from the OT network.
- An alert to the plant's security operations center (SOC) and the on-call incident response team.
- A temporary lockout of the affected user's access credentials.
- A verification of the valve's physical state by a local technician dispatched based on the camera feed and location data.
Result:
SentinelX Industrial Guard provides the petrochemical plant in Visakhapatnam with a significantly enhanced cyber-physical security posture. The ability to detect subtle anomalies in both the cyber and physical domains, and to correlate these events in real time, allows for the prevention of potentially catastrophic incidents before they can manifest. This proactive approach minimizes the risk of explosions, environmental damage, and production downtime, safeguarding human life, the environment, and the company's assets and reputation in Andhra Pradesh. The increased visibility into OT operations also improves overall security awareness and enables more effective long-term risk management.
🚀 Ready to turn your passion for connected tech into real-world impact?
At Huebits, we don’t just teach IoT — we train you to build smart, scalable, and data-driven systems using the tech stacks powering today’s most innovative industries.
From edge devices to cloud platforms, you’ll gain hands-on experience designing end-to-end IoT architectures that collect, analyze, and respond in real time — built for deployment in cities, farms, factories, and homes.
🧠 Whether you're a student, aspiring IoT engineer, or future smart systems architect, our Industry-Ready IoT Program is your launchpad.
Master Python, Embedded C, MQTT, REST APIs, ESP32, Raspberry Pi, AWS IoT, Azure IoT Hub, and Grafana — all by building real-world IoT solutions that deliver results, not just data.
🎓 Next Cohort Starts Soon!
🔗 Join now and claim your seat in the IoT revolution powering tomorrow’s ₹1 trillion+ connected economy.
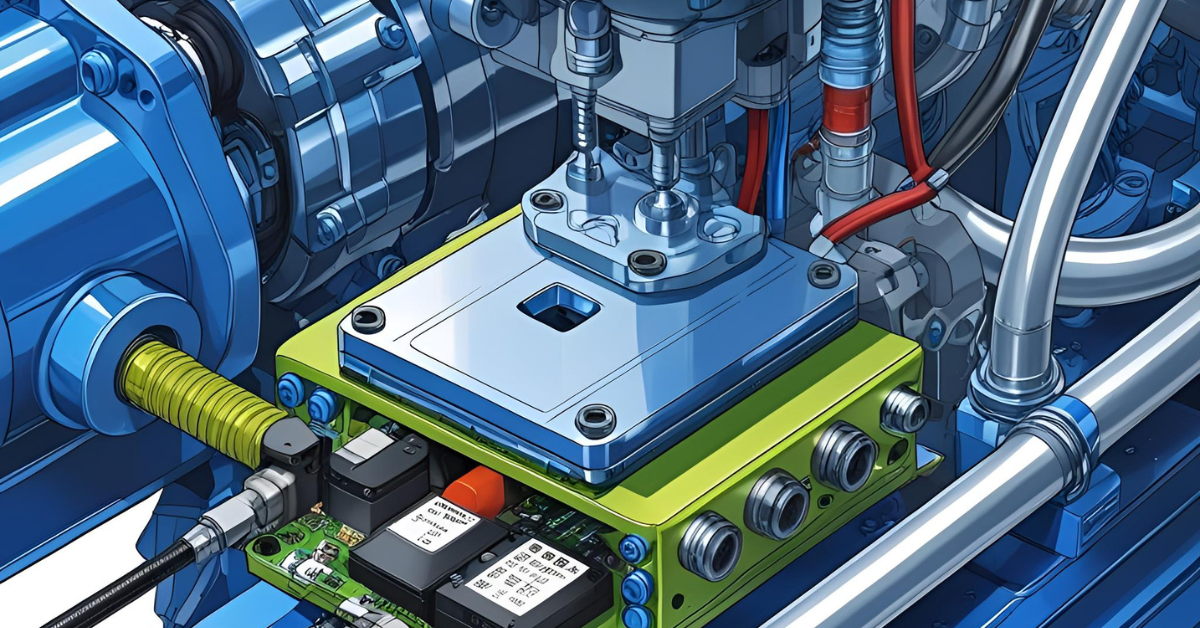
17.Smart Lubrication Systems for Heavy Machinery
Application Name: LubeSense AI
Overview:
LubeSense AI revolutionizes heavy machinery maintenance through Smart Lubrication Systems. Moving beyond traditional scheduled or reactive lubrication, LubeSense AI employs advanced microfluidic and tribological sensors directly embedded within critical machinery components. These intelligent sensors continuously monitor lubricant conditions (viscosity, contamination, degradation) and detect friction and wear in real-time at a microscopic level. When an optimal lubrication need is identified—whether due to increased friction, changing load conditions, or lubricant degradation—LubeSense AI triggers precision auto-lubrication, delivering the exact type and amount of lubricant precisely when and where it's needed. This data-driven, closed-loop system extends machine lifespan, dramatically reduces unplanned downtime, minimizes lubricant consumption, and transforms maintenance from a generalized schedule into a highly precise, demand-driven process.
Use Case:
LubeSense AI is indispensable for industries relying on heavy, continuously operating, and high-value machinery where lubrication is critical for performance and longevity, and where downtime is extremely costly. Key use cases include:
- Mining Operations (Excavators, Haul Trucks, Conveyors):
- Draglines & Shovels: Monitors massive gears, bearings, and pivot points. LubeSense AI ensures optimal lubrication under extreme loads and dusty conditions, preventing catastrophic failures of critical components.
- Haul Truck Wheel Hubs & Bearings: Detects increased friction due to heavy loads or rough terrain, triggering precise lubrication to prevent premature wear and wheel detachment.
- Crushers & Conveyor Systems: Ensures continuous lubrication of bearings and rollers operating in abrasive environments, extending component life and preventing jams.
- Steel Manufacturing (Rolling Mills, Continuous Casters):
- Roll Stands & Bearings: Monitors the massive bearings in hot and cold rolling mills. LubeSense AI detects subtle changes in friction caused by high temperatures or immense pressure, triggering immediate precision lubrication to prevent seizing and ensure consistent product quality.
- Continuous Casters: Ensures precise lubrication of molds and rollers in extreme heat conditions to prevent material sticking and maintain casting integrity.
- Ports & Heavy Lifting Equipment (Cranes, Spreaders):
- Port Container Cranes (Gantry, Ship-to-Shore): Monitors large gears, wire ropes, and slew bearings in continuous operation. LubeSense AI ensures critical lubrication for components under constant heavy load and corrosive marine environments.
- Spreader Mechanisms: Ensures lubrication of complex moving parts that interact directly with containers, preventing friction and wear during rapid loading/unloading.
- Power Generation (Turbines, Generators, Coal Mills):
- Turbine Bearings: Monitors lubrication film thickness and contamination for critical turbine bearings, adjusting lubricant flow to maintain optimal conditions and prevent catastrophic bearing failure.
- Coal Mill Gearboxes: Ensures robust lubrication in high-vibration, dusty environments.
- Construction (Heavy Earthmoving Equipment):
- Excavator Booms & Buckets: Monitors pins, bushings, and hydraulic cylinders. LubeSense AI provides demand-driven lubrication for moving parts under extreme, dirty, and variable load conditions.
Tech Stack:
LubeSense AI integrates advanced sensing, fluidics, and AI:
- Microfluidic & Tribological Sensors:
- Friction & Wear Sensors: Piezoelectric sensors, acoustic emission sensors, or specialized MEMS (Micro-Electro-Mechanical Systems) sensors embedded near contact points (bearings, gears) to detect minute changes in friction coefficient, material wear particles, or acoustic signatures of impending wear.
- Oil Quality Sensors: Microfluidic sensors that analyze lubricant properties (viscosity, dielectric constant for contamination, particle counts, oxidation levels) in real-time.
- Temperature & Pressure Sensors: Integrated for contextual data on operating conditions.
- Precision Auto-Lubrication System:
- Smart Lubricant Dispensers: Electronically controlled pumps and nozzles that can deliver precise micro-doses of lubricant to specific points.
- Multi-Point Lubrication Systems: Configurable systems capable of delivering different types of lubricants to various points on a single machine.
- Reservoir & Filtration Monitoring: Sensors to monitor lubricant levels and filter status.
- Edge Computing & Local Intelligence:
- Industrial Edge Controllers/Gateways: Process high-frequency data from the microfluidic and tribological sensors in real-time.
- Edge AI Models: Run lightweight machine learning models (e.g., neural networks trained on friction/wear patterns, anomaly detection algorithms) directly on the edge to make instantaneous decisions on lubrication needs (e.g., "increase flow by X amount," "apply Y type of grease to Z point"). This "reflex" action is critical.
- Closed-Loop Control: Direct communication between the edge controller and the precision lubrication system for immediate actuation without cloud latency.
- IIoT Connectivity:
- Industrial Wireless: LoRaWAN (for lower data rate sensors over large areas), Wi-Fi 6, 5G private networks (for high-bandwidth sensor data and critical control), or wired industrial Ethernet (Modbus TCP, PROFINET) for reliable data transmission to edge gateways and then to the cloud.
- Cloud Platform & Advanced Analytics:
- IoT Platform: AWS IoT Core, Azure IoT Hub, Google Cloud IoT for secure ingestion and management of aggregated lubrication data, machine health, and operational parameters.
- Time-Series Databases: For efficient storage and analysis of high-frequency sensor data.
- Machine Learning Models (Cloud-based): For long-term trend analysis, predictive modeling of component lifespan based on lubrication data, and optimization of lubricant types/schedules across an entire fleet.
- Digital Twin Integration: The lubrication data feeds into a broader digital twin of the heavy machinery, providing a comprehensive view of its health and performance.
- User Interface & Management:
- Maintenance Dashboard: Visualizes real-time lubricant conditions, friction levels, remaining useful life (RUL) of components, and active lubrication events.
- Alerting System: Notifications to maintenance teams for critical issues (e.g., sudden excessive wear, lubricant contamination) or for human intervention when necessary.
- Integration: APIs to connect with CMMS (Computerized Maintenance Management Systems), ERP (Enterprise Resource Planning), and EAM (Enterprise Asset Management) systems for automated work order generation and inventory management of lubricants.
Impact/ROI:
LubeSense AI delivers significant and multi-faceted ROI for heavy machinery operators:
- Dramatic Reduction in Unplanned Downtime (20-50%): By preventing catastrophic failures caused by inadequate or excessive lubrication, the primary cause of many machine breakdowns. This is the single biggest value driver.
- Extended Machinery Lifespan (15-30%): Optimal, demand-driven lubrication reduces wear and tear on critical components like bearings, gears, and shafts, extending the operational life of very expensive heavy machinery.
- Significant Lubricant Consumption Reduction (10-30%): Precision auto-lubrication applies only the necessary amount of lubricant exactly when and where needed, eliminating waste from over-lubrication or unnecessary scheduled applications.
- Lower Maintenance Costs (15-25%):
- Reduced need for reactive repairs and component replacements.
- Fewer labor hours for manual lubrication checks and applications.
- Optimized inventory of spare parts and lubricants.
- Improved Operational Efficiency & Productivity: Machines run more smoothly and reliably, leading to consistent performance and higher throughput.
- Enhanced Safety: Reduces the need for manual lubrication in hazardous areas and prevents machinery breakdowns that could lead to accidents.
- Data-Driven Maintenance Strategy: Provides granular insights into machine health and lubrication needs, enabling a shift from time-based to true condition-based and prescriptive maintenance.
- Environmental Benefits: Reduced lubricant consumption means less waste and better environmental stewardship.
Real-World Example:
Consider a large open-pit iron ore mine in Visakhapatnam, Andhra Pradesh, India. This mine operates enormous excavators (e.g., hydraulic shovels, draglines) and a fleet of massive haul trucks, working continuously under extreme loads, high temperatures, and abrasive, dusty conditions. The pivot points, bearings, and gears of these machines are under immense stress, and proper lubrication is paramount. A single excavator breakdown can halt operations and cost millions per day in lost production.
Before LubeSense AI: The mine relied on scheduled lubrication (e.g., daily greasing) or reactive lubrication (applying grease when a technician noticed excessive noise or wear). This often led to:
- Over-lubrication: Wasting expensive lubricants, creating environmental hazards, and attracting dust.
- Under-lubrication: Leading to premature wear, increased friction, and ultimately catastrophic bearing or gear failures, causing unplanned downtime.
- Manual Labor: Technicians spending significant time manually greasing hundreds of points.
With LubeSense AI:
- Sensor Integration: The mine equips its excavators and haul trucks with LubeSense AI sensors:
- Microfluidic oil quality sensors: Continuously monitor the engine oil and hydraulic fluid for contamination, viscosity degradation, and wear particles.
- Tribological sensors (friction/wear): Embedded in critical bearings (e.g., slew bearings of the excavator, wheel hub bearings of haul trucks) to detect friction changes in real-time.
- Vibration sensors: On gearboxes and motors, providing contextual data.
- Edge Intelligence: Each piece of heavy machinery has an edge controller running LubeSense AI models.
- Real-time Decision: As an excavator performs heavy digging, the edge AI detects a slight increase in friction in the slew bearing due to increased load. Simultaneously, the oil quality sensor shows a subtle rise in metallic particles.
- Precision Actuation: Within milliseconds, the edge AI commands the integrated precision auto-lubrication system to dispense a micro-dose of high-performance grease specifically to that slew bearing. It avoids over-greasing other components.
- Condition-Based Adjustment: For haul trucks, the system adjusts the frequency and amount of lubricant dispensed to wheel hub bearings based on the truck's real-time load, speed, and the dustiness of the terrain it's traversing.
- Cloud for Fleet Optimization: All local lubrication events, sensor data, and machine health reports are aggregated in the cloud. The central AI optimizes lubrication strategies across the entire fleet, predicts long-term component lifespans, and manages lubricant inventory.
Result:
The iron ore mine in Visakhapatnam achieves a 35% reduction in unplanned downtime for its excavators and haul trucks, directly translating to millions of dollars in increased iron ore production. The lifespan of critical components like large bearings is extended by 25%, reducing costly replacements. Lubricant consumption is cut by 20%, leading to significant material cost savings and a reduced environmental footprint. The mine transitions from reactive to truly prescriptive maintenance, ensuring its heavy machinery operates at peak performance with unparalleled reliability in the harsh mining environment of Andhra Pradesh.
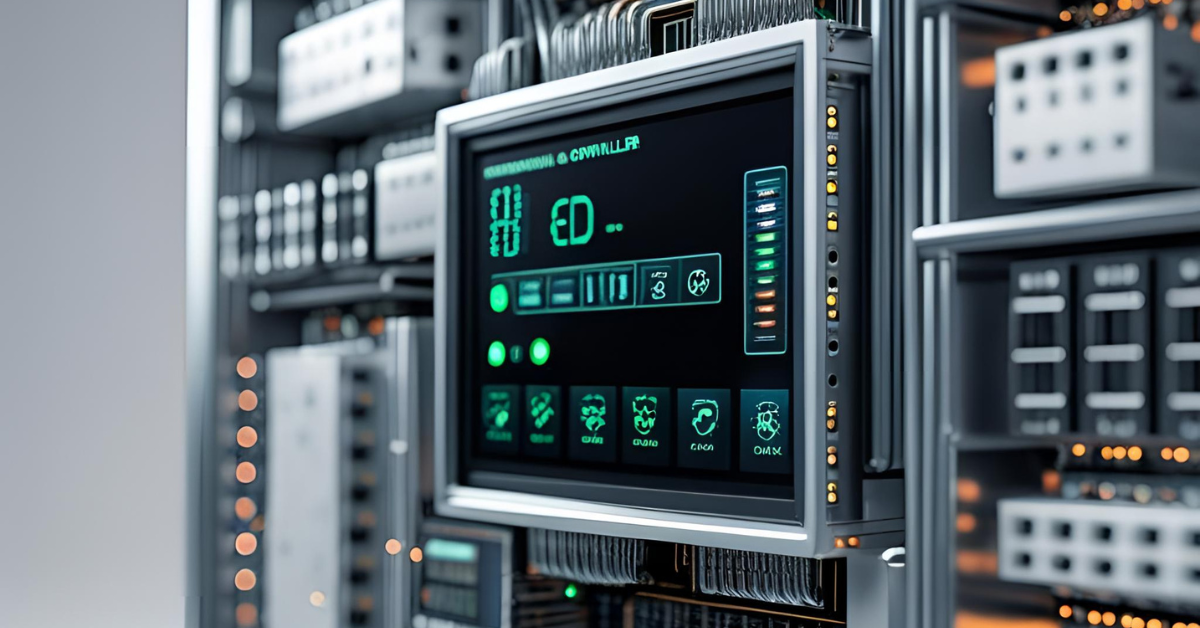
18.Microgrid-Synced Industrial Controllers
Application Name: GridHarmony Industrial
Overview:
GridHarmony Industrial introduces a new paradigm for energy management in industrial settings by implementing Microgrid-Synced Industrial Controllers. This solution goes beyond passive energy monitoring, transforming factories into active participants in their energy supply, particularly when integrated with local microgrids powered by renewable sources like solar and wind. At its core, GridHarmony Industrial comprises a network of IIoT systems deeply integrated with production machinery and facility infrastructure, all orchestrated by intelligent controllers. These controllers continuously monitor the microgrid status (e.g., renewable generation output, battery storage levels, grid connection status, energy pricing signals) in real-time. Leveraging AI and predictive analytics, they auto-balance energy usage within the factory, optimizing operations to match available clean energy, minimize reliance on the main grid during peak pricing, and seamlessly transition during grid outages. This creates a resilient, sustainable, and cost-efficient industrial operation.
Use Case:
GridHarmony Industrial is ideal for large manufacturing plants, data centers, critical infrastructure facilities, or any industrial complex seeking to enhance energy independence, reduce operational costs, and bolster sustainability through integrated renewable energy and microgrid capabilities. Key use cases include:
- Automotive Manufacturing Plants:
- Paint Shops & Welding Lines: These are high-energy consumers. GridHarmony can dynamically adjust non-critical operations (e.g., pre-heating ovens, charging AGVs) to periods of high solar or wind generation from the microgrid or during off-peak grid hours.
- Assembly Line Synchronization: In islanded mode (disconnected from the main grid), it ensures critical assembly line segments remain operational by prioritizing power and potentially shedding non-essential loads based on real-time microgrid capacity.
- Pharmaceutical & Biotech Facilities:
- Lab & Cleanroom HVAC: While critical loads, some HVAC systems or research equipment might have flexibility. GridHarmony can shift certain energy-intensive processes or non-critical lab equipment usage to optimize against microgrid output or grid pricing.
- Seamless Power Transition: Ensures uninterrupted power for sensitive cold storage, fermentation tanks, and critical laboratory instruments during main grid outages by seamlessly switching to microgrid power.
- Steel Mills & Heavy Industry:
- Electric Arc Furnaces (EAFs): While EAFs are immense power draws, GridHarmony can help optimize their operational scheduling to align with periods of high renewable energy availability or lower grid prices, reducing demand charges.
- Motor Control & Pumping Stations: Adjusts the operational cycles of large pumps or conveyors based on microgrid capacity, ensuring essential operations continue reliably.
- Data Centers (Edge & Colocation):
- Server Rack Power Optimization: Dynamically shifts computational workloads or fan speeds based on real-time microgrid energy availability and pricing, minimizing reliance on expensive grid power.
- Uninterrupted Power: Acts as the brain for seamless transfer to battery storage and on-site generation during grid fluctuations or blackouts, ensuring continuous data processing.
- Food Processing Plants:
- Refrigeration & Freezing Units: While essential, GridHarmony can optimize the defrost cycles or pre-cooling of cold storage units to periods of abundant renewable energy.
- Wastewater Treatment Facilities: Synchronizes pump operations and aerators with microgrid status to reduce energy costs and improve resilience.
- Remote Industrial Sites (e.g., Mining, Oil & Gas Fields):
- Full Grid Independence: For sites primarily relying on solar/wind microgrids with battery storage, GridHarmony is essential for managing load, charging/discharging batteries, and dispatching backup generators only when absolutely necessary, minimizing fuel costs and emissions.
Tech Stack:
GridHarmony Industrial relies on a sophisticated integration of energy systems, IIoT, and AI:
- Microgrid Components:
- Distributed Energy Resources (DERs): Solar PV arrays, wind turbines, battery energy storage systems (BESS), small-scale conventional generators (e.g., natural gas, diesel for backup).
- Power Converters & Inverters: Bi-directional inverters for connecting DERs to the microgrid bus, optimizing power flow.
- Switchgear & Circuit Breakers: For seamless connection/disconnection from the main grid and internal load management.
- GridHarmony Controller (Microgrid Management System - MGMS):
- Centralized Control Unit (Edge/On-Premise): A ruggedized industrial computer or dedicated controller (e.g., from Schneider Electric, Siemens, ABB, SEL) acting as the brain of the microgrid.
- Real-time Operating System (RTOS): For low-latency control and response.
- AI/ML Optimization Engine:
- Predictive Analytics: Forecasting renewable energy generation (based on weather, historical data) and factory load demand.
- Optimization Algorithms: (e.g., Reinforcement Learning, Mixed-Integer Linear Programming) to dynamically dispatch DERs, optimize battery charge/discharge cycles, and manage factory load shedding/shifting based on real-time energy prices, generation forecasts, and operational priorities.
- Anomaly Detection: Identifying abnormal energy consumption patterns that could indicate equipment malfunction or inefficiency.
- Industrial IoT (IIoT) Ecosystem:
- Smart Sensors: Embedded in machinery (motor current, conveyor speed, process variables), facility HVAC, lighting, and environmental systems to provide granular, real-time energy consumption data.
- Smart Meters: At sub-system levels within the factory for detailed energy consumption monitoring.
- IIoT Gateways: Collect and pre-process sensor data at the edge before sending it to the central controller or cloud.
- Communication Protocols:
- Industrial Protocols: Modbus TCP/IP, OPC UA, PROFINET, EtherNet/IP for communication between controllers, PLCs, and factory machinery.
- Energy-Specific Protocols: IEC 61850 for substation automation and DER communication, DNP3 for SCADA systems.
- Network Infrastructure: High-bandwidth, low-latency industrial Ethernet, TSN (Time-Sensitive Networking), 5G private networks for critical control data.
- Cloud Platform (for long-term analytics & fleet management):
- IoT Platform: (e.g., AWS IoT, Azure IoT, Google Cloud IoT) for data ingestion, device management, and secure communication.
- Big Data Analytics: For historical data analysis, long-term trend identification, and continuous improvement of AI models.
- Digital Twin: A virtual replica of the factory and microgrid, allowing simulation of different operational and energy scenarios.
- Human-Machine Interface (HMI) & Dashboards:
- Control Room Displays: Real-time visualization of microgrid status, energy flows, factory load, and operational KPIs.
- Energy Management System (EMS) Interface: For operators to set energy priorities, view forecasts, and intervene if necessary.
- Cybersecurity Measures:
- Network Segmentation: Isolating OT networks from IT networks.
- Secure Communication: Encryption and authentication for all data transfers.
- Anomaly Detection & IPS: As detailed in previous applications, integrated for overall system security.
Impact/ROI:
GridHarmony Industrial delivers significant and quantifiable benefits:
- Substantial Energy Cost Reduction (15-30%): By optimizing energy usage to leverage cheaper renewable sources, avoiding peak demand charges, and potentially selling excess power back to the grid.
- Enhanced Energy Resiliency & Reliability: Seamlessly transitions to islanded mode during grid outages, ensuring uninterrupted power for critical industrial processes, preventing costly downtime, and protecting sensitive equipment.
- Reduced Carbon Footprint (Significant): Maximizes the utilization of on-site renewable energy, reducing reliance on fossil fuel-based grid power and contributing to corporate sustainability goals.
- Increased Energy Independence: Lessens reliance on a fluctuating and potentially unreliable main utility grid.
- Optimized Resource Utilization: Intelligently manages energy storage (batteries), extending their lifespan through optimized charge/discharge cycles.
- Improved Operational Efficiency: Aligning production schedules with energy availability and cost, leading to smoother operations and reduced energy waste.
- Competitive Advantage: Demonstrates commitment to sustainability and resilience, appealing to environmentally conscious customers and investors.
- Data-Driven Decision Making: Provides granular insights into energy consumption patterns and microgrid performance, enabling continuous optimization.
Real-World Example:
Consider a large-scale automotive ancillary manufacturing plant in Visakhapatnam, Andhra Pradesh, India, producing critical components for electric vehicles (EVs). The plant has a significant energy footprint, including heavy machinery, robotics, and advanced painting lines. To meet its sustainability goals and ensure uninterrupted production (especially given potential grid instabilities), the plant has invested in an on-site microgrid consisting of rooftop solar panels, a medium-scale wind turbine, and a large battery energy storage system (BESS).
Before GridHarmony Industrial: The plant had a basic microgrid, but its integration with factory operations was rudimentary. It could switch to islanded mode during outages, but it couldn't intelligently optimize factory load against renewable generation. During cloudy days, they'd still import expensive grid power, and during sunny days with low factory demand, excess solar might be curtailed or inefficiently exported. Production schedules were rigid and didn't consider real-time energy costs or availability.
With GridHarmony Industrial (LubeSense AI as an integrated component for specific machinery):
- Real-time Microgrid Awareness: GridHarmony controllers continuously monitor the solar PV output, wind turbine generation, BESS state of charge, and real-time grid electricity prices (e.g., time-of-use rates from the discom).
- Intelligent Load Synchronization:
- Forecasting: GridHarmony's AI engine predicts solar generation for the next 24 hours (based on weather forecasts and historical patterns) and predicts the factory's energy demand (based on production schedules, historical consumption, and machine-specific data).
- Automated Balancing:
- During a period of high solar generation and low grid prices, GridHarmony will automatically prioritize powering all non-critical loads (e.g., charging forklifts, running HVAC at maximum efficiency, pre-heating some low-priority ovens) directly from solar. It might also use excess solar to charge the BESS to full capacity.
- If a cloudy spell is predicted or grid prices are expected to peak, GridHarmony will automatically signal the plant's MES to shift certain energy-intensive processes (e.g., a large batch paint curing cycle, or the charging of heavy-duty robotic batteries) to later, off-peak hours or to times when the BESS can efficiently discharge its stored renewable energy.
- If the main grid experiences an outage, GridHarmony's controllers seamlessly and instantaneously switch the factory to islanded mode. Simultaneously, it communicates with critical industrial controllers (PLCs, motor drives). It might temporarily reduce the speed of certain conveyor belts or dim non-essential lighting, while ensuring core EV component assembly lines and safety systems receive uninterrupted power from the microgrid and BESS. The system also instructs the BESS to prioritize discharge to meet immediate critical load.
- Optimized Asset Usage: The AI ensures the BESS is charged and discharged optimally, extending its lifespan and maximizing its economic value.
- Reduced Grid Dependence: The plant significantly reduces its reliance on the main grid, especially during peak demand, lowering its electricity bills and reducing exposure to grid instability.
Result:
The automotive ancillary plant in Visakhapatnam achieves a 25% reduction in its annual energy costs by maximizing renewable energy self-consumption and intelligently managing demand. Its energy resiliency improves dramatically, ensuring continuous production even during grid outages, thereby preventing millions of dollars in potential losses from downtime and missed production targets. The plant also significantly reduces its carbon emissions, contributing to a greener manufacturing footprint in Andhra Pradesh and enhancing its brand as a sustainable EV component supplier.
🚀 Ready to turn your passion for connected tech into real-world impact?
At Huebits, we don’t just teach IoT — we train you to build smart, scalable, and data-driven systems using the tech stacks powering today’s most innovative industries.
From edge devices to cloud platforms, you’ll gain hands-on experience designing end-to-end IoT architectures that collect, analyze, and respond in real time — built for deployment in cities, farms, factories, and homes.
🧠 Whether you're a student, aspiring IoT engineer, or future smart systems architect, our Industry-Ready IoT Program is your launchpad.
Master Python, Embedded C, MQTT, REST APIs, ESP32, Raspberry Pi, AWS IoT, Azure IoT Hub, and Grafana — all by building real-world IoT solutions that deliver results, not just data.
🎓 Next Cohort Starts Soon!
🔗 Join now and claim your seat in the IoT revolution powering tomorrow’s ₹1 trillion+ connected economy.
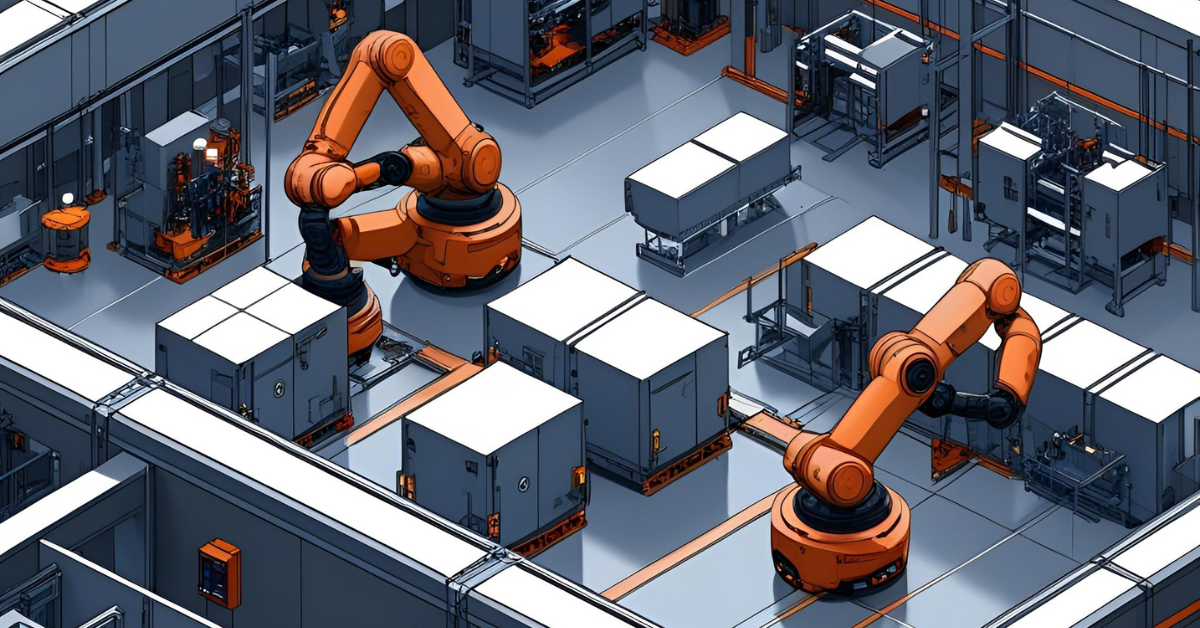
19.Autonomous Reconfiguration of Industrial Layouts
Application Name: FlexiFab Orchestrator
Overview:
FlexiFab Orchestrator pioneers the concept of Autonomous Reconfiguration of Industrial Layouts, transforming static factory floors into dynamic, adaptive production environments. This solution leverages a sophisticated ecosystem of smart cranes, autonomous mobile robots (AMRs), mobile workstations, and adaptive tooling that can intelligently reshuffle their physical positions and operational workflows. Driven by real-time data on changing production goals, fluctuating demand, material availability, and even unexpected equipment failures, FlexiFab Orchestrator's AI engine continuously optimizes the factory layout and material flow. It enables instant adaptation to new product lines, custom orders, or varying production volumes, minimizing manual retooling, eliminating rigid assembly lines, and achieving unprecedented levels of agility, efficiency, and responsiveness in modern manufacturing.
Use Case:
FlexiFab Orchestrator is highly beneficial for industries requiring rapid adaptation to market changes, producing high-mix/low-volume products, or dealing with frequent product redesigns and customization. Key use cases include:
- Automotive Industry (EV Manufacturing, Custom Vehicles):
- Modular Assembly Lines: Assembling different EV models or highly customized luxury vehicles on the same floor. FlexiFab can autonomously reconfigure welding stations, battery installation points, and final assembly cells for each vehicle as it moves through the factory.
- Flexible Body Shops: Re-arranging robotic welding cells to accommodate new body types or material changes without halting production for extensive retooling.
- Aerospace Manufacturing:
- Large Component Assembly: For aircraft wings or fuselage sections, FlexiFab can dynamically reposition tooling jigs, robotic riveting stations, and inspection gantries based on the specific section being built, optimizing workflow for unique geometries.
- Maintenance, Repair, and Overhaul (MRO): Reconfiguring hangar layouts to accommodate different aircraft types for maintenance, moving specialized equipment to the exact spot needed.
- Electronics Manufacturing (High-Mix/Low-Volume):
- Custom PCB Assembly: Adapting the layout of pick-and-place machines, reflow ovens, and inspection stations for different PCB designs or short production runs, minimizing changeover time.
- Flexible Device Assembly: Re-arranging modular assembly cells to produce different consumer electronics devices on the same line, moving components and tools as needed.
- Heavy Machinery Manufacturing (Agricultural, Construction):
- Large Component Handling: Utilizing smart cranes and AMRs to autonomously move and position massive engine blocks, chassis, or hydraulic components to available assembly points, optimizing the flow for different machinery models.
- Variable Production Batches: Adapting the assembly sequence and tooling setup for varying batch sizes of tractors, excavators, or harvesters.
- Furniture & Fixture Manufacturing (Custom Orders):
- Batch-of-One Production: Dynamically arranging woodworking stations, painting booths, and assembly areas to create highly customized furniture pieces efficiently, moving components between specialized workstations.
Tech Stack:
FlexiFab Orchestrator requires a sophisticated blend of robotics, AI, real-time sensing, and advanced software:
- Autonomous Mobile Robots (AMRs) / Mobile Workstations:
- Navigation & Mapping: LiDAR, cameras, ultrasonic sensors, and SLAM (Simultaneous Localization and Mapping) algorithms for autonomous navigation in dynamic environments.
- Payload Capacity & Manipulation: AMRs capable of transporting heavy components, entire workstations, or acting as mobile robotic manipulators.
- Swarm Intelligence: Algorithms for coordinating hundreds of AMRs to avoid collisions and achieve collective goals.
- Smart Cranes & Overhead Transport Systems:
- Precision Positioning: High-accuracy sensors (e.g., laser trackers, vision systems) for millimeter-level positioning of heavy loads.
- Autonomous Operation: Capable of picking up, transporting, and placing items/workstations without human intervention, integrating with AMR traffic.
- Load Balancing: Algorithms to distribute heavy lifting tasks efficiently across available cranes.
- Adaptive Tooling & Reconfigurable Jigs:
- Modular Fixturing: Tooling and jigs that can be quickly reassembled or adjusted using robotic grippers or automated mechanisms.
- Robotic End-Effectors: General-purpose or quickly interchangeable grippers and tools for robots that can handle various tasks.
- Automated Tool Changers: For robotic arms on mobile workstations.
- Real-time Sensing & Digital Twin:
- Environmental Sensors: LiDAR, 3D cameras, and depth sensors deployed across the factory floor to continuously map the environment, detect obstacles, and track the real-time positions of all movable assets.
- IoT Sensors on Assets: Monitoring status, battery levels, tool presence, and operational parameters of robots, AMRs, and workstations.
- Comprehensive Digital Twin: A dynamic, real-time virtual replica of the entire factory floor, including machine status, component locations, active production orders, and the current layout. This is the central brain for simulation and optimization.
- AI & Optimization Engine (The "Orchestrator"):
- Production Planning & Scheduling: Algorithms that translate high-level production goals (e.g., "produce 50 units of Product A, 20 of Product B by tomorrow") into detailed operational sequences and resource requirements.
- Dynamic Layout Optimization:
- Reinforcement Learning (RL): Training AI agents to learn optimal layout configurations and movement strategies based on simulated production scenarios and real-world performance data.
- Heuristic Algorithms/Genetic Algorithms: For rapid exploration of optimal layout options given constraints.
- Discrete Event Simulation (DES): To simulate proposed reconfigurations and predict their impact on throughput, bottlenecks, and efficiency before physical execution.
- Path Planning & Collision Avoidance: Advanced algorithms for AMRs and cranes to navigate complex, dynamic environments safely and efficiently.
- Resource Allocation: Dynamically assigning tasks and components to available mobile workstations and robotic cells.
- Anomaly Detection: Identifying unexpected movements, blockages, or equipment malfunctions that require re-planning.
- Central Control & Communication Platform:
- Industrial Connectivity: Low-latency, high-bandwidth networks (e.g., 5G Private Network, TSN-enabled Ethernet) for real-time communication between the orchestrator, AMRs, cranes, and other assets.
- MQTT/OPC UA: For robust data exchange.
- Fleet Management System: For coordinating and monitoring the health of all mobile assets.
- User Interface (UI) & Analytics:
- Intuitive Dashboard: Visualizing the real-time factory layout, active production flows, pending reconfigurations, and performance KPIs.
- Simulation & What-If Analysis: Tools for engineers to test new production scenarios or layout changes in the digital twin before deployment.
Impact/ROI:
FlexiFab Orchestrator delivers profound and multi-faceted ROI:
- Unprecedented Agility & Responsiveness: Enables manufacturers to adapt almost instantly to market changes, new product introductions, or demand fluctuations, achieving true "batch-of-one" or "mass customization" capabilities.
- Significant Cost Reduction (15-30%):
- Minimized Changeover Time & Cost: Eliminates lengthy, expensive manual retooling and physical reconfigurations.
- Optimized Space Utilization: Dynamically adjusting layouts means less wasted floor space for idle equipment or buffer inventory.
- Increased Productivity: Eliminating bottlenecks and optimizing flow boosts overall throughput.
- Reduced Labor for Reconfiguration: Automation frees up skilled personnel for higher-value tasks.
- Higher Throughput & Efficiency (up to 20%): Continuous optimization of material flow and workstation arrangement directly translates to faster production cycles.
- Improved Quality: Optimal layout can reduce material handling damage and ensure consistent process flow.
- Enhanced Resilience: The factory can autonomously adapt to unexpected disruptions (e.g., a machine breakdown) by dynamically rerouting production or reassigning tasks.
- Accelerated New Product Introduction (NPI): Rapidly test and scale up production for new products without disrupting existing lines or building new facilities.
- Future-Proof Manufacturing: A factory that can reconfigure itself is inherently more adaptable to future technological advancements and market demands.
- Data-Driven Optimization: Provides rich data for continuous improvement of production processes and layout strategies.
Real-World Example:
Consider a major shipbuilding yard in Visakhapatnam, Andhra Pradesh, India, which undertakes diverse projects ranging from naval vessels to large cargo ships and specialized offshore platforms. Each project requires unique assembly sequences, specialized tooling, and handling of massive, uniquely shaped components. Traditionally, the shipyard relied on fixed assembly bays, which were reconfigured manually for each new vessel type – a slow, labor-intensive, and extremely costly process that often caused significant delays.
Before FlexiFab Orchestrator: When a new type of vessel (e.g., an LNG carrier vs. a frigate) entered the main assembly hall, cranes, temporary jigs, welding stations, and material staging areas had to be manually repositioned. This involved hours, sometimes days, of planning, moving heavy equipment with forklifts, re-routing power, and physical marking, leading to long periods of non-production in the assembly hall. Material flow was often suboptimal due to static layouts.
With FlexiFab Orchestrator:
- Digital Twin of Shipyard: The entire assembly hall, including all movable assets, is represented as a dynamic digital twin within FlexiFab Orchestrator. This twin is continuously updated with real-time locations of components, vessel sections, and all mobile resources.
- Smart Cranes & Mobile Workstations: The shipyard's massive gantry cranes are upgraded with precision positioning sensors and autonomous control. Mobile workstations, equipped with robotic welding arms, inspection tools, or painting systems, are built on heavy-duty AMRs.
- Dynamic Production Goal: A new naval vessel contract comes in, requiring a different assembly sequence and specialized tooling than the previous cargo ship. The production planning team inputs the new vessel's blueprint and production goals into FlexiFab Orchestrator.
- Autonomous Reconfiguration:
- AI Simulation: FlexiFab's AI engine instantly runs simulations in its digital twin, analyzing the optimal placement of various vessel sections, the most efficient path for components to flow, and the ideal positioning for mobile welding stations, inspection gantries, and painting robots for this specific vessel type.
- Orchestrated Movement: The AI then issues commands to:
- Smart Cranes: Autonomously pick up large, pre-fabricated vessel blocks and position them precisely in the most efficient assembly sequence within the hall.
- Mobile Workstations (AMRs): Simultaneously, the mobile welding stations, equipped with robotic arms, autonomously move to their optimal positions around the vessel section, receiving their specific welding parameters for that hull plate. Other AMRs might bring specialized tools or components directly to these mobile workstations.
- Adaptive Tooling: Any reconfigurable tooling jigs automatically adjust their dimensions and clamping points based on the digital blueprint of the current section being assembled.
- Real-time Adaptation: If a specific mobile workstation experiences a temporary fault, the orchestrator instantly reroutes incoming components to an available alternative workstation or dispatches another AMR with a similar capability, minimizing disruption.
- Continuous Optimization: As assembly progresses, FlexiFab continuously monitors the flow, detecting potential bottlenecks or underutilized resources, and subtly adjusts the positioning or task assignments of mobile assets to maintain optimal efficiency.
Result:
The Visakhapatnam shipbuilding yard experiences a 60% reduction in the time and cost associated with factory layout reconfigurations, translating into significantly faster project completion times for new vessels. This leads to millions of dollars in increased revenue from being able to take on more diverse and complex shipbuilding contracts. The shipyard achieves unprecedented agility, able to switch between different vessel types with minimal downtime, making it highly competitive in the global shipbuilding market and strengthening India's defense and maritime capabilities.
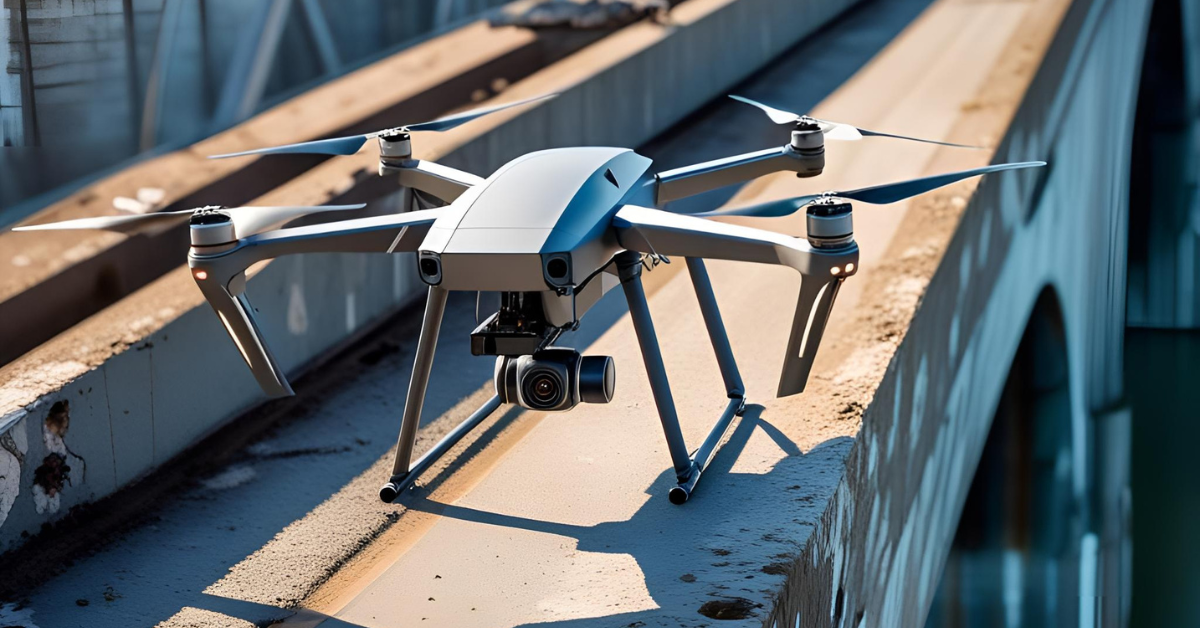
20.Drone-Assisted Infrastructure Audits
Application Name: SkyInspect AI
Overview:
SkyInspect AI represents a paradigm shift in infrastructure auditing and maintenance. It utilizes Drones equipped with advanced IIoT payloads for comprehensive thermal, structural, and visual scans of critical industrial assets. These intelligent drones are not merely flying cameras; they are mobile IIoT nodes that capture high-resolution data from hard-to-reach or hazardous areas. This rich, multi-modal data is then subjected to real-time upload and AI-powered analysis, enabling immediate fault flagging and predictive insights. SkyInspect AI eliminates the need for manual, time-consuming, and dangerous inspections, transforming reactive maintenance into a proactive, data-driven strategy, ensuring infrastructure integrity and extending asset lifespans.
Use Case:
SkyInspect AI is invaluable for any industry managing extensive, complex, or high-risk infrastructure where traditional inspection methods are costly, time-consuming, or unsafe. Key use cases include:
- Power & Utilities (Transmission Lines, Substations, Wind Turbines):
- Power Line Inspection: Drones with thermal cameras identify overheating insulators, frayed cables, loose connections, or vegetation encroachment that could cause outages, even before visible signs appear. Visual cameras detect structural damage to towers.
- Substation Audits: Inspecting transformers for hotspots, circuit breakers for wear, and general structural integrity of substation components, often without the need for power shutdown.
- Wind Turbine Blade Inspection: High-resolution cameras and LiDAR map defects like cracks, erosion, or delamination on turbine blades, detecting issues early to prevent catastrophic failures and optimize energy generation.
- Oil & Gas (Pipelines, Storage Tanks, Offshore Rigs):
- Pipeline Integrity Monitoring: Drones equipped with visual, thermal, and potentially gas leak detection payloads patrol vast stretches of pipelines, identifying corrosion, leaks, unauthorized taps, and environmental damage.
- Storage Tank Inspection: Inspecting tank roofs, walls, and foundations for deformities, corrosion, or insulation defects that could lead to leaks or structural failure. Thermal cameras detect liquid levels and potential sludge buildup.
- Offshore Platform Audits: Safely inspecting flares, derricks, and structural elements of offshore rigs for corrosion, fatigue, or damage in harsh marine environments, reducing the need for dangerous human climbs or costly scaffolding.
- Transportation Infrastructure (Bridges, Railways, Ports):
- Bridge Inspection: Drones capture detailed visual and 3D LiDAR data of bridge decks, piers, abutments, and undersides to identify cracks, spalling, corrosion, or scour. Thermal cameras detect water ingress or delamination.
- Railway Track Surveillance: Monitoring tracks for rail defects, ballast issues, vegetation encroachment, and critical infrastructure like signals and overhead lines.
- Port Infrastructure: Inspecting cranes, quay walls, and storage facilities for structural damage, wear, or operational inefficiencies.
- Manufacturing & Industrial Facilities (Roofs, Stacks, Large Structures):
- Building Envelope Inspection: Thermal drones detect insulation gaps, moisture ingress, or roof leaks in large factory buildings, improving energy efficiency and preventing structural damage.
- Stack & Chimney Inspections: Safely inspecting tall industrial stacks for cracks, corrosion, and structural integrity.
- Mining Operations (Tailings Dams, Conveyor Systems):
- Tailings Dam Monitoring: Regularly assessing the structural integrity of tailings dams for signs of seepage, cracks, or erosion.
- Conveyor System Inspection: Identifying worn rollers, misaligned belts, or motor overheating.
Tech Stack:
SkyInspect AI relies on a sophisticated fusion of drone technology, IIoT, and advanced analytics:
- Advanced Drone Platforms:
- Industrial-grade UAVs: Robust, stable drones with high payload capacity, extended flight times, and often RTK/PPK GPS for centimeter-level positioning accuracy (e.g., DJI Matrice series, Inspired Flight, Autel Enterprise).
- Autonomous Flight Capabilities: Pre-programmed flight paths, waypoints, and automated takeoff/landing; obstacle avoidance systems (LiDAR, optical, ultrasonic).
- IIoT Payloads (Sensors):
- High-Resolution Visual Cameras (RGB): 4K+ resolution for detailed visual inspection, often with optical zoom capabilities to inspect distant components.
- Thermal/Infrared (IR) Cameras: For detecting heat anomalies, hotspots, insulation defects, electrical faults, and liquid levels (e.g., FLIR thermal sensors, DJI Zenmuse H20T).
- LiDAR (Light Detection and Ranging) Scanners: Creates precise 3D point clouds for structural analysis, volumetric measurements, deformation detection, and accurate modeling of infrastructure (e.g., YellowScan, DJI Zenmuse L2).
- Gas Leak Detection Sensors: Tunable diode laser absorption spectroscopy (TDLAS) or similar sensors for methane/hydrocarbon leak detection in oil & gas.
- Multi-spectral/Hyperspectral Cameras: For vegetation health analysis around infrastructure or detecting subtle material changes.
- Ultrasonic & Acoustic Sensors: For detecting internal defects or subtle sounds of equipment malfunction.
- Edge Computing & Real-time Processing:
- Onboard AI Processors: Drones equipped with powerful edge GPUs/CPUs to perform immediate data processing, filtering, and initial AI inference (e.g., basic object detection, anomaly flagging) during flight.
- Real-time Data Streaming: High-bandwidth, low-latency wireless communication (e.g., 5G/LTE cellular modules, proprietary radio links) for live video feeds and critical sensor data transmission from the drone to a ground station or cloud.
- Cloud-based Data Platform & AI Analytics:
- IoT Platform: (e.g., AWS IoT, Azure IoT Hub) for secure ingestion and management of massive volumes of drone data.
- Data Lake/Object Storage: For storing raw images, videos, thermal data, LiDAR point clouds, and metadata.
- AI/Machine Learning Core:
- Computer Vision (CV): Deep learning models (CNNs, transformers) for automated defect detection (cracks, corrosion, spalling, rust), object recognition (insulators, bolts, structural members), and change detection (comparing current state to historical data).
- Thermal Image Analysis: AI models to analyze temperature patterns and identify abnormal thermal signatures.
- 3D Model Analysis: Algorithms to process LiDAR point clouds and photogrammetry models for precise measurements, deformation analysis, and structural integrity assessment.
- Predictive Analytics: Forecasting potential failure points or maintenance needs based on detected deterioration rates and environmental factors.
- Geospatial Information Systems (GIS): For mapping identified faults onto geographical coordinates and integrating with existing asset management systems.
- Communication & Connectivity:
- Cellular (4G/5G LTE): For long-range, real-time data upload, especially for linear infrastructure like pipelines or power lines.
- Dedicated Radio Links: For robust control and telemetry, particularly in remote areas or where cellular coverage is poor.
- Mesh Networks: For coordinating multiple drones or ground robots in complex industrial sites.
- User Interface & Reporting:
- Intuitive Dashboards: Web-based or mobile applications visualizing 2D/3D models of inspected infrastructure, annotated with detected faults, severity ratings, and actionable recommendations.
- Automated Report Generation: Customizable reports for regulatory compliance, maintenance planning, and stakeholder communication.
- Integration APIs: For seamless connectivity with Enterprise Asset Management (EAM), Computerized Maintenance Management Systems (CMMS), and GIS platforms.
Impact/ROI:
SkyInspect AI delivers a compelling ROI for infrastructure owners and operators:
- Enhanced Safety (Significant): Eliminates the need to send human inspectors into hazardous environments (e.g., working at height, confined spaces, high-voltage areas, unstable structures), drastically reducing risks, injuries, and associated liabilities.
- Dramatic Cost Reduction (20-50%):
- Reduced labor costs (fewer inspectors, less scaffolding, no heavy machinery for access).
- Minimized equipment rental and operational expenses (helicopters, cranes).
- Lower insurance premiums due to reduced risk.
- Faster Inspection Times (Up to 70% reduction): Drones can cover vast areas and collect data much more quickly than traditional methods, leading to less operational downtime for the infrastructure itself (e.g., not needing to shut down a power line).
- Superior Data Quality & Precision: High-resolution imagery, thermal data, and 3D models provide an unparalleled level of detail and objective, consistent data, allowing for the detection of subtle defects often missed by human eyes.
- Proactive & Predictive Maintenance: Real-time fault flagging and AI-driven analysis enable a shift from reactive repairs to predictive, condition-based maintenance, preventing catastrophic failures and extending asset lifespan.
- Improved Compliance & Auditability: Comprehensive, documented digital records of inspections aid in regulatory compliance and provide clear audit trails.
- Reduced Operational Downtime: By identifying issues early, major shutdowns for repairs can be avoided or scheduled efficiently, minimizing disruption.
- Environmental Benefits: Reduced reliance on fossil fuel-powered vehicles (helicopters, bucket trucks) and preventing leaks/spills.
Real-World Example:
Consider the extensive network of oil and gas pipelines stretching across the coastal and industrial belts of Visakhapatnam, Andhra Pradesh, India. These pipelines transport crude oil, natural gas, and refined products from port facilities and refineries to various industrial users and distribution points. Regular inspection is critical for safety, environmental protection, and preventing costly leaks or explosions, but traditional methods (walking patrols, manned helicopter flyovers) are slow, expensive, and often miss subtle issues.
Before SkyInspect AI: Pipeline inspections were labor-intensive. Ground crews would manually walk sections, often missing remote areas or small leaks. Manned helicopters provided aerial views but were expensive, had limited flight times, and their visual inspections were less precise than dedicated sensors. Detecting subsurface leaks or minor corrosion required physical access and often didn't happen until a visible leak occurred.
With SkyInspect AI:
- Specialized Drone Fleet: The oil and gas company deploys a fleet of SkyInspect AI drones equipped with:
- High-resolution RGB cameras for visual structural integrity.
- High-sensitivity thermal cameras for detecting temperature anomalies indicating leaks or insulation breakdown.
- LiDAR sensors for creating precise 3D models of the pipeline and surrounding terrain to detect ground deformation or subtle shifts.
- Methane gas detection payloads for identifying even small, invisible gas leaks.
- Automated Flight Paths: The drones are programmed with precise flight paths covering hundreds of kilometers of pipeline. They fly autonomously at optimized altitudes and speeds, capturing continuous streams of data.
- Real-time Upload & Edge Processing: During flight, the drone's onboard edge processor immediately analyzes the sensor data. For example, if the methane sensor detects a concentration spike, or if the thermal camera identifies a localized hotspot, this information is immediately flagged. Critical data (e.g., high-resolution thermal image of a potential leak) is then streamed in real-time via a 4G/5G cellular connection (or satellite in remote areas) to a central control room in Visakhapatnam.
- AI-Powered Fault Flagging:
- In the cloud-based SkyInspect AI platform, computer vision models automatically scan the visual imagery for signs of corrosion, cracks, vegetation encroachment, or unauthorized construction near the pipeline.
- Thermal analytics algorithms pinpoint unusual heat signatures, distinguishing between environmental heat and anomalies indicative of leaks or stressed components.
- LiDAR data is processed to detect ground subsidence or unexpected changes in the pipeline's position, indicating potential stress or damage.
- The system cross-references data points: if a methane reading is high and there's a thermal anomaly, the fault confidence level increases dramatically, triggering a high-priority alert.
- Actionable Insights: The control room receives immediate alerts on a dashboard, pinpointing the exact GPS coordinates of potential issues. They can instantly view the high-resolution visual and thermal imagery. Based on the flagged faults and their severity, the system can automatically:
- Generate a work order for a ground crew to investigate a specific GPS location.
- Recommend a repair schedule.
- Provide a comprehensive audit report for regulatory compliance.
Result:
The oil and gas company in Visakhapatnam achieves a 40% reduction in inspection costs by replacing manual and helicopter-based methods. They see a significant increase in safety by removing personnel from hazardous environments. Crucially, the ability to perform real-time, granular fault detection leads to the early identification of leaks and structural issues, preventing costly environmental damage, production shutdowns, and ensuring continuous, safe operation of their vital pipeline infrastructure across Andhra Pradesh.
Closing Line: A Deeper Look into the Smart Factory of 2025
The smart factory of 2025 won’t just be automated — it’ll be self-aware, adaptive, and untouchable. If you’re still waiting for the "future of industry," you’re already obsolete. IIoT isn’t an upgrade. It’s an uprising. Either sync or sink.
This bold declaration encapsulates the transformative power of the Industrial Internet of Things (IIoT) and advanced technologies discussed through applications like GridGuardian AI, VisionPro Assist, QuantumFortress Industrial, SentinelEdge AI, AutoConnect Pro, SynapseChain, GridHarmony Industrial, FlexiFab Orchestrator, and SkyInspect AI. Here's a breakdown of the implied details:
- "The smart factory of 2025 won’t just be automated..."
- Implied Detail: Traditional automation focuses on repetitive tasks and programmed sequences. While efficient, it lacks the ability to respond intelligently to dynamic conditions, learn from data, or manage complex interdependencies without human intervention. The smart factory moves beyond merely performing tasks automatically.
- "...it’ll be self-aware..."
- Implied Detail: This refers to the pervasive sensing and data collection capabilities provided by IIoT devices (e.g., SynapseChain's cognitive sensors, SentinelEdge AI's microfluidic sensors, GridHarmony's microgrid monitoring).
- Why? Machines and systems will have a deep, real-time understanding of their own operational status, health, and environmental context.
- How? Through continuous data streams from connected assets (e.g., friction detection in LubeSense AI, thermal scans from SkyInspect AI drones, real-time demand monitoring in GridGuardian AI), AI/ML algorithms analyze this data to form an accurate, up-to-the-minute picture of the entire industrial ecosystem, enabling predictive insights and internal diagnostics.
- "...adaptive..."
- Implied Detail: This highlights the ability to dynamically adjust to changing internal and external conditions.
- Why? Unlike rigid, fixed production lines, the adaptive factory can reconfigure, reschedule, and optimize operations on the fly.
- How? Driven by AI and real-time data, systems like FlexiFab Orchestrator autonomously reshuffle layouts based on new production goals or component availability. GridHarmony Industrial intelligently auto-balances energy usage based on renewable generation. SynapseChain's cognitive engine predicts delays and suggests route optimizations, allowing the supply chain to flex and respond to disruptions.
- "...and untouchable."
- Implied Detail: This emphasizes the unprecedented level of security and resilience built into the very fabric of the industrial network.
- Why? In an increasingly digital world, the "digital fortress" concept is paramount to protect against cyber threats, physical intrusions, and tampering.
- How? QuantumFortress Industrial secures data with next-gen, quantum-resistant encryption. SentinelX Industrial Guard employs cyber-physical intrusion prevention, detecting anomalies across both IT and OT networks. AutoConnect Pro ensures "zero-touch" secure onboarding with blockchain validation, preventing unauthorized devices from ever compromising the system. This collective defense makes the industrial environment robust against even sophisticated attacks.
- "If you’re still waiting for the 'future of industry,' you’re already obsolete."
- Implied Detail: This is a direct challenge to complacency. The technologies described are not distant visions; they are here and being implemented now.
- Why? Organizations that hesitate risk being outmaneuvered by competitors who embrace these capabilities for efficiency, cost savings, and resilience. Waiting means falling behind on productivity, sustainability, and security.
- "IIoT isn’t an upgrade. It’s an uprising."
- Implied Detail: This emphasizes the revolutionary, rather than evolutionary, nature of IIoT.
- Why? An "upgrade" implies a linear improvement; an "uprising" signifies a fundamental shift, a complete transformation of how industries operate. IIoT isn't just about making existing processes slightly better; it's about enabling entirely new paradigms of operation, efficiency, and intelligence that were previously impossible. It's a bottom-up revolution driven by data from every corner of the factory.
- "Either sync or sink."
- Implied Detail: A final, stark warning about the binary choice facing industrial enterprises.
- Why? To "sync" means to align with, integrate, and leverage these new IIoT-driven capabilities. To "sink" implies falling into obsolescence, being unable to compete on cost, agility, quality, or security in the new industrial landscape. It's a call to immediate action, recognizing the critical juncture at which the industry stands.
In essence, the closing line details the culmination of the capabilities described in each application, painting a picture of an industrial future that is highly intelligent, responsive, secure, and fundamentally transformed by IIoT.
🚀 About This Program — Internet of Things (IoT)
By 2030, it won’t be just people online — everything will be. From smart homes to connected cities, autonomous farms to self-healing factories, the Internet of Things (IoT) is becoming the digital nervous system of our world. Every light that adapts, every machine that predicts failure, every wearable that senses vitals — it’s all IoT, and it’s all real.
🛠️ The problem? Most IoT training is stuck in 2015. Boring dashboards. Cookie-cutter Arduino kits. Zero context for production-scale systems. The industry doesn’t need tinkerers — it needs systems engineers, data-driven architects, and full-stack IoT builders who can code, connect, and deploy across the entire spectrum — from edge devices to the cloud.
🔥 That’s where Huebits rewrites the rulebook.
We don’t train you to understand IoT.
We train you to build intelligent, connected systems that solve real-world problems.
Welcome to a 6-month, hands-on, Industry-Ready IoT Program — built to make you deployment-ready from Day One. Whether it’s building smart sensor networks, deploying AI at the edge, or creating cloud-connected automation systems, this program gives you the power to architect the future.
From mastering Embedded C, Python, and MQTT, to working with ESP32, Raspberry Pi, STM32, and deploying live systems with AWS IoT, Azure IoT Hub, and Grafana — we turn your curiosity into capabilities.
🎖️ Certification That Speaks Tech
Graduate with a Huebits-Certified IoT Engineer Credential, validated by tech leaders, IoT startups, and enterprise partners. This isn’t some paper souvenir — it’s industry-backed proof that you can build, optimize, and ship end-to-end IoT systems at scale.
📌 Why This Program Hits Harder:
✅ Real-World Edge-to-Cloud Projects
✅ Hands-on Hardware & Sensor Labs
✅ Live Debugging Sessions + Firmware Flashing
✅ LMS Access for One Full Year
✅ Job Guarantee After Successful Completion
💥 Your future team doesn’t want textbook definitions of MQTT or GPIO — they want someone who can get a fleet of devices online, secured, and generating business value in hours, not weeks.
Let’s build that engineer. Let’s build you.
🎯 Join Huebits’ Industry-Ready IoT Program
and shape the world — one smart device, one data packet at a time.
🔥 "Take Your First Step into the Internet of Things (IoT) Revolution!"
Ready to build the smart, connected systems that drive tomorrow’s homes, cities, farms, and industries?
Join the Huebits Industry-Ready IoT Program and gain hands-on experience with sensors, microcontrollers, IoT protocols, edge computing, and cloud platforms — using the exact tech stack trusted by leading IoT companies worldwide.
✅ Live Mentorship | 🌐 Real-World Projects | 📶 Career-Focused IoT Curriculum